Method for growing metal carbide on metal surface
A metal carbide and surface growth technology, which is applied in metal material coating process, gaseous chemical plating, ion implantation plating, etc., can solve problems such as weak binding force, mismatched stress, and affecting the internal structure and performance of metals
- Summary
- Abstract
- Description
- Claims
- Application Information
AI Technical Summary
Problems solved by technology
Method used
Image
Examples
Embodiment 1
[0040] Example 1: 304 stainless steel sheet
[0041] 1. Place the target: put the tungsten target on the radio frequency table of the magnetron sputtering apparatus;
[0042] 2. Place the 304 stainless steel sheet: first clean the 304 stainless steel sheet, place the 304 stainless steel sheet in a beaker and immerse it in acetone, and ultrasonically clean it for at least 5 minutes; take out the 304 stainless steel sheet and place it in another beaker, immerse it in alcohol, and ultrasonically clean it for at least 5 minutes; take it out Place the 304 stainless steel sheet in another beaker and immerse it in deionized water, and ultrasonically clean it for at least 5 minutes; take out the 304 stainless steel sheet, rinse it with deionized water for at least 30 seconds, dry it, and then place the 304 stainless steel sheet on the sample stage;
[0043] 3. Adjust the position of the sample stage: adjust the distance d=50mm between the sample stage and the radio frequency stage;
...
Embodiment 2
[0058] Example 2: 304 stainless steel sheet
[0059] 1. Place the target: put the zirconium target on the radio frequency table of the magnetron sputtering apparatus;
[0060] 2. Place the 304 stainless steel sheet: first clean the 304 stainless steel sheet, place the 304 stainless steel sheet in a beaker and immerse it in acetone, and ultrasonically clean it for at least 5 minutes; take out the 304 stainless steel sheet and place it in another beaker, immerse it in alcohol, and ultrasonically clean it for at least 5 minutes; take it out Place the 304 stainless steel sheet in another beaker and immerse it in deionized water, and ultrasonically clean it for at least 5 minutes; take out the 304 stainless steel sheet, rinse it with deionized water for at least 30 seconds, dry it, and then place the 304 stainless steel sheet on the sample stage;
[0061] 3. Adjust the position of the sample stage: adjust the distance d=90mm between the sample stage and the radio frequency stage; ...
Embodiment 3
[0076] Embodiment 3: GH4169 superalloy foil
[0077] 1. Place the target: put the tungsten-zirconium alloy target on the radio frequency table of the magnetron sputtering apparatus;
[0078] 2. Place the GH4169 superalloy foil: first clean the GH4169 superalloy foil, place the GH4169 superalloy foil in a beaker and immerse it in acetone, and ultrasonically clean it for at least 5 minutes; take out the GH4169 superalloy foil and place it in another beaker, immerse it in alcohol, and ultrasonically clean it At least 5 minutes; take out the GH4169 superalloy foil and place it in another beaker, immerse it in deionized water, and ultrasonically clean it for at least 5 minutes; take out the GH4169 superalloy foil and rinse it with deionized water for at least 30 seconds, dry it, and then place the GH4169 superalloy foil on the sample on stage;
[0079] 3. Adjust the position of the sample stage: adjust the distance d=70mm between the sample stage and the radio frequency stage;
...
PUM
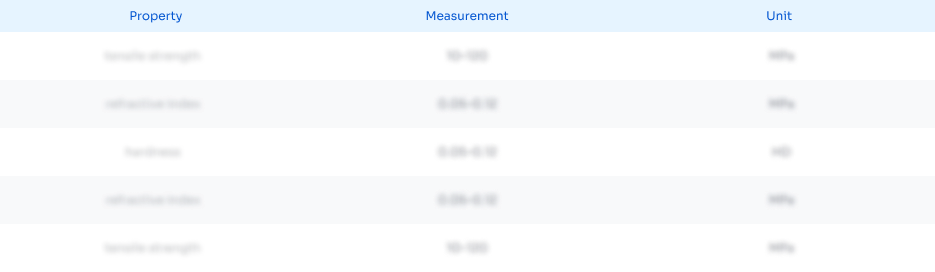
Abstract
Description
Claims
Application Information

- R&D
- Intellectual Property
- Life Sciences
- Materials
- Tech Scout
- Unparalleled Data Quality
- Higher Quality Content
- 60% Fewer Hallucinations
Browse by: Latest US Patents, China's latest patents, Technical Efficacy Thesaurus, Application Domain, Technology Topic, Popular Technical Reports.
© 2025 PatSnap. All rights reserved.Legal|Privacy policy|Modern Slavery Act Transparency Statement|Sitemap|About US| Contact US: help@patsnap.com