Preparation method of prealloyed high-entropy alloy porous material
A pre-alloyed, porous material technology, applied in metal processing equipment, transportation and packaging, etc., to achieve high production efficiency, good economy, excellent corrosion resistance and high temperature oxidation resistance
- Summary
- Abstract
- Description
- Claims
- Application Information
AI Technical Summary
Problems solved by technology
Method used
Examples
Embodiment Construction
[0020] The present invention will be further described below in conjunction with specific examples, so that those skilled in the art can better understand the present invention and implement it, but the given examples are not intended to limit the present invention.
[0021] 1. A method for preparing a pre-alloyed CrNiFeTiMoW high-entropy alloy porous material according to this embodiment, the preparation steps are as follows:
[0022] Step 1, raw material weighing: Weigh ultrasonically treated Cr, Ni, Fe, Ti, Mo and W materials according to equimolar ratio;
[0023] Step 2: Atomized powder production: ① put the material weighed in step 1 into a medium-frequency induction melting furnace and melt it into a metal liquid; ② introduce a high-speed jet of argon flow through the nozzle to impact and shear the metal flow, breaking it into fine particles The metal droplet, the nozzle gap size is 0.5~1.0mm, and the spray angle is 30~60°; ③The liquid droplet is quenched in 1.8~2.0MPa p...
PUM
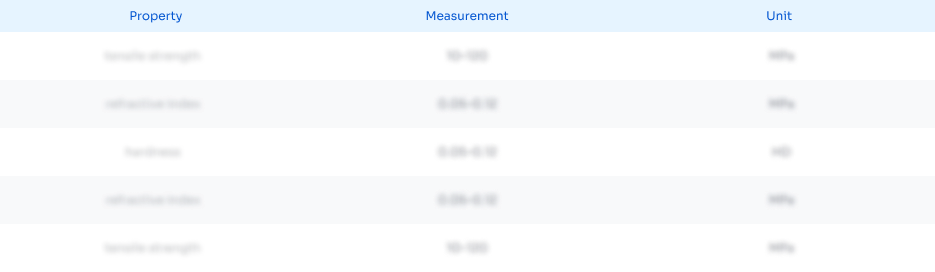
Abstract
Description
Claims
Application Information

- Generate Ideas
- Intellectual Property
- Life Sciences
- Materials
- Tech Scout
- Unparalleled Data Quality
- Higher Quality Content
- 60% Fewer Hallucinations
Browse by: Latest US Patents, China's latest patents, Technical Efficacy Thesaurus, Application Domain, Technology Topic, Popular Technical Reports.
© 2025 PatSnap. All rights reserved.Legal|Privacy policy|Modern Slavery Act Transparency Statement|Sitemap|About US| Contact US: help@patsnap.com