Dielectric film with ultrahigh discharge energy storage density and preparation method of dielectric film
A technology of energy storage density and dielectric thin film, which is applied in the direction of fixed capacitor dielectric, fixed capacitor components, circuits, etc., can solve the problems of complex film capacitor technology and the inability to greatly reduce the production cost, and achieve energy storage density. The effect of improving the withstand voltage strength and reducing redistribution
- Summary
- Abstract
- Description
- Claims
- Application Information
AI Technical Summary
Problems solved by technology
Method used
Image
Examples
Embodiment 1
[0032] A dielectric thin film with ultra-high discharge energy storage density, its expression is BiMg 0.5 Ti 0.5 o 3 .
[0033] The preparation method of the above-mentioned dielectric thin film with ultra-high discharge energy storage density comprises the following steps:
[0034] (1) Weigh Bi(NO 3 ) 3 ·5H 2 O, Mg(CH 3 COO) 2 4H 2 O, C 16 h 36 o 4 Ti raw material, the prepared raw material was dissolved in a mixed solvent of acetic acid, distilled water, acetylacetone and ethylene glycol methyl ether with a volume ratio of 11:2:1:35, and stirred at room temperature 25°C for 24 hours to obtain a stable precursor body solution;
[0035] (2) Aging the precursor solution obtained in step (1) at room temperature for 24 hours to obtain a uniformly dispersed sol for spin coating;
[0036] (3) Add the sol obtained in step (2) dropwise on the substrate at a low speed of 800 rpm by spin coating, and then shake off the sol at a high speed of 4600 rpm to obtain a wet gel w...
Embodiment 2
[0042] A dielectric thin film with ultra-high discharge energy storage density, its expression is BiMg 0.5 Ti 0.55 o 3 .
[0043] The preparation method of the above-mentioned dielectric thin film with ultra-high discharge energy storage density comprises the following steps:
[0044] (1) Weigh Bi(NO 3 ) 3 ·5H 2 O, Mg(CH 3 COO) 2 4H 2 O, C 16 h 36 o 4 Ti raw material, the prepared raw material was dissolved in a mixed solvent of acetic acid, distilled water, acetylacetone and ethylene glycol methyl ether with a volume ratio of 11:2:1:35, and stirred at room temperature 25°C for 24 hours to obtain a stable precursor body solution;
[0045] (2) Aging the precursor solution obtained in step (1) at room temperature for 24 hours to obtain a uniformly dispersed sol for spin coating;
[0046] (3) Add the sol obtained in step (2) dropwise on the substrate at a low speed of 800 rpm by spin coating, and then shake off the sol at a high speed of 4600 rpm to obtain a wet gel ...
Embodiment 3
[0053] A dielectric thin film with ultra-high discharge energy storage density, its expression is BiMg 0.5 Ti 0.60 o 3 .
[0054] The preparation method of the above-mentioned dielectric thin film with ultra-high discharge energy storage density comprises the following steps:
[0055] (1) Weigh Bi(NO 3 ) 3 ·5H 2 O, Mg(CH 3 COO) 2 4H 2 O, C 16 h 36 o 4 Ti raw material, the prepared raw material was dissolved in a mixed solvent of acetic acid, distilled water, acetylacetone and ethylene glycol methyl ether with a volume ratio of 11:2:1:35, and stirred at room temperature 25°C for 24 hours to obtain a stable precursor body solution;
[0056] (2) Aging the precursor solution obtained in step (1) at room temperature for 24 hours to obtain a uniformly dispersed sol for spin coating;
[0057] (3) Add the sol obtained in step (2) dropwise on the substrate at a low speed of 800 rpm by spin coating, and then shake off the sol at a high speed of 4600 rpm to obtain a wet gel ...
PUM
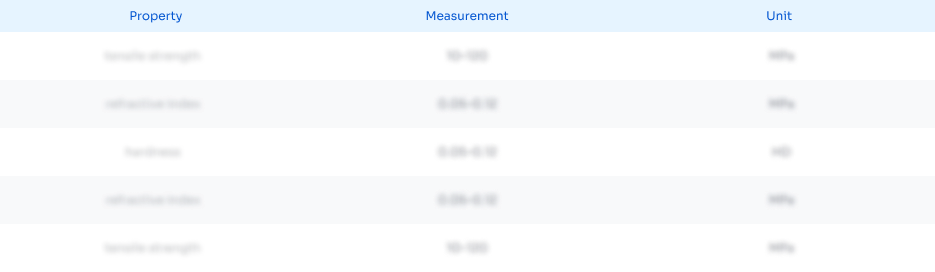
Abstract
Description
Claims
Application Information

- R&D
- Intellectual Property
- Life Sciences
- Materials
- Tech Scout
- Unparalleled Data Quality
- Higher Quality Content
- 60% Fewer Hallucinations
Browse by: Latest US Patents, China's latest patents, Technical Efficacy Thesaurus, Application Domain, Technology Topic, Popular Technical Reports.
© 2025 PatSnap. All rights reserved.Legal|Privacy policy|Modern Slavery Act Transparency Statement|Sitemap|About US| Contact US: help@patsnap.com