Phase change heat dissipation device
A technology for heat dissipation device and phase change heat, which is used in indirect heat exchangers, lighting and heating equipment, cooling/ventilation/heating renovation, etc. Non-uniformity and other problems, to achieve the effect of improving pressure bearing capacity, efficient boiling heat transfer, and uniform heat expansion
- Summary
- Abstract
- Description
- Claims
- Application Information
AI Technical Summary
Problems solved by technology
Method used
Image
Examples
Embodiment 1
[0081] For the heat source 30 with a size of 30mm×45mm, the power of the heat source 30 is adjusted by frequency conversion, the condensing part 12 is air-cooled, the air volume is provided by the test wind tunnel, the inlet air temperature is 25°C, and the outlet air temperature is 50°C. Control the temperature at 60°C, use different phases to change the heat medium 20, and test the working pressure and heating power inside the phase change component. The test results are shown in Table 2:
[0082] Table 2
[0083]
[0084] As can be seen from the data in Table 2, the present invention uses a phase-change heat medium 20 with a boiling point lower than 30° C. under standard atmospheric pressure. Due to the increase in the pressure difference in the phase-change component, the transmission capacity of the phase-change component is greatly increased. For a size of 45mm ×69mm CPU, radiator with the same volume, using R134a, R142b, R114, R124, R1233Zd(E), R1234Ze(Z), R1234Ze(E)...
PUM
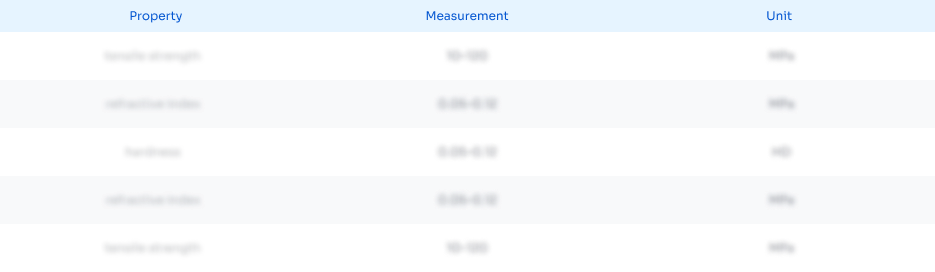
Abstract
Description
Claims
Application Information

- R&D Engineer
- R&D Manager
- IP Professional
- Industry Leading Data Capabilities
- Powerful AI technology
- Patent DNA Extraction
Browse by: Latest US Patents, China's latest patents, Technical Efficacy Thesaurus, Application Domain, Technology Topic, Popular Technical Reports.
© 2024 PatSnap. All rights reserved.Legal|Privacy policy|Modern Slavery Act Transparency Statement|Sitemap|About US| Contact US: help@patsnap.com