Preparation method of phosphorus-based flame-retardant glass fiber reinforced PBT composite material
A composite material, phosphorus-based flame-retardant technology, applied in the field of polymer materials, can solve the problems of material mechanical performance deterioration, poor antibacterial performance, and large amount of addition
- Summary
- Abstract
- Description
- Claims
- Application Information
AI Technical Summary
Problems solved by technology
Method used
Image
Examples
preparation example Construction
[0056] The preparation method of PBT composite material of the present invention may further comprise the steps:
[0057] (1) Weigh the raw materials of each component by weight percentage;
[0058] (2) Dry the corresponding PBT resin in a vacuum oven at 120-140°C for 3-5 hours;
[0059](3) Add the corresponding glass fiber, filling material, phosphorus flame retardant, flame retardant synergist, aluminum hydroxide, diethylene glycol dimethyl benzoate, coupling agent, inorganic antibacterial agent, antibacterial Oxygen and other processing aids are placed in another vacuum drying oven, the temperature is controlled at 40-50°C, and the time is 3-4h;
[0060] (4) Pour the component materials described in steps (2) and (3) into a mixer for stirring and mixing at room temperature, first stir at a stirring speed of 200r / min for 2 minutes, and then stir at a stirring speed of 500r / min 4min obtains premixture;
[0061] (5) Put the premix in the hopper of the twin-screw extruder an...
Embodiment 1
[0063] A phosphorus-based flame-retardant glass fiber-reinforced PBT composite material consists of the following components by weight percentage:
[0064] PBT 49%
[0065] Fiberglass 19%
[0066] Filling material 5%
[0067] Phosphorus flame retardant 9%
[0068] Flame Retardant Synergist 6%
[0069] Aluminum hydroxide 3.5%
[0070] Diethylene glycol di-m-toluate 3.5%
[0071] Coupling agent 1.2%
[0072] Inorganic antibacterial agent 0.8%
[0073] Antioxidant 0.9%
[0074] Other processing aids 2.1%
[0075] The preparation method of the above-mentioned phosphorus-based flame-retardant glass fiber reinforced PBT composite material specifically includes the following steps:
[0076] (1) Weigh the raw materials of each component by weight percentage;
[0077] (2) Dry the corresponding PBT resin in a vacuum oven at 130°C for 4 hours;
[0078] (3) Add the corresponding glass fiber, filling material, phosphorus flame retardant, flame retardant synergist, aluminum hydro...
Embodiment 2
[0082] A phosphorus-based flame-retardant glass fiber-reinforced PBT composite material consists of the following components by weight percentage:
[0083] PBT 58%
[0084] Fiberglass 12%
[0085] Filling material 7%
[0086] Phosphorus flame retardant 7%
[0087] Flame Retardant Synergist 4%
[0088] Aluminum hydroxide 5%
[0089] Diethylene glycol di-m-toluate 4%
[0090] Coupling agent 0.6%
[0091] Inorganic antibacterial agent 0.6%
[0092] Antioxidant 0.7%
[0093] Other processing aids 1.1%
[0094] The preparation method of the above-mentioned phosphorus-based flame-retardant glass fiber reinforced PBT composite material specifically includes the following steps:
[0095] (1) Weigh the raw materials of each component by weight percentage;
[0096] (2) Dry the corresponding PBT resin in a vacuum oven at 140°C for 3 hours;
[0097] (3) Add the corresponding glass fiber, filling material, phosphorus flame retardant, flame retardant synergist, aluminum hydroxide...
PUM
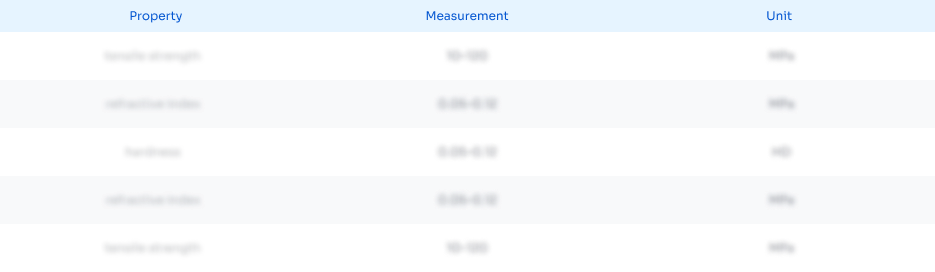
Abstract
Description
Claims
Application Information

- R&D
- Intellectual Property
- Life Sciences
- Materials
- Tech Scout
- Unparalleled Data Quality
- Higher Quality Content
- 60% Fewer Hallucinations
Browse by: Latest US Patents, China's latest patents, Technical Efficacy Thesaurus, Application Domain, Technology Topic, Popular Technical Reports.
© 2025 PatSnap. All rights reserved.Legal|Privacy policy|Modern Slavery Act Transparency Statement|Sitemap|About US| Contact US: help@patsnap.com