Impurity removing agent for smelting copper alloy and application method of impurity removing agent
A copper alloy and smelting technology, which is applied in the field of impurity remover for copper alloy smelting, can solve the problems of ineffective removal of trace impurity elements and non-metallic impurities, etc., achieve good promotion and application value, reduce the content of impurity elements, and purify smelting liquid effect
- Summary
- Abstract
- Description
- Claims
- Application Information
AI Technical Summary
Problems solved by technology
Method used
Image
Examples
Embodiment 1
[0039] A impurity remover for copper alloy smelting, which is mixed with the following raw materials in mass percentage: 10% Eu 2 o 3 Powder, 5% Rb 2 o 2 powder, 5% SiO 2 Powder, 3% TiO 2 powder, 5% Na 2 SiF 6 powder, 15% Na 2 CO 3 powder, the balance is Na 2 B 4 0 7 powder;
[0040] According to the proportion in Example 1, the powders of various industrial pure grades were mixed uniformly by mechanical means, then compressed into a block by a tablet press, and then covered tightly with a thin copper skin.
[0041] When the copper alloy is smelted, after the alloy raw materials are completely melted, the temperature of the melt is raised to the smelting temperature, and then left to stand for 10 minutes to remove slag; When the impurity remover is put into the melt, the impurity remover pressed into agglomerates will melt slowly, so that it will not be lost quickly. The impurity remover and the melt have sufficient contact time. When fine scum appears on the surface...
Embodiment 2
[0044] A impurity remover for copper alloy smelting, which is mixed with the following raw materials in mass percentage: 20% Eu 2 o 3 Powder, 10% Rb 2 o 2 Powder, 12% SiO 2 Powder, 4% TiO 2 powder, 7% Na 2 SiF 6 powder, 17% Na 2 CO 3 powder, the balance is Na 2 B 4 0 7 powder;
[0045] According to the proportion in Example 2, the powders of various industrial grades were mechanically mixed uniformly, then compressed into a block by a tablet press, and then covered tightly with a thin copper sheet.
[0046] When the copper alloy is smelted, after the alloy raw materials are completely melted, the temperature of the melt is raised to the smelting temperature, and then left to stand for 10 minutes to remove slag; When the impurity remover is put into the melt, the impurity remover pressed into agglomerates will melt slowly, so that it will not be lost quickly. The impurity remover and the melt have sufficient contact time. When fine scum appears on the surface of the...
Embodiment 3
[0049] A impurity remover for copper alloy smelting, which is mixed with the following raw materials in mass percentage: 25% Eu 2 o 3 Powder, 15% Rb 2 o 2 Powder, 15% SiO 2 Powder, 5% TiO 2 powder, 10% Na 2 SiF 6 powder, 20% Na 2 CO 3 powder, the balance is Na 2 B 4 0 7 powder;
[0050] According to the proportion in Example 3, the powders of various industrial grades were mechanically mixed uniformly, then compressed into a block by a tablet press, and then covered tightly with a thin copper sheet.
[0051] When the copper alloy is smelted, after the alloy raw materials are completely melted, the temperature of the melt is raised to the smelting temperature, and then left to stand for 10 minutes to remove slag; When the impurity remover is put into the melt, the impurity remover that is pressed into blocks will melt slowly, so that it will not be lost quickly. The impurity remover and the melt have sufficient contact time. When fine scum appears on the surface of ...
PUM
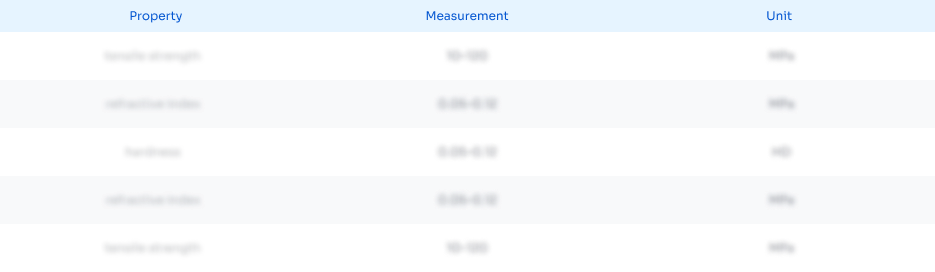
Abstract
Description
Claims
Application Information

- R&D
- Intellectual Property
- Life Sciences
- Materials
- Tech Scout
- Unparalleled Data Quality
- Higher Quality Content
- 60% Fewer Hallucinations
Browse by: Latest US Patents, China's latest patents, Technical Efficacy Thesaurus, Application Domain, Technology Topic, Popular Technical Reports.
© 2025 PatSnap. All rights reserved.Legal|Privacy policy|Modern Slavery Act Transparency Statement|Sitemap|About US| Contact US: help@patsnap.com