3D Printing material
A 3D printing and composite plastic technology, applied in the field of 3D printing materials, can solve the problems of poor colorability, high price of 3D printing materials, insufficient strength, etc., and achieve the effect of uniform stacking, tight materials, and increased strength
- Summary
- Abstract
- Description
- Claims
- Application Information
AI Technical Summary
Problems solved by technology
Method used
Examples
Embodiment 1
[0021] This embodiment provides a 3D printing material, which is made by mixing components A and B according to the mass ratio of 1:1.5, wherein A includes the following components in parts by mass: 90 parts of composite plastic, modified phenolic resin 50 parts, 8 parts of nano-titanium dioxide, 20 parts of polytetrafluoroethylene, 10 parts of nano-pigment, 3 parts of polyphenylene ether sulfone, 6 parts of nano-metal material, 4 parts of polyisocyanate, 2 parts of stabilizer, 3 parts of attapulgite, 6 parts of dialkylamino methacrylate quaternary ammonium salt polymer color fixing agent, 2 parts of nano-manganese oxide, of which composite plastics include 60 parts of ABS resin, 20 parts of polyvinyl chloride, 13 parts of binary ethylene propylene rubber, carbon fiber 10 parts, 4 parts of zinc sulfide powder, 11 parts of cellulose acetate-butyrate, 3 parts of coupling agent; nano-metal materials are nano-aluminum powder, nano-zirconium powder, nano-zinc powder, nano-iron powde...
Embodiment 2
[0024] This embodiment provides a 3D printing material, which is made by mixing components A and B according to a mass ratio of 1:2, wherein A includes the following components in parts by mass: 95 parts of composite plastic, modified phenolic resin 60 parts, 12 parts of nano-titanium dioxide, 22 parts of polytetrafluoroethylene, 13 parts of nano-pigment, 4 parts of polyphenylene ether sulfone, 8 parts of nano-metal material, 4.5 parts of polyisocyanate, 3.5 parts of stabilizer, 4 parts of soybean protein glue, two 7 parts of alkylamino methacrylate quaternary ammonium salt polymer color fixing agent, 3 parts of nano-manganese oxide, of which composite plastics include 70 parts of ABS resin, 25 parts of polyvinyl chloride, 16 parts of binary ethylene propylene rubber, and 14 parts of carbon fiber 5 parts, 5 parts of zinc sulfide powder, 13 parts of cellulose acetate-butyrate, 4 parts of coupling agent; the nano metal materials are nano aluminum powder, nano zirconium powder, na...
PUM
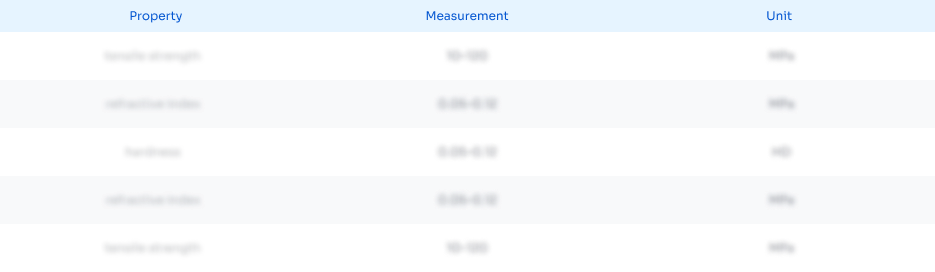
Abstract
Description
Claims
Application Information

- R&D
- Intellectual Property
- Life Sciences
- Materials
- Tech Scout
- Unparalleled Data Quality
- Higher Quality Content
- 60% Fewer Hallucinations
Browse by: Latest US Patents, China's latest patents, Technical Efficacy Thesaurus, Application Domain, Technology Topic, Popular Technical Reports.
© 2025 PatSnap. All rights reserved.Legal|Privacy policy|Modern Slavery Act Transparency Statement|Sitemap|About US| Contact US: help@patsnap.com