High-efficient creep age forming method for aluminum alloy
A technology of creep aging forming and aluminum alloy, which is applied in the field of precision forming of aluminum alloy components, can solve problems such as unfavorable components closely fitting with the mold surface, not satisfying the principle of economy, and long creep aging time, etc., to achieve convenient The effect of synergistic control of shape and property, excellent mechanical properties, improvement of forming accuracy and manufacturing efficiency
- Summary
- Abstract
- Description
- Claims
- Application Information
AI Technical Summary
Problems solved by technology
Method used
Image
Examples
Embodiment 1
[0026] 2219 aluminum alloy is subjected to solution treatment and water quenching in an air circulation resistance furnace to obtain an aluminum alloy plate; then cold rolled at room temperature to 80% of the deformation treatment to 8mm, and then the creep test is carried out in the creep machine. The aging temperature is 165°C, the creep time is 12h, and the creep stress is 150MPa. The tensile test is carried out after the plate is taken out and cooled at room temperature.
Embodiment 2
[0028] 2219 aluminum alloy is subjected to solution treatment and water quenching in an air circulation resistance furnace to obtain an aluminum alloy plate; then cold rolled at room temperature to 80% of the deformation treatment to 8mm, and then the creep test is carried out in the creep machine. The aging temperature is 165°C, the creep time is 12h, and the creep stress is 50MPa. The tensile test is carried out after the plate is taken out and cooled at room temperature.
Embodiment 3
[0030] 2219 aluminum alloy is subjected to solution treatment and water quenching in an air circulation resistance furnace to obtain an aluminum alloy plate; then cold rolled at room temperature to 80% of the deformation treatment to 8mm, and then the creep test is carried out in the creep machine. The aging temperature is 120°C, the creep time is 12h, and the creep stress is 150MPa. The tensile test is carried out after the plate is taken out and cooled at room temperature.
PUM
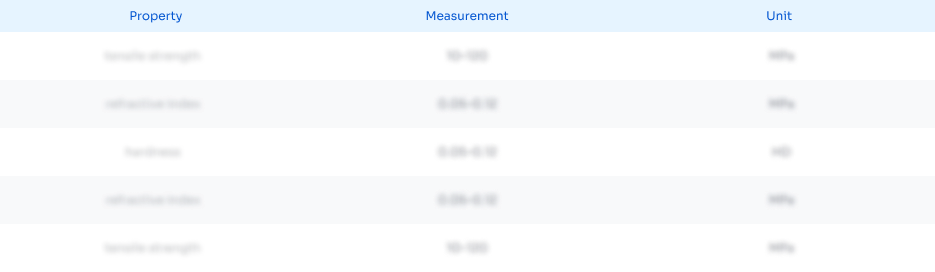
Abstract
Description
Claims
Application Information

- R&D
- Intellectual Property
- Life Sciences
- Materials
- Tech Scout
- Unparalleled Data Quality
- Higher Quality Content
- 60% Fewer Hallucinations
Browse by: Latest US Patents, China's latest patents, Technical Efficacy Thesaurus, Application Domain, Technology Topic, Popular Technical Reports.
© 2025 PatSnap. All rights reserved.Legal|Privacy policy|Modern Slavery Act Transparency Statement|Sitemap|About US| Contact US: help@patsnap.com