Ceramic sponge material method for preparing nanowire woven microspheres by reverse template method
A technology of ceramic sponge and nanowire, which is applied in the field of ceramic materials and achieves the effect of simple preparation process
- Summary
- Abstract
- Description
- Claims
- Application Information
AI Technical Summary
Problems solved by technology
Method used
Image
Examples
Embodiment 1
[0017] A kind of reverse template method prepares the ceramic sponge material method of nanowire weaving microsphere, comprises the steps:
[0018] (1) Add water-soluble carbon black with 40 wt% mass of silica sol particles to 20 wt% alkaline silica sol (average particle size: 20nm), and mix for 12 hours with a planetary ball mill.
[0019] (2) Add 0.1 wt.% dodecyltrimethylammonium bromide to the above slurry, and adjust the pH to 11.5.
[0020] (3) Foaming the slurry at a rotational speed of 1500-2000 rpm for 20 minutes by mechanical stirring to obtain a stable foam slurry of silica sol and carbon black particles.
[0021] (4) keep the humidity in a constant temperature and humidity box as 70%, and the temperature is 20°C to dry the particle-stabilized foam to obtain a porous green body, such as figure 1 shown. Its microstructure is as figure 2 shown.
[0022] (5) The foam body obtained above was reacted and sintered in an atmospheric nitrogen environment, heated to 1650...
Embodiment 2
[0024] A kind of reverse template method prepares the ceramic sponge material method of nanowire weaving microsphere, comprises the steps:
[0025] (1) Add water-soluble carbon black with a mass of 70 wt% of silica sol particles to 5 wt% alkaline silica sol (average particle size: 50 nm), and mix for 12 hours using a planetary ball mill.
[0026] (2) Add 0.5wt% cetyltrimethylammonium chloride to the above slurry to adjust the pH to 9.0.
[0027] (3) Foaming the slurry at a rotational speed of 1500-2000 rpm for 5 minutes by mechanical stirring to obtain a stable foam slurry of silica sol and carbon black particles.
[0028] (4) Dry the foam in a constant temperature and humidity box in an environment of 95% humidity and 35° C. to obtain a dry billet.
[0029] (5) Sinter the foam body obtained above under an argon atmosphere at normal pressure, heat it to 1450°C at a heating rate of 0.5°C / min, and then keep it warm for 5h. The prepared SiC nanowire braided microspheres are as f...
PUM
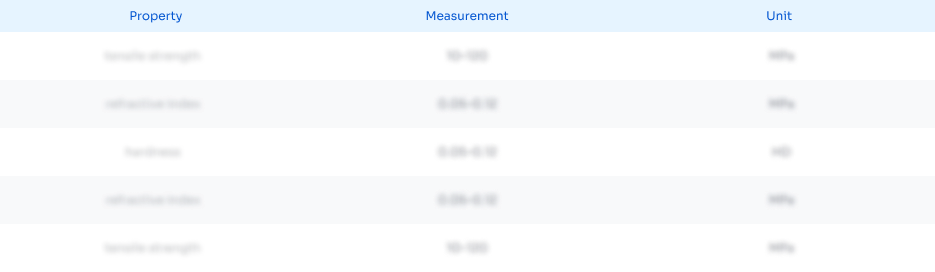
Abstract
Description
Claims
Application Information

- R&D Engineer
- R&D Manager
- IP Professional
- Industry Leading Data Capabilities
- Powerful AI technology
- Patent DNA Extraction
Browse by: Latest US Patents, China's latest patents, Technical Efficacy Thesaurus, Application Domain, Technology Topic, Popular Technical Reports.
© 2024 PatSnap. All rights reserved.Legal|Privacy policy|Modern Slavery Act Transparency Statement|Sitemap|About US| Contact US: help@patsnap.com