Method for improving electrolytic zinc waste residue sintering mode
A technology of waste slag and electric zinc, which is applied in the direction of improving process efficiency, can solve the problems of high production cost, complicated embedding relationship, low recovery rate of electric zinc process, etc., and achieve the effect of reducing coal utilization rate and cost saving
- Summary
- Abstract
- Description
- Claims
- Application Information
AI Technical Summary
Problems solved by technology
Method used
Image
Examples
Embodiment 1
[0026] This embodiment provides a method for improving the roasting method of electrolytic zinc waste slag, including:
[0027] (1) When opening the kiln, control the kiln speed: when the temperature in the kiln is 90°C, control the kiln speed to 0.4r / 4h; when the temperature in the kiln is 180°C, control the kiln speed to 0.4r / h; When the temperature is 450°C, control the kiln speed to 0.8r / 300s; when the temperature inside the kiln is 610°C, start to put in neutralized slag;
[0028] (2) After the neutralization slag is fed, the control system operates: the kiln speed is 1r / 60s; the blast volume is 50m 3 / min; kiln tail temperature is 550°C; kiln tail negative pressure is ±50Pa; surface cooler inlet temperature is 350°C; surface cooler outlet temperature is 120°C; dust collector inlet temperature is 130°C; roasting temperature is 750°C ; Vulcanization time is 16h.
Embodiment 2
[0030] This embodiment provides a method for improving the roasting method of electrolytic zinc waste slag, including:
[0031] (1) When opening the kiln, control the kiln speed: when the temperature in the kiln is 80°C, control the kiln speed to 0.6r / 4h; when the temperature in the kiln is 150°C, control the kiln speed to 0.6r / h; When the temperature is 500°C, control the kiln speed to 1.2r / 300s; when the temperature inside the kiln is 620°C, start to put in neutralized slag;
[0032] (2) After the neutralization slag is fed, the control system operates: the kiln speed is 1r / 180s; the blast volume is 60m 3 / min; kiln tail temperature is 650°C; kiln tail negative pressure is ±50Pa; surface cooler inlet temperature is 500°C; surface cooler outlet temperature is 140°C; dust collector inlet temperature is 150°C; roasting temperature is 900°C ; Vulcanization time is 24h.
Embodiment 3
[0034] This embodiment provides a method for improving the roasting method of electrolytic zinc waste slag, including:
[0035] (1) When opening the kiln, control the kiln speed: when the temperature in the kiln is 120°C, control the kiln speed to 0.5r / 4h; when the temperature in the kiln is 140°C, control the kiln speed to 0.5r / h; When the temperature is 480°C, control the kiln speed to 1r / 300s; when the temperature in the kiln is 605°C, start to put in neutralized slag;
[0036] (2) After the neutralization slag is fed, the control system operates: the kiln speed is 1r / 70s; the blast volume is 30m 3 / min; kiln tail temperature is 500°C; kiln tail negative pressure is ±50Pa; surface cooler inlet temperature is 400°C; surface cooler outlet temperature is 120°C; dust collector inlet temperature is 140°C; roasting temperature is 850°C ; Vulcanization time is 20h.
PUM
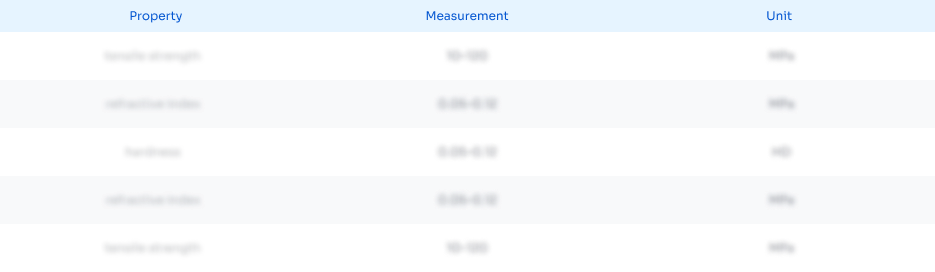
Abstract
Description
Claims
Application Information

- Generate Ideas
- Intellectual Property
- Life Sciences
- Materials
- Tech Scout
- Unparalleled Data Quality
- Higher Quality Content
- 60% Fewer Hallucinations
Browse by: Latest US Patents, China's latest patents, Technical Efficacy Thesaurus, Application Domain, Technology Topic, Popular Technical Reports.
© 2025 PatSnap. All rights reserved.Legal|Privacy policy|Modern Slavery Act Transparency Statement|Sitemap|About US| Contact US: help@patsnap.com