Preparation method of high-permeability aerosolized iron silicon aluminum magnetic powder core
A technology of high magnetic permeability and sendust powder, which is applied in the manufacture of inductors/transformers/magnets, electrical components, metal processing equipment, etc., and can solve the problem that the formability and permeability of sendust magnetic powder cores cannot be optimized at the same time. problem, to achieve the effect of reducing the breath of the magnetic core, improving the magnetic permeability, and simple process
- Summary
- Abstract
- Description
- Claims
- Application Information
AI Technical Summary
Problems solved by technology
Method used
Image
Examples
Embodiment 1
[0024] Take by weighing the raw material that total weight is 200kg, wherein the aluminum ingot of 10.8kg, the ferrosilicon ingot of 25.6kg, the surplus is iron, wherein silicon content is 75wt% in the ferrosilicon ingot, is placed in vacuum high-frequency induction furnace and smelts, waits for After melting, remove the scum; choose 2.5MPa pressure nitrogen in the tundish of the atomization equipment for atomization powder; sieve the powder, and then carry out particle size combination, the powder particle size distribution is -200 ~ +300 mesh, -300 mesh ~+400 mesh, -400 mesh or less, the weight ratio of the three is 2:3:15; put the mixed powder into the H 2 Carry out heat treatment under atmosphere protection for 1.5 hours, heat treatment temperature is 800 ℃; take heat treated powder 20kg and 1kg aluminum alloy chromium-free passivating agent solution and mix and stir, stirring time is 25 minutes, take it out and dry it at room temperature for 4 hours, then place In the ove...
Embodiment 2
[0028] Take by weighing the raw material that gross weight is 200kg, wherein the aluminum ingot of 10.4kg, the ferrosilicon ingot of 20.5kg, the surplus is iron, wherein silicon content is 90wt% in the ferrosilicon ingot, puts in the vacuum high-frequency induction furnace to smelt, waits for After melting, remove the scum; choose 3MPa pressure nitrogen in the tundish of the atomization equipment to atomize and make powder; sieve the powder, and then carry out particle size combination. The powder particle size distribution is -200~+300 mesh, -300~ +400 mesh, -400 mesh or less, the weight ratio of the three is 1:1:10; put the mixed powder into the H 2Carry out heat treatment under atmosphere protection for 3 hours, and the heat treatment temperature is 760°C; take 20kg of heat-treated powder and 1.2kg of aluminum alloy chromium-free passivator solution and mix and stir for 20 minutes, take it out and dry it at room temperature for 6 hours, and then place In the oven, the flatt...
Embodiment 3
[0032] Take by weighing the raw material that total weight is 200kg, wherein the aluminum ingot of 11.6kg, the ferrosilicon ingot of 21.6kg, the surplus is iron, wherein silicon content is 95wt% in the ferrosilicon ingot, is placed in vacuum high-frequency induction furnace and smelts, waits for After melting, remove the scum; choose 3MPa pressure nitrogen in the tundish of the atomization equipment to atomize and make powder; sieve the powder, and then carry out particle size combination. The powder particle size distribution is -200~+300 mesh, -300~ +400 mesh, -400 mesh or less, the weight ratio of the three is 3:4:13; put the mixed powder into the H 2 Carry out heat treatment under atmosphere protection for 3 hours, and the heat treatment temperature is 760°C; take 20kg of heat-treated powder and 1.2kg of aluminum alloy chromium-free passivator solution and mix and stir for 20 minutes, take it out and dry it at room temperature for 6 hours, and then place In the oven, the f...
PUM
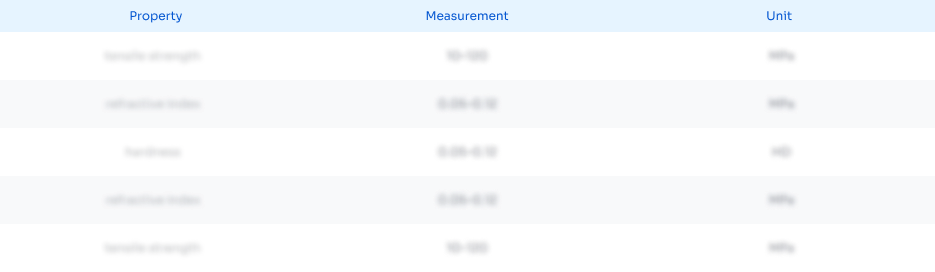
Abstract
Description
Claims
Application Information

- Generate Ideas
- Intellectual Property
- Life Sciences
- Materials
- Tech Scout
- Unparalleled Data Quality
- Higher Quality Content
- 60% Fewer Hallucinations
Browse by: Latest US Patents, China's latest patents, Technical Efficacy Thesaurus, Application Domain, Technology Topic, Popular Technical Reports.
© 2025 PatSnap. All rights reserved.Legal|Privacy policy|Modern Slavery Act Transparency Statement|Sitemap|About US| Contact US: help@patsnap.com