Method for producing lithium-rich pure solution from waste lithium ion battery positive electrode active material
A positive electrode active material and lithium-ion battery technology, applied in battery recycling, waste collector recycling, recycling technology, etc., can solve the problems of low recovery rate, high energy consumption of lithium recovery, and large consumption of acid-base neutralization reagents, etc. Achieve the effect of high recovery rate of useful elements, reduce comprehensive recovery cost and increase recovery rate
- Summary
- Abstract
- Description
- Claims
- Application Information
AI Technical Summary
Problems solved by technology
Method used
Image
Examples
Embodiment 1
[0025] Take 200g of ternary battery positive electrode material containing 28.3% nickel, 10.63% cobalt, 11.75% manganese and 6.50% lithium, according to the acid ore mass ratio of 2:1, the hydrogen peroxide volume mass ratio of 1:1, the leaching solid-liquid mass-to-volume ratio 1:10, the leaching time is 1h for sulfuric acid reduction leaching; the leaching solution is adjusted by 30% NaOH solution to adjust the pH value to remove iron. Add sodium phosphate to the nickel extraction raffinate according to 1.2 times the theoretical amount of lithium moles. At 90°C, stir and react for 1 hour to obtain lithium-containing phosphate, the lithium precipitation rate is 96%, and the lithium-containing liquid contains 0.01 g / L; Lithium-containing phosphate concentrate is leached by 200g / L calcium chloride solution, leaching temperature is 90°C, leaching time is 2h, leaching solid-liquid mass to volume ratio is 1:8, lithium leaching rate is 98%, lithium-containing leaching solution The ...
Embodiment 2
[0027]Take 200g of ternary battery cathode material containing 28.3% nickel, 10.63% cobalt, 11.75% manganese and 6.50% lithium. The ratio of liquid mass to volume is 1:10, and the leaching time is 1h for leaching; the leaching liquid is leached through 30% NaOH solution to adjust the pH value to remove iron. Nickel extraction; add sodium phosphate to the nickel extraction raffinate according to 1.2 times the theoretical amount of lithium moles, stir and react for 1.5h at 90°C, the lithium precipitation rate is 96.5%, and the lithium-containing phosphate concentrate is obtained by solid-liquid separation , the lithium-containing phosphate concentrate was leached by 300g / L calcium chloride solution, the leaching temperature was 90°C, the leaching time was 1.5h, the leaching solid-liquid mass to volume ratio was 1:5, the lithium leaching rate was 98.5%, and the lithium-containing leaching solution contained lithium The concentration is about 22.5g / L.
Embodiment 3
[0029] Take 200g of ternary battery cathode material containing 28.3% nickel, 10.63% cobalt, 11.75% manganese and 6.50% lithium, mix the cathode material, concentrated sulfuric acid, and anthracite in proportion, wherein the amount of sulfuric acid added is based on the mass ratio of sulfuric acid to the cathode material 2: 1. The amount of anthracite added is 20% of the mass of the positive electrode material, the roasting temperature is 300°C, and the roasting time is 2 hours; the clinker is leached with water, the leached solid-liquid mass to volume ratio is 1:5, 1% hydrogen peroxide is added, the leaching time is 1 hour, nickel-cobalt The leaching rate of lithium is greater than 95%. The leaching solution adjusts the pH value with 30% NaOH solution to remove iron. Sodium phosphate is added to the solution according to 1.2 times the theoretical amount of lithium moles, and the reaction is stirred for 1 hour at 90°C, and the lithium precipitation rate is 95.5%. The concentra...
PUM
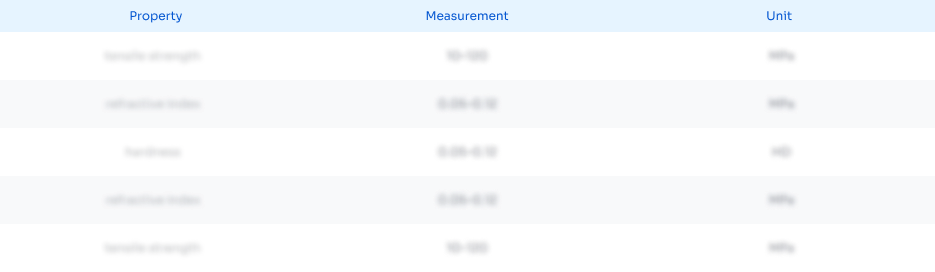
Abstract
Description
Claims
Application Information

- R&D
- Intellectual Property
- Life Sciences
- Materials
- Tech Scout
- Unparalleled Data Quality
- Higher Quality Content
- 60% Fewer Hallucinations
Browse by: Latest US Patents, China's latest patents, Technical Efficacy Thesaurus, Application Domain, Technology Topic, Popular Technical Reports.
© 2025 PatSnap. All rights reserved.Legal|Privacy policy|Modern Slavery Act Transparency Statement|Sitemap|About US| Contact US: help@patsnap.com