Zirconium silicate powder and preparation method and application thereof
A technology of zirconium silicate and powder, applied in the field of zirconium silicate powder and its preparation, can solve the problems of uneven morphology, large crystal size, irregular and uniform powder morphology, etc.
- Summary
- Abstract
- Description
- Claims
- Application Information
AI Technical Summary
Problems solved by technology
Method used
Image
Examples
preparation example Construction
[0026] The invention provides a method for preparing zirconium silicate powder, including the following steps: (1) mixing a zirconium source, acid and water to obtain a zirconium source solution; (2) mixing a silicon source and a solvent to obtain a silicon source solution (3) The zirconium source solution obtained in the step (1) is mixed with the silicon source solution obtained in the step (2) and then pre-hydrolyzed to obtain a precursor solution; (4) the step (3) is obtained The precursor solution, mineralizer, and surfactant are mixed to perform a solvothermal reaction to obtain zirconium silicate powder; the steps (1) and (2) are not limited in order.
[0027] The invention mixes zirconium source, acid and water to obtain zirconium source solution. In the present invention, the zirconium source preferably includes one or more of zirconium sulfate, zirconium nitrate, zirconyl nitrate, zirconium chloride, zirconium oxychloride, zirconium acetate, zirconium acetylacetonate, a...
Embodiment 1
[0047] (1) Mix zirconium chloride, sulfuric acid and water to obtain a zirconium chloride solution with a concentration of 0.09 mol / L; wherein the molar ratio of zirconium chloride to sulfuric acid is 1:35;
[0048] (2) Mix ethyl orthosilicate, water, and ethanol at a molar ratio of 1:450:40 to obtain an ethyl orthosilicate solution with a concentration of 0.10 mol / L;
[0049] (3) Add the ethyl orthosilicate solution dropwise to the zirconium chloride solution, adjust the volume to control the molar ratio of the zirconium source to the silicon source at 1:1.2; pre-hydrolyze in a water bath at 20°C for 5 hours to obtain the precursor solution ;
[0050] (4) Add sodium fluoride with a molar ratio of zirconium chloride: sodium fluoride=1:0.8 to the precursor solution and the theoretical total mass of zirconium silicate (the silicon source and the zirconium source are 100% converted into zirconium silicate) 3% PEG and 0.02% urea were mixed, and solvothermal reaction was carried out at 1...
Embodiment 2
[0054] (1) Mix zirconium oxychloride, hydrochloric acid and water to obtain a zirconium oxychloride solution with a concentration of 0.12mol / L; wherein the molar ratio of zirconium oxychloride to hydrochloric acid is 1:50;
[0055] (2) Mix sodium silicate, water and isopropanol at a molar ratio of 1:500:30 to obtain a sodium silicate solution with a concentration of 0.09mol / L;
[0056] (3) Add the sodium silicate solution dropwise to the zirconium oxychloride solution, adjust the volume ratio to control the molar ratio of the zirconium source to the silicon source at 1:1.1; pre-hydrolyze in a water bath at 30°C for 0.5h to obtain the precursor Solution
[0057] (4) Add sodium fluoride with a molar ratio of zirconium oxychloride: sodium fluoride=1:1.5 to the precursor solution and the total mass of theoretical zirconium silicate (the silicon source and the zirconium source are 100% converted into zirconium silicate ) Mix 5% of PVP and carry out a solvothermal reaction at 180°C for 12...
PUM
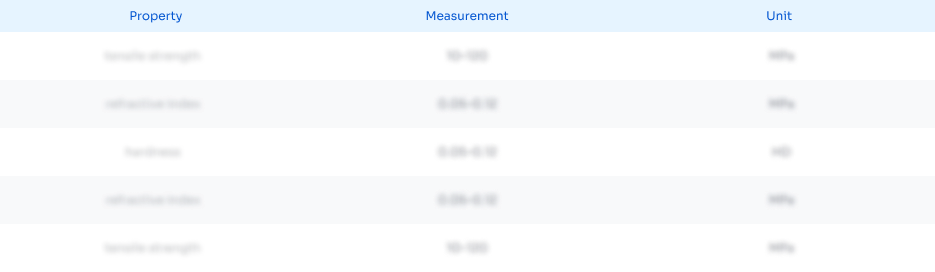
Abstract
Description
Claims
Application Information

- Generate Ideas
- Intellectual Property
- Life Sciences
- Materials
- Tech Scout
- Unparalleled Data Quality
- Higher Quality Content
- 60% Fewer Hallucinations
Browse by: Latest US Patents, China's latest patents, Technical Efficacy Thesaurus, Application Domain, Technology Topic, Popular Technical Reports.
© 2025 PatSnap. All rights reserved.Legal|Privacy policy|Modern Slavery Act Transparency Statement|Sitemap|About US| Contact US: help@patsnap.com