Metal carbide catalyst for catalyzing a CFC-113a hydrogenation coupling reaction and preparation method and application thereof
A metal carbide, cfc-113a technology, applied in the field of metal carbide catalyst and its preparation, can solve the problems of low conversion rate and selectivity, high yield, and achieve the effect of high catalytic stability
- Summary
- Abstract
- Description
- Claims
- Application Information
AI Technical Summary
Problems solved by technology
Method used
Image
Examples
Embodiment 1
[0022] Grind ferric nitrate nonahydrate and oxalic acid aqueous solution with a molar ratio of 1:3 into a yellow viscous liquid in an agate mortar (the concentration of oxalic acid aqueous solution is 30wt%, and the molar ratio of ferric nitrate nonahydrate and oxalic acid is 1:3) , to obtain ferric oxalate solution. After the ferric oxalate solution is dried at 100°C to remove moisture, it is calcined in a tube furnace under a CO atmosphere. The calcining temperature is 500°C, and the CO volume flow rate is 80mL / min. Promptly obtain the metal carbide catalyst (the metal carbide catalyst prepared in this embodiment is iron carbide), the XRD pattern of the metal carbide catalyst is as follows figure 1 shown, from figure 1 It can be seen that the structure of the catalyst presents the crystalline structure of iron carbide.
[0023] Take 2mL of the above-prepared iron carbide catalyst in the constant temperature zone of a reaction tube with an inner diameter of 8mm, raise the t...
Embodiment 2
[0025] Ruthenium trichloride and formic acid aqueous solution with a molar ratio of 1:3 were ground into a viscous liquid in an agate mortar (the concentration of formic acid aqueous solution was 40wt%, and the molar ratio of ruthenium trichloride and formic acid was 1:3), to obtain Solution A. After solution A was dried at 120°C to remove moisture, it was fired in a tube furnace at 350°C for 7 hours in a carbon-containing atmosphere, and the gas in the carbon-containing atmosphere was CH 4Mixed gas with diluent, CH 4 The volume flow rate is 20mL / min, the diluent gas is nitrogen and the volume flow rate is 40 mL / min. After the calcination is completed, the tablet is formed, and the metal carbide catalyst is obtained by sieving under 60-100 mesh (the metal carbide catalyst prepared in this embodiment for ruthenium carbide).
[0026] The process of using the metal carbide catalyst prepared in this example to catalyze the hydrocoupling reaction of CFC-113a was repeated in Examp...
Embodiment 3
[0028] Grind cobalt carbonate and citric acid aqueous solution with a molar ratio of 1:3 into a viscous liquid in an agate mortar (the concentration of citric acid aqueous solution is 40wt%, and the molar ratio of cobalt carbonate and citric acid is 1:3), and then Add 2wt% potassium nitrate and re-grind into a viscous liquid (based on the total amount of cobalt carbonate, citric acid and potassium nitrate as raw materials, the amount of potassium nitrate added is 2wt%) to obtain solution B. After solution B was dried at 120°C to remove moisture, it was fired in a tube furnace at 450°C for 1 hour in a carbon-containing atmosphere. The gas in the carbon-containing atmosphere was a mixture of carbon-containing gas and diluent gas. The carbon-containing gas was CO and CO 2 Mixed gas, CO and CO 2 The volume flow rate is 20mL / min, the diluent gas is nitrogen and the flow rate is 70 mL / min, after the calcination is completed, it is pressed into tablets, and sieved under 60-100 mesh ...
PUM
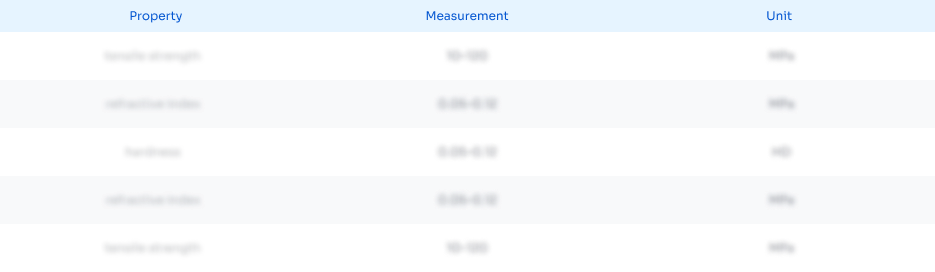
Abstract
Description
Claims
Application Information

- Generate Ideas
- Intellectual Property
- Life Sciences
- Materials
- Tech Scout
- Unparalleled Data Quality
- Higher Quality Content
- 60% Fewer Hallucinations
Browse by: Latest US Patents, China's latest patents, Technical Efficacy Thesaurus, Application Domain, Technology Topic, Popular Technical Reports.
© 2025 PatSnap. All rights reserved.Legal|Privacy policy|Modern Slavery Act Transparency Statement|Sitemap|About US| Contact US: help@patsnap.com