Method for preparing Pt/C catalyst from platinum-containing waste catalyst
A technology of spent catalysts and catalysts, applied in chemical instruments and methods, physical/chemical process catalysts, metal/metal oxides/metal hydroxide catalysts, etc., can solve problems such as high raw material costs, complicated operations, and environmental pollution. Achieve the effect of low cost, simple operation and short process
- Summary
- Abstract
- Description
- Claims
- Application Information
AI Technical Summary
Problems solved by technology
Method used
Image
Examples
Embodiment 1
[0031] After the platinum-containing waste catalyst was roasted at 700°C for 8 hours, it was oxidized to chloroplatinic acid by hydrogen peroxide under the condition of hydrogen ion concentration of 6.0 mol / L in the system. The crude chloroplatinic acid solution was obtained by filtration. Chloroplatinic acid solution was obtained by extraction with tert-butylamine. The volume ratio of tert-butylamine to crude chloroplatinic acid aqueous solution was 0.5:1, and then back-extracted with 5.0 mol / L sodium hydroxide solution to obtain a solution in which 99% of the solute was sodium chloroplatinate. Mix carbon black with 99% of the solute solution of sodium chloroplatinate in a reaction kettle, add formaldehyde and reduce sodium chloroplatinate for 3 hours at 20°C to obtain a Pt / C powder with a Pt loading of 10%, after filtration, Wash and dry to obtain Pt / C catalyst.
Embodiment 2
[0033] After the platinum-containing spent catalyst was calcined at 800°C for 6 hours, it was oxidized to chloroplatinic acid by hydrogen peroxide under the condition of hydrogen ion concentration of 4.0 mol / L in the system. The crude chloroplatinic acid solution was obtained by filtration. Chloroplatinic acid solution was obtained by extraction with tert-butylamine. The volume ratio of tert-butylamine to crude chloroplatinic acid aqueous solution was 0.75:1, and then back-extracted with 4.0mol / L sodium hydroxide solution to obtain a solution in which 99.1% of the solute was sodium chloroplatinate. Mix carbon black with a solution of 99.1% sodium chloroplatinate as the solute in a reaction kettle, add formaldehyde and reduce sodium chloroplatinate at 40°C for 2.5h to obtain Pt / C powder with a Pt loading of 9%, and filter , washing and drying to obtain a Pt / C catalyst.
Embodiment 3
[0035] After the platinum-containing waste catalyst was calcined at 900°C for 4 hours, it was oxidized to chloroplatinic acid by hydrogen peroxide under the condition of hydrogen ion concentration of 2.0 mol / L in the system. The crude chloroplatinic acid solution was obtained by filtration. Chloroplatinic acid solution was obtained by extraction with tert-butylamine. The volume ratio of tert-butylamine to crude chloroplatinic acid aqueous solution was 1:1, and then back-extracted with 3.0mol / L sodium hydroxide solution to obtain a solution in which 99.3% of the solute was sodium chloroplatinate. Mix carbon black with 99.3% of the solute solution of sodium chloroplatinate in a reaction kettle, add formaldehyde and reduce sodium chloroplatinate at 60°C for 2 hours to obtain Pt / C powder with a Pt loading of 8%, filter, Wash and dry to obtain Pt / C catalyst.
PUM
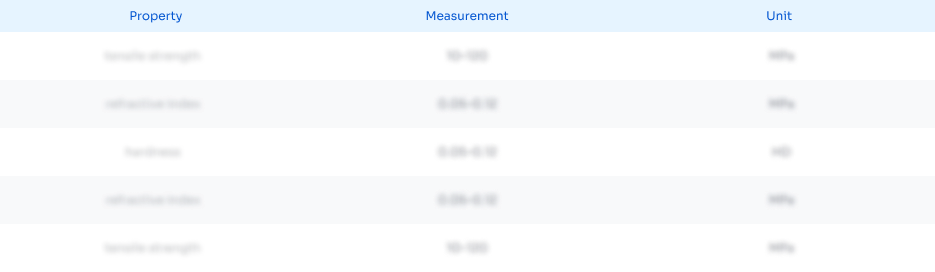
Abstract
Description
Claims
Application Information

- R&D Engineer
- R&D Manager
- IP Professional
- Industry Leading Data Capabilities
- Powerful AI technology
- Patent DNA Extraction
Browse by: Latest US Patents, China's latest patents, Technical Efficacy Thesaurus, Application Domain, Technology Topic, Popular Technical Reports.
© 2024 PatSnap. All rights reserved.Legal|Privacy policy|Modern Slavery Act Transparency Statement|Sitemap|About US| Contact US: help@patsnap.com