Preparation method of composite polymer electrolyte membrane and lithium ion battery
A technology of composite polymer and electrolyte membrane, which is applied in the direction of non-aqueous electrolyte battery, electrolyte battery manufacturing, solid electrolyte, etc., can solve the problem of poor electrochemical performance, poor electrochemical stability, liquid absorption rate and retention of lithium-ion batteries. Low liquid rate and other problems, achieve superior mechanical properties, overcome poor electrochemical stability, and good liquid retention rate
- Summary
- Abstract
- Description
- Claims
- Application Information
AI Technical Summary
Problems solved by technology
Method used
Image
Examples
preparation example Construction
[0022] The composite polymer electrolyte membrane of the present invention is a carbonate functionalized vinyl copolymer electrolyte membrane, and its preparation method comprises the following steps:
[0023] Stirring and mixing the carbonate-functionalized vinyl monomer and the polyether structural monomer with the solvent under an inert gas atmosphere, wherein the mass parts of the carbonate-functionalized vinyl monomer and the polyether structural monomer are respectively 10 to 50 parts and 50-90 parts, and then add the initiator, the mass part of the initiator is 0.1-1 part, react at a temperature of 50-100 °C, under the protection of an inert gas for 4-48 hours, dry and purify to obtain a carbonate functionalized vinyl copolymer;
[0024] Add the obtained carbonate-functionalized vinyl copolymer and inorganic filler into the solvent and stir and mix, the mass parts of carbonate-functionalized vinyl copolymer and inorganic filler are respectively 70-95 parts and 0-5 parts...
Embodiment 1
[0032] The preparation method of the composite semi-solid electrolyte membrane of this embodiment comprises the following steps:
[0033] 10 parts by mass of vinyl ethylene carbonate and 30 parts by mass of polyethylene glycol methyl ether methacrylate (molecular weight 300), 30 parts of methyl methacrylate and 30 parts of acrylonitrile are added to the reactor together with tetrahydrofuran. The reactor was continuously blown with nitrogen and kept stirring, then added 1 mass part of azobisisobutyronitrile, stirred at 50°C at a speed of 100r / min, reacted for 48h under the protection of an inert gas, and obtained carbonate after drying and purification Functionalized vinyl copolymers;
[0034] Add 80 parts by mass of carbonate-functionalized vinyl copolymer to 600 parts by mass of tetrahydrofuran, and stir at a speed of 3000r / min for 6h to obtain a uniformly mixed liquid;
[0035] The mixed solution was uniformly coated on a polytetrafluoroethylene mold, and then vacuum-dried ...
Embodiment 2
[0038] The preparation method of the electrolyte membrane of the present embodiment is as follows:
[0039]The allyl methyl carbonate of 50 mass parts and the polyethylene glycol methyl ether methacrylate (molecular weight 20000) of 10 mass parts, the polyethylene glycol methyl ether acrylate (molecular weight 480) of 10 mass parts and 30 Parts by mass of methyl methacrylate and methylpyrrolidone are added to the reactor, nitrogen is continuously fed into the reactor and stirred continuously, and then 0.5 parts by mass of benzoyl peroxide is added, at 100°C, at 600r / Min speed stirring, reaction 4h under the protection of inert gas, after drying and purifying, obtain carbonate functionalized vinyl copolymer;
[0040] Add 70 parts by mass of carbonate-functionalized vinyl copolymer and 2 parts by mass of nano-silica to 200 parts by mass of tetrahydrofuran, stir at a speed of 1000r / min for 2h, and obtain a uniformly mixed mixed solution;
[0041] The mixed solution was uniforml...
PUM
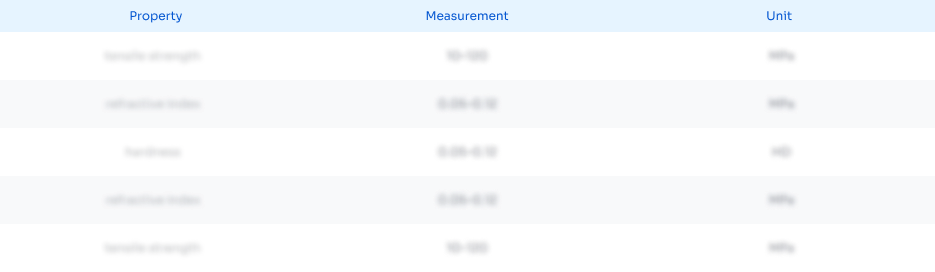
Abstract
Description
Claims
Application Information

- R&D Engineer
- R&D Manager
- IP Professional
- Industry Leading Data Capabilities
- Powerful AI technology
- Patent DNA Extraction
Browse by: Latest US Patents, China's latest patents, Technical Efficacy Thesaurus, Application Domain, Technology Topic, Popular Technical Reports.
© 2024 PatSnap. All rights reserved.Legal|Privacy policy|Modern Slavery Act Transparency Statement|Sitemap|About US| Contact US: help@patsnap.com