Thermal treatment process for 20CrMnMoA steel bevel gear
A technology of bevel gears and gears, which is applied in the field of heat treatment of 20CrMnMoA steel bevel gears, can solve the problems of low impact toughness, etc., and achieve the effects of improving hardness, high order of organization and fine grains.
- Summary
- Abstract
- Description
- Claims
- Application Information
AI Technical Summary
Problems solved by technology
Method used
Image
Examples
Embodiment 1
[0025] A heat treatment process for a 20CrMnMoA steel bevel gear, the chemical element composition and mass percentage of the 20CrMnMoA steel bevel gear are: C: 0.17%, Si: 0.17%, Mn: 0.8%, Cr: 1.0%, Ti: 0.04%, Mo: 0.20%, Ni<0.03%, Cu<0.03%, P<0.035%, S<0.035%, the balance is iron, and the heat treatment process includes the following steps:
[0026] S1: Preparatory process: cleaning and drying the bevel gear forging, and performing anti-carburization treatment on the web between the teeth of the bevel gear;
[0027] S2: Carburizing: Use the method of heating to high temperature. After the gas carburizing furnace is heated to 950°C, put the bevel gear vertically into the furnace, exhaust, and keep warm for 2.5 hours. Cool down to 830±10°C after the penetration layer meets the requirements;
[0028] S3: heat preservation: heat preservation and soaking for 2 hours;
[0029] S4: Two-stage quenching: immerse the bevel gear vertically in calcium chloride solution at a temperature ...
Embodiment 2
[0035] A heat treatment process for a 20CrMnMoA steel bevel gear, the chemical element composition and mass percentage of the 20CrMnMoA steel bevel gear are: C: 0.23%, Si: 0.37%, Mn: 1.3%, Cr: 1.3%, Ti: 0.12%, Mo: 0.30%, Ni<0.03%, Cu<0.03%, P<0.035%, S<0.035%, the balance is iron, and the heat treatment process includes the following steps:
[0036] S1: Preparatory process: cleaning and drying the bevel gear forging, and performing anti-carburization treatment on the web between the teeth of the bevel gear;
[0037] S2: Carburizing: Use the method of heating to high temperature. After the gas carburizing furnace is heated to 920-930°C, put the bevel gear vertically into the furnace, exhaust, keep warm for 2.5 hours, and drop 160-180 drops of kerosene during the heat preservation. Minutes, cool down to 830±10℃ after the penetration layer reaches the requirement;
[0038] S3: heat preservation: heat preservation and soaking for 2 hours;
[0039] S4: two-stage quenching: immers...
Embodiment 3
[0045]A heat treatment process for a 20CrMnMoA steel bevel gear, the chemical element composition and mass percentage of the 20CrMnMoA steel bevel gear are: C: 0.21%, Si: 0.26%, Mn: 0.11%, Cr: 1.2%, Ti: 0.08%, Mo: 0.25%, Ni<0.03%, Cu<0.03%, P<0.035%, S<0.035%, the balance is iron, and the heat treatment process includes the following steps:
[0046] S1: Preparatory process: cleaning and drying the bevel gear forging, and performing anti-carburization treatment on the web between the teeth of the bevel gear;
[0047] S2: Carburizing: Use the method of heating to high temperature. After the gas carburizing furnace is heated to 920-930°C, put the bevel gear vertically into the furnace, exhaust, keep warm for 2.5h, and drop kerosene 160-180 drops / Minutes, cool down to 830±10℃ after the penetration layer reaches the requirement;
[0048] S3: heat preservation: heat preservation and soaking for 2 hours;
[0049] S4: Two-stage quenching: immerse the bevel gear vertically in calciu...
PUM
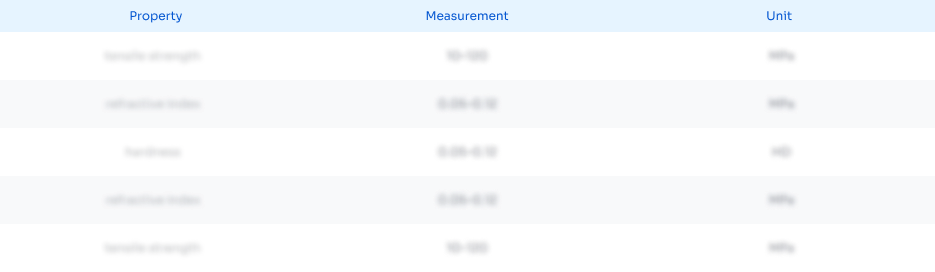
Abstract
Description
Claims
Application Information

- R&D
- Intellectual Property
- Life Sciences
- Materials
- Tech Scout
- Unparalleled Data Quality
- Higher Quality Content
- 60% Fewer Hallucinations
Browse by: Latest US Patents, China's latest patents, Technical Efficacy Thesaurus, Application Domain, Technology Topic, Popular Technical Reports.
© 2025 PatSnap. All rights reserved.Legal|Privacy policy|Modern Slavery Act Transparency Statement|Sitemap|About US| Contact US: help@patsnap.com