An aluminum alloy fusion welding back face fusion width detection method with a pseudo edge
A detection method, aluminum alloy technology, applied in image analysis, instrumentation, calculation, etc., can solve the problems of detection error of back fusion width, affect the control accuracy of closed-loop control, and cannot effectively distinguish false edges from real edges, etc., and achieve simple programming , easy-to-achieve effects
- Summary
- Abstract
- Description
- Claims
- Application Information
AI Technical Summary
Problems solved by technology
Method used
Image
Examples
Embodiment Construction
[0035] Embodiments of the present invention are described below through specific examples, and those skilled in the art can easily understand other advantages and effects of the present invention from the content disclosed in this specification. The present invention can also be implemented or applied through other different specific implementation modes, and various modifications or changes can be made to the details in this specification based on different viewpoints and applications without departing from the spirit of the present invention.
[0036] The test platform of the inventive method is as figure 2 As shown, it includes Panasonic 400GE2 welding machine, WAT-902H3 ultra-low illumination black and white industrial camera, USB2813A data acquisition card, 6061 aluminum alloy, and the plate thickness is 4mm. The required image of the back weld seam of aluminum alloy fusion welding is collected through the following process: the industrial camera and the auxiliary light ...
PUM
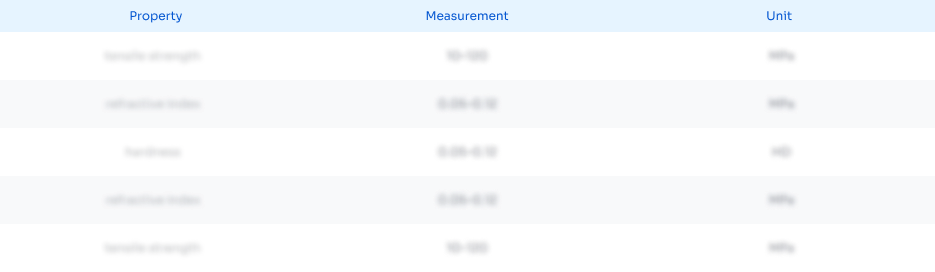
Abstract
Description
Claims
Application Information

- R&D
- Intellectual Property
- Life Sciences
- Materials
- Tech Scout
- Unparalleled Data Quality
- Higher Quality Content
- 60% Fewer Hallucinations
Browse by: Latest US Patents, China's latest patents, Technical Efficacy Thesaurus, Application Domain, Technology Topic, Popular Technical Reports.
© 2025 PatSnap. All rights reserved.Legal|Privacy policy|Modern Slavery Act Transparency Statement|Sitemap|About US| Contact US: help@patsnap.com