a mnse/cose 2 Composite material, preparation method and application thereof
A composite material and acetate technology, applied in the direction of structural parts, electrical components, battery electrodes, etc., can solve the problems of limited application, fast attenuation speed, poor cycle performance, etc., and achieve simple and easy process, high tap density, The effect of close contact
- Summary
- Abstract
- Description
- Claims
- Application Information
AI Technical Summary
Problems solved by technology
Method used
Image
Examples
Embodiment 1
[0031] Add manganese acetate, cobalt acetate, and urea into 10 mL of deionized water at a molar ratio of 1.2:2:9, and stir until clarification at room temperature. Add 20 mL of ethylene glycol into the prepared acetate solution, mix well, then transfer to a hydrothermal reaction kettle, and heat at 180° C. for 24 hours. The resulting product was centrifuged and washed several times with water and ethanol, then dried at 70°C. Then 0.2 g of the obtained precursor was placed adjacent to 2 g of selenium powder in a tube furnace, and the temperature was raised to 600 °C at a rate of 5 °C / min under a protective atmosphere, and then kept for 4 h to obtain a dumbbell-shaped MnSe / CoSe 2 composite material. Adopt Japanese science D / max-2500 type X-ray diffraction analyzer to analyze gained sample, obtained result is as follows figure 1 As shown, all the diffraction peaks of the product correspond to MnSe and CoSe 2 phase. No other impurity peaks were found, indicating that the purit...
Embodiment 2
[0033] Add manganese acetate, cobalt acetate, and urea into 10 mL of deionized water at a molar ratio of 1.2:2:9, and stir until clarification at room temperature. Add 20 mL of ethylene glycol into the prepared acetate solution, mix well, then transfer to a hydrothermal reaction kettle, and heat at 180° C. for 30 h. The resulting product was centrifuged and washed several times with water and ethanol, then dried at 70°C. Then 0.2 g of the obtained precursor and 4 g of selenium powder were placed adjacent to a tube furnace, and the temperature was raised to 500 °C at a rate of 5 °C / min under a protective atmosphere, and after another 6 h, a dumbbell-shaped MnSe / CoSe 2composite material. Observing the sample with a Nova NanoSEM230 scanning electron microscope from FEI Company in the United States, it was found that the dumbbell-shaped particles were self-assembled by many secondary particles and had a porous structure, such as Figure 4 shown.
Embodiment 3
[0035] Add manganese acetate, cobalt acetate, and urea into 10 mL of deionized water at a molar ratio of 1.2:5:20, and stir until clarification at room temperature. Add 20 mL of ethylene glycol into the prepared acetate solution, mix well, then transfer to a hydrothermal reaction kettle, and heat at 200°C for 24 hours. The resulting product was centrifuged and washed several times with water and ethanol, then dried at 70°C. Then 0.2 g of the obtained precursor was placed adjacent to 4 g of selenium powder in a tube furnace, and the heating rate was raised to 500 °C under a protective atmosphere at a rate of 5 °C / min, and then kept for 6 h to obtain a dumbbell-shaped MnSe / CoSe 2 composite material.
PUM
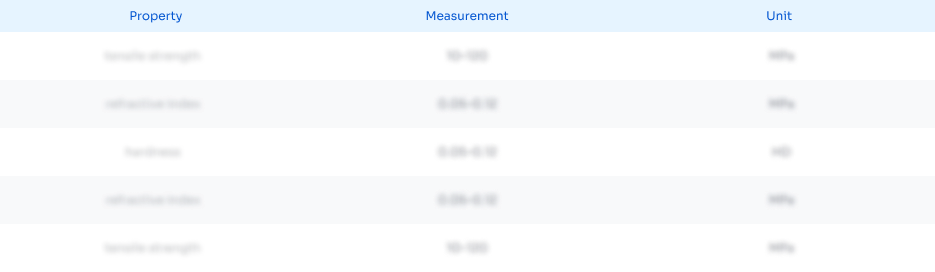
Abstract
Description
Claims
Application Information

- R&D Engineer
- R&D Manager
- IP Professional
- Industry Leading Data Capabilities
- Powerful AI technology
- Patent DNA Extraction
Browse by: Latest US Patents, China's latest patents, Technical Efficacy Thesaurus, Application Domain, Technology Topic, Popular Technical Reports.
© 2024 PatSnap. All rights reserved.Legal|Privacy policy|Modern Slavery Act Transparency Statement|Sitemap|About US| Contact US: help@patsnap.com