Multiphase motor channel fault ride-through operation control method
A multi-phase motor and fault ride-through technology, applied in the field of communication, can solve problems such as overcurrent or overvoltage, fault shutdown, inrush current, etc.
- Summary
- Abstract
- Description
- Claims
- Application Information
AI Technical Summary
Problems solved by technology
Method used
Image
Examples
Embodiment 1
[0057] figure 1 Shown is a general diagram of the control method of a basic embodiment of the present invention.
[0058] A multi-phase motor channel fault ride-through operation control method, based on multiple converter channels connected to the bridge arms and windings of the multi-phase motor, including overcurrent protection for the AC side of the remaining channel inverter (ie, the motor winding side), The voltage stabilization control of the DC side of the remaining channel inverter, and the implementation of magnetic field compensation control of the multiphase motor by the remaining channel inverter during the fault ride-through transition process.
[0059] The overcurrent protection on the AC side of the inverter (that is, the motor winding side) uses an active shunt circuit to provide a path for the transient impact surge current, so that the impact surge current flowing through the stator winding of the remaining non-fault channel is transferred from the inverter ...
Embodiment 2
[0064] figure 2 A further example of Example 1 is shown. The difference with embodiment 1 is:
[0065] The shunt circuit is an active topology composed of multi-phase (the number of phases is the number of phases of one channel) fully-controlled power switching devices and current limiting resistors. This topology can be a multi-phase power switching tube such as a bidirectional insulated gate bipolar type Transistor (IGBT) anti-parallel bidirectional switch structure. The controller of the shunt circuit of each channel uses the stator winding current i of the channel ac As an input, if the winding current is lower than the inverter capacity safety lower limit threshold current I ac_L , the switch tube of the shunt circuit is blocked, the shunt circuit is closed, and the inverter works, if the winding current is higher than or equal to the safety upper limit threshold current I of the inverter capacity ac_H , the switch tube of the shunt circuit is triggered, the shunt ci...
Embodiment 3
[0068] Embodiment 3 is a further embodiment of Embodiment 1. The difference with embodiment 1 is:
[0069] The energy storage circuit is provided with a voltage-type energy storage medium (supercapacitor or chemical battery, etc.), and uses a three-level multiple phase-shifting DC bidirectional voltage source converter as the energy conversion control interface between the DC bus and the energy storage medium, reducing Switching device voltage and current stress, improved ripple filtering quality, smaller filters, and fault tolerant operation.
PUM
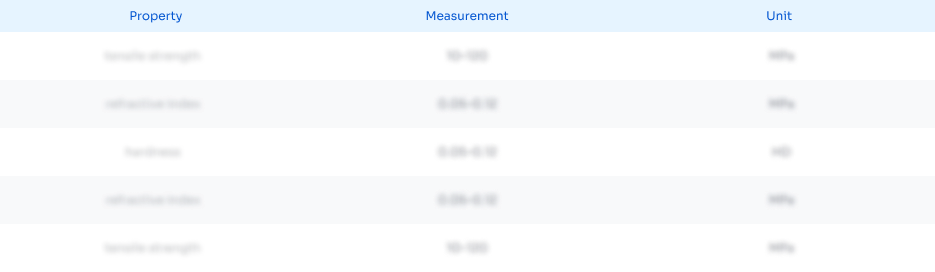
Abstract
Description
Claims
Application Information

- Generate Ideas
- Intellectual Property
- Life Sciences
- Materials
- Tech Scout
- Unparalleled Data Quality
- Higher Quality Content
- 60% Fewer Hallucinations
Browse by: Latest US Patents, China's latest patents, Technical Efficacy Thesaurus, Application Domain, Technology Topic, Popular Technical Reports.
© 2025 PatSnap. All rights reserved.Legal|Privacy policy|Modern Slavery Act Transparency Statement|Sitemap|About US| Contact US: help@patsnap.com