Cleaning technology for extracting vanadium from vanadium containing materials through sodium salt roasting
A technology of sodium roasting and raw materials, applied in the direction of improving process efficiency, etc., can solve the problems of sodium chloride resource cost, environmental pollution, high cost, etc., and achieve the effects of low production cost, environmental friendliness and simple process
- Summary
- Abstract
- Description
- Claims
- Application Information
AI Technical Summary
Problems solved by technology
Method used
Image
Examples
Embodiment 1
[0032]10kg of pre-decarburized stone coal mine containing 0.95% vanadium (V) is added with 600g of sodium chloride, mixed and ground to -120 mesh pellets, roasted at 750°C for 2.5h, and the roasted flue gas is absorbed by a filter layer of Ф10-15 lime balls Harmful gases, the calcine is leached with water at room temperature for 3 hours at a solid-to-liquid ratio of 1:2g / mL, and filtered to obtain the water immersion liquid and water leaching residue. Add 1mol / L sodium carbonate solution to the water leaching residue at a solid-to-liquid ratio of 1:2.5g / mL, stir and leaching at 25°C for 3h, filter to obtain the alkali leaching solution and leaching residue, the leaching residue contains 0.15% vanadium (V), vanadium The total leaching rate is 84.5%. Add calcium chloride to the water immersion solution according to 1 times the stoichiometric number of vanadium converted into calcium vanadate, stir at room temperature for 0.5h, filter to obtain calcium vanadate filter cake and so...
Embodiment 2
[0034] Add 150g of sodium chloride to 5kg of stone coal ore powder (-150 mesh) containing 1.13% vanadium (V), use the vanadium-precipitated liquid mass ore obtained in Example 1 to roast at 790°C for 2 hours, and use Ф10 to 15 lime balls for the roasting flue gas The filter layer absorbs the harmful gas therein, and the calcine is added to the vanadium-precipitated solution obtained in Example 1 at a solid-to-liquid ratio of 1:2g / mL and leached at room temperature for 2.5 hours, and filtered to obtain the water leaching liquid and water leaching residue. Water leaching slag was added to the crystallization mother liquor obtained in Example 1 at a solid-to-liquid ratio of 1:3g / mL, stirred and leached at 80°C for 1.5h, and filtered to obtain alkali leaching solution and leaching slag. The leaching slag contained 0.093% vanadium (V). The total leaching rate is 91.8%. The water immersion solution is converted into 1 times of the stoichiometric number of calcium vanadate by vanadiu...
Embodiment 3
[0036] Add 60g of sodium carbonate and 40g of sodium chloride to 500g of vanadium slag containing 13.5% vanadium (V), grind and mix well, roast at 800°C for 3h, add water to the calcine at a solid-to-liquid ratio of 1:3g / mL for 2.5h at 45°C, and filter Obtain water immersion liquid and water leaching residue. Add 1.5mol / L sodium carbonate solution to the water leaching slag at a solid-to-liquid ratio of 1:2.5g / mL, stir and leaching at 65°C for 2h, filter to obtain the alkali leaching solution and leaching slag, the leaching slag contains 0.57% vanadium (V), vanadium The total leaching rate is 95.9%. Add the mixture of calcium oxide and calcium chloride to the water immersion solution according to 1.2 times of the stoichiometric number of vanadium converted into calcium vanadate, stir and ball mill at room temperature for 1.5h, filter to obtain calcium vanadate filter cake and solution after vanadium precipitation, and then add vanadium Stir the calcium acid filter cake into t...
PUM
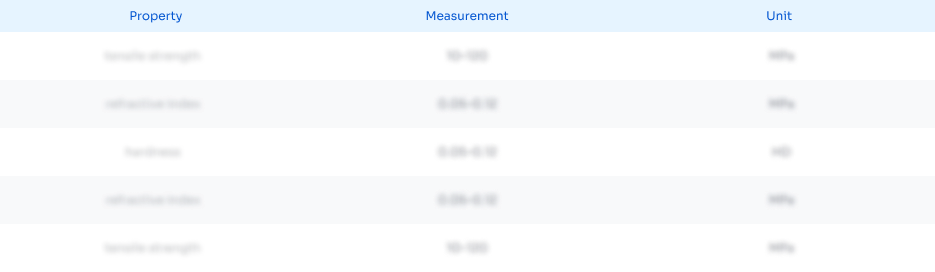
Abstract
Description
Claims
Application Information

- R&D
- Intellectual Property
- Life Sciences
- Materials
- Tech Scout
- Unparalleled Data Quality
- Higher Quality Content
- 60% Fewer Hallucinations
Browse by: Latest US Patents, China's latest patents, Technical Efficacy Thesaurus, Application Domain, Technology Topic, Popular Technical Reports.
© 2025 PatSnap. All rights reserved.Legal|Privacy policy|Modern Slavery Act Transparency Statement|Sitemap|About US| Contact US: help@patsnap.com