A dpf with low back pressure, low light-off temperature catalytic layer and its preparation process
A technology of light-off temperature and preparation process, which is applied in the field of catalyst research and preparation, and the research and preparation of automobile exhaust gas treatment catalysts, can solve the problems of insufficient catalytic oxidation capacity, insufficient high temperature resistance, deterioration of engine combustion efficiency, and poor back pressure control. , to achieve the effect of improving the utilization rate of precious metals, uniform distribution of precious metal particles, and low cost
- Summary
- Abstract
- Description
- Claims
- Application Information
AI Technical Summary
Problems solved by technology
Method used
Image
Examples
preparation example Construction
[0034] 1) For the preparation of the coating layer glue, add soluble aluminum salt or alumina according to a certain mass concentration requirement into the water-alcohol solvent system, the mass ratio to the solvent system is ≤30%, and then add 0.1wt% to 0.1% by weight of solvent 1wt% soluble acid, after the high-energy ball milling process, obtains the slurry A; the ionic mixed solution formed by the soluble salt of cerium and zirconium according to a certain molar ratio is added to the slurry A, and the slurry B is formed through electromagnetic stirring, Then the slurry B is aged and high-energy ultrasonic vibration is performed at the same time to form the glue C with gel particles.
[0035] 2) Coating of glue solution: dipping and coating glue solution C on the wall surface of the DPF air inlet of the wall-flow diesel particulate filter and into the pores in the wall, and blowing back with compressed airflow, that is, the airflow enters from the outlet end and removes Ex...
Embodiment 1
[0049] Coating slurry configuration, coating and precious metal particle impregnation process:
[0050] 1) Glue configuration: add pseudo-boehmite to deionized water at 20wt%, add 0.1wt% citric acid, and perform high-energy ball milling. The speed requirement is 1000r / min. After about 60min, add a mixture of cerium nitrate and zirconium nitrate Solution, the molar ratio of cerium nitrate and zirconium nitrate is 4:1, then continue to stir electromagnetically, the stirring rate is 200r / min, the time is about 30min, and finally aging, high-energy ultrasonic oscillation, working frequency 50KHz, power 100W, temperature control At 50° C., the solid content was adjusted to 15 wt % for 12 hours.
[0051] 2) Coating of glue solution: apply the aged glue solution to the wall surface of the air inlet of the wall-flow diesel particulate filter and the pores in the wall by dipping method, and blow back with compressed air flow, To remove excess glue, and then dry the coated DPF in a hot...
Embodiment 2
[0054] Coating slurry configuration, coating and precious metal particle impregnation process:
[0055] 1) Glue configuration: add pseudoboehmite to deionized water at 20wt%, add 1.0wt% citric acid, and perform high-energy ball milling. The speed requirement is 1000r / min. After about 60min, add a mixture of cerium nitrate and zirconium nitrate Solution, the molar ratio of cerium nitrate and zirconium nitrate is 1:1, then continue to stir electromagnetically, the stirring rate is 200r / min, the time is about 30min, and finally aging treatment, high-energy ultrasonic oscillation, working frequency 50KHz, power 100W, temperature The temperature is controlled at 50°C, the solid content is adjusted to 15wt%, and the time is 12h.
[0056] 2) Glue coating: the aged glue is dipped and coated on the wall surface of the air inlet of the wall-flow diesel particulate filter and in the pores in the wall by dipping method, and blown back with compressed airflow , to remove excess glue, and ...
PUM
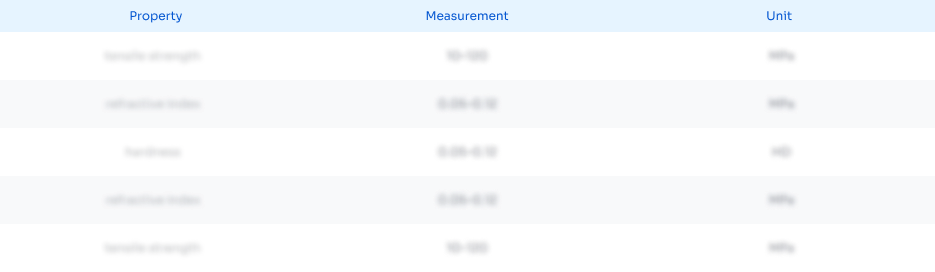
Abstract
Description
Claims
Application Information

- R&D Engineer
- R&D Manager
- IP Professional
- Industry Leading Data Capabilities
- Powerful AI technology
- Patent DNA Extraction
Browse by: Latest US Patents, China's latest patents, Technical Efficacy Thesaurus, Application Domain, Technology Topic, Popular Technical Reports.
© 2024 PatSnap. All rights reserved.Legal|Privacy policy|Modern Slavery Act Transparency Statement|Sitemap|About US| Contact US: help@patsnap.com