Preparation method of high-toughness impact-resistant PET protective film
A technology of impact resistance and protective film, which is applied in the field of preparation of high-toughness and impact-resistant PET protective film, which can solve the problems of insufficient toughness of PET protective film, easy tearing of PET protective film, and poor impact resistance, so as to improve toughness And the effects of impact resistance, enhanced connection density, and enhanced dispersion
- Summary
- Abstract
- Description
- Claims
- Application Information
AI Technical Summary
Problems solved by technology
Method used
Image
Examples
example 1
[0026]In terms of parts by weight, weigh 1.5 parts of calcium hydroxide powder, 0.6 parts of sucrose and 110 parts of distilled water into a beaker under a vacuum environment, mix and stir with a stirrer at a speed of 600r / min for 30min, and pour 500mL of Inject carbon dioxide gas at a rate of 1 / min, filter to obtain the filter residue, put it in an oven and dry it for 3 hours at a temperature of 110°C to obtain the reaction product; in parts by weight, weigh 8 parts of the above reaction product and 20 parts of distilled water in In the three-necked flask, the temperature of the three-necked flask was raised to 85°C, stirred and mixed with a stirrer at a speed of 600r / min for 30min, and after stirring, 0.5 parts of distearoyloxyisopropyl aluminate, 0.3 parts of ten Octamine, continue to stir for 3 hours, after stirring, suction filter to obtain a filter cake, put the filter cake in an oven and dry at a temperature of 110°C, after drying, grind and pass through a 200-mesh sieve...
example 2
[0028] In terms of parts by weight, weigh 1.7 parts of calcium hydroxide powder, 0.8 parts of sucrose and 115 parts of distilled water into a beaker under a vacuum environment, mix and stir with a stirrer at a speed of 620r / min for 35min, and pour 550mL of Pass carbon dioxide gas at a rate of 1 / min, filter to obtain the filter residue, put it in an oven and dry it for 3.5 hours at a temperature of 115°C to obtain the reaction product; in parts by weight, weigh 9 parts of the above reaction product and 22 parts of distilled water In the three-necked flask, raise the temperature of the three-necked flask to 87°C, stir and mix with a stirrer at a speed of 620r / min for 35min, and add 0.7 parts of distearoyloxyisopropyl aluminate, 0.4 parts of Octadecylamine, continue to stir for 3.5 hours, after stirring, suction filter to obtain a filter cake, put the filter cake in an oven and dry at a temperature of 115°C, after drying, grind and pass through a 200-mesh sieve to obtain a modifie...
example 3
[0030] In terms of parts by weight, weigh 1.8 parts of calcium hydroxide powder, 1.0 parts of sucrose and 120 parts of distilled water into a beaker under a vacuum environment, mix and stir with a stirrer at a speed of 650r / min for 40min, and pour 600mL of Inject carbon dioxide gas at a rate of 1 / min, filter to obtain the filter residue, put it in an oven and dry it for 4 hours at a temperature of 120°C to obtain the reaction product; in parts by weight, weigh 10 parts of the above reaction product and 25 parts of distilled water in In the three-necked flask, raise the temperature of the three-necked flask to 90°C, stir and mix with a stirrer at a speed of 650r / min for 40min, after stirring, add 0.8 parts of distearoyloxyisopropyl aluminate, 0.5 parts of ten Octamine, continue to stir for 4 hours, after stirring, suction filter to obtain a filter cake, put the filter cake in an oven to dry at a temperature of 120°C, and after drying, grind and pass through a 200-mesh sieve to o...
PUM
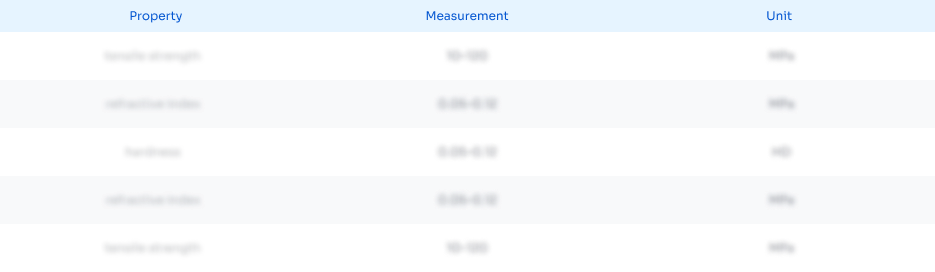
Abstract
Description
Claims
Application Information

- R&D
- Intellectual Property
- Life Sciences
- Materials
- Tech Scout
- Unparalleled Data Quality
- Higher Quality Content
- 60% Fewer Hallucinations
Browse by: Latest US Patents, China's latest patents, Technical Efficacy Thesaurus, Application Domain, Technology Topic, Popular Technical Reports.
© 2025 PatSnap. All rights reserved.Legal|Privacy policy|Modern Slavery Act Transparency Statement|Sitemap|About US| Contact US: help@patsnap.com