An in-situ mineralization dyeing process for polyester disperse dyes
A technology of disperse dyes and in-situ mineralization, which is applied in the field of dyeing technology, can solve the problems of increasing sewage discharge, achieve the effects of reducing damage, improving color fastness, and reducing reduction and cleaning links
- Summary
- Abstract
- Description
- Claims
- Application Information
AI Technical Summary
Problems solved by technology
Method used
Image
Examples
preparation example Construction
[0055] The preparation method of disperse dyeing post-treatment auxiliary agent YBD is characterized in that it is specifically prepared according to the following steps:
[0056] Step 1. Weigh raw materials according to mass percentage: polyacrylamide 0.001% to 5%, polyaluminum chloride 0.001% to 2.5%, sulfuric acid polyacrylamide 0.001% to 5%, sodium sulfate 0.001% to 3%, formamide 0.001%~10%, fatty alcohol polyoxyethylene ether 0.001%~15%, carboxymethyl cellulose 0.001%~3%, sodium alkylsulfonate 1.0%~10%, long chain sodium amidobenzenesulfonate 1.0% ~10%, sodium edetate 0.001% ~ 25%, pure water 11.5% ~ 97.992%, the total content of the above components is 100%;
[0057] Step 2, heating the pure water weighed in step 1 to 45°C-55°C;
[0058] Step 3, the polyacrylamide weighed in step 1, polyaluminum chloride, polyacrylamide sulfate, sodium sulfate, formamide, fatty alcohol polyoxyethylene ether, carboxymethyl cellulose, sodium alkylsulfonate, long Sodium chain amidobenzene...
Embodiment 1
[0092] Preparation of disperse dyeing post-treatment auxiliary YBD;
[0093] Disperse dyeing post-processing auxiliary YBD, composed of the following substances by mass percentage: polyacrylamide 3%, polyaluminum chloride 2%, sulfuric acid polyacrylamide 0.5%, sodium sulfate 1%, formamide 1%, fatty alcohol poly Oxyethylene ether 0.8%, carboxymethyl cellulose 0.2%, sodium alkylsulfonate 1.2%, long-chain amidobenzenesulfonate sodium 0.8%, sodium edetate 1.5%, pure water 88%, the above components The sum of the contents is 100%; the weighed polyacrylamide, polyaluminum chloride, sulfuric acid polyacrylamide, sodium sulfate, formamide, fatty alcohol polyoxyethylene ether, carboxymethyl cellulose, sodium alkylsulfonate, Sodium long-chain amidobenzenesulfonate and sodium ethylenediaminetetraacetate are added together into pure water at a temperature of 45°C to 55°C, and after stirring evenly, the post-treatment auxiliary YBD for disperse dyeing is obtained;
[0094] Preparation of ...
Embodiment 2
[0114] Preparation of disperse dyeing post-treatment auxiliary YBD;
[0115] Disperse dyeing post-treatment auxiliary YBD is composed of the following substances by mass percentage: polyacrylamide 0.06%, polyaluminum chloride 0.2%, sulfuric acid polyacrylamide 0.55%, sodium sulfate 0.5%, formamide 0.8%, fatty alcohol poly Oxyethylene ether 0.6%, carboxymethyl cellulose 0.01%, sodium alkyl sulfonate 1%, long-chain amidobenzene sulfonate sodium 1.2%, sodium edetate 0.08%, pure water 95%, the above components The sum of the contents is 100%; the weighed polyacrylamide, polyaluminum chloride, sulfuric acid polyacrylamide, sodium sulfate, formamide, fatty alcohol polyoxyethylene ether, carboxymethyl cellulose, sodium alkylsulfonate, Sodium long-chain amidobenzenesulfonate and sodium ethylenediaminetetraacetate are added together into pure water at a temperature of 45°C to 55°C, and after stirring evenly, the post-treatment auxiliary YBD for disperse dyeing is obtained;
[0116] Pr...
PUM
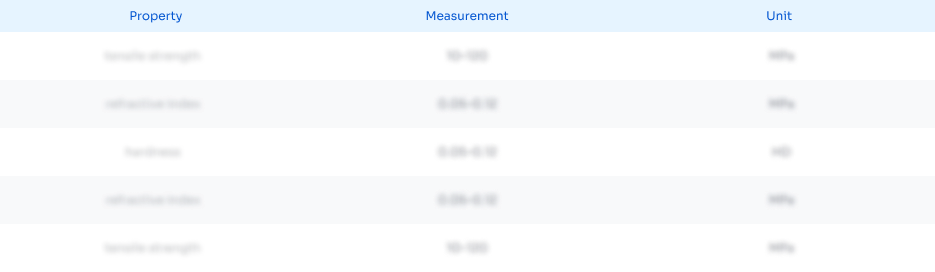
Abstract
Description
Claims
Application Information

- R&D Engineer
- R&D Manager
- IP Professional
- Industry Leading Data Capabilities
- Powerful AI technology
- Patent DNA Extraction
Browse by: Latest US Patents, China's latest patents, Technical Efficacy Thesaurus, Application Domain, Technology Topic, Popular Technical Reports.
© 2024 PatSnap. All rights reserved.Legal|Privacy policy|Modern Slavery Act Transparency Statement|Sitemap|About US| Contact US: help@patsnap.com