Passivating agent for hot-dip galvanized steel plate and preparation method
A technology of hot-dip galvanized steel sheet and passivating agent, applied in the coating process of metal materials, etc., can solve the problems of large consumption, low passivation efficiency, passivation film density and hardness not up to standard, etc., and achieve passivation efficiency High, smooth surface, good dispersion uniformity effect
- Summary
- Abstract
- Description
- Claims
- Application Information
AI Technical Summary
Problems solved by technology
Method used
Examples
Embodiment 1
[0019] A passivating agent for hot-dip galvanized steel sheets proposed by the present invention comprises the following raw materials in parts by weight: 28 parts of trivalent chromium compounds, 15 parts of sodium hypophosphite, 10 parts of sodium sulfate, 8 parts of sodium fluorosilicate, cobalt chloride 18 parts, 10 parts of boric acid, 22 parts of organic carboxylic acid, 1 part of sodium dodecylbenzenesulfonate, 12 parts of glycerol, 40 parts of deionized water, wherein the mass ratio of the trivalent complex is 1.2:2 : 0.8 mixture of chromium chloride, chromium nitrate and potassium dichromate; organic carboxylic acid is a mixture of oxalic acid, 2-methylsuccinic acid and sebacic anhydride with a mass ratio of 3:1.2:1.
[0020] Its preparation method comprises the following steps:
[0021] S1. Add the trivalent chromium compound of the specific gravity, sodium hypophosphite, sodium nitrate and cobalt chloride into deionized water, stir and mix for 30 minutes at 85°C, an...
Embodiment 2
[0026] A passivator for hot-dip galvanized steel sheets proposed by the present invention comprises the following raw materials in parts by weight: 45 parts of trivalent chromium compound, 22 parts of sodium hypophosphite, 16 parts of sodium sulfate, 10 parts of sodium fluorosilicate, cobalt chloride 25 parts, 14 parts of boric acid, 28 parts of organic carboxylic acid, 3 parts of sodium dodecylbenzenesulfonate, 20 parts of glycerol, 55 parts of deionized water, wherein the mass ratio of the trivalent complex is 1.6:2.8 : 1 mixture of chromium chloride, chromium nitrate and potassium dichromate; the organic carboxylic acid is a mixture of oxalic acid, 2-methylsuccinic acid and sebacic anhydride in a mass ratio of 4:1.5:1.
[0027] Its preparation method comprises the following steps:
[0028] S1. Add the trivalent chromium compound of the specific gravity, sodium hypophosphite, sodium nitrate and cobalt chloride into deionized water, stir and mix for 20 minutes at 105°C, and d...
Embodiment 3
[0033] A passivator for hot-dip galvanized steel sheets proposed by the present invention comprises the following raw materials in parts by weight: 32 parts of trivalent chromium compound, 18 parts of sodium hypophosphite, 12 parts of sodium sulfate, 9 parts of sodium fluorosilicate, cobalt chloride 22 parts, 12 parts of boric acid, 25 parts of organic carboxylic acid, 2 parts of sodium dodecylbenzenesulfonate, 15 parts of glycerol, 48 parts of deionized water, wherein the mass ratio of the trivalent complex is 1.4:2.2 : 1 mixture of chromium chloride, chromium nitrate and potassium dichromate; the organic carboxylic acid is a mixture of oxalic acid, 2-methylsuccinic acid and sebacic anhydride in a mass ratio of 4:1.4:1.
[0034] Its preparation method comprises the following steps:
[0035] S1. Add the trivalent chromium compound of the specific gravity, sodium hypophosphite, sodium nitrate and cobalt chloride into deionized water, stir and mix for 25 minutes at 95°C, and dis...
PUM
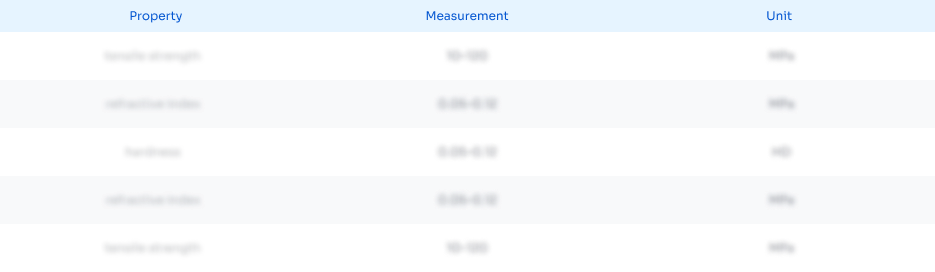
Abstract
Description
Claims
Application Information

- R&D
- Intellectual Property
- Life Sciences
- Materials
- Tech Scout
- Unparalleled Data Quality
- Higher Quality Content
- 60% Fewer Hallucinations
Browse by: Latest US Patents, China's latest patents, Technical Efficacy Thesaurus, Application Domain, Technology Topic, Popular Technical Reports.
© 2025 PatSnap. All rights reserved.Legal|Privacy policy|Modern Slavery Act Transparency Statement|Sitemap|About US| Contact US: help@patsnap.com