A method for optimal design of super austenitic stainless steel and its alloy composition
An austenitic stainless steel, optimized design technology, applied in the field of stainless steel, can solve the problems of poor high temperature thermoplasticity, easy cracking during rolling, high temperature oxidation and so on
- Summary
- Abstract
- Description
- Claims
- Application Information
AI Technical Summary
Problems solved by technology
Method used
Image
Examples
Embodiment 1
[0073] The preparation of embodiment 1 super austenitic stainless steel
[0074] The super austenitic stainless steel invented by 100kg induction furnace is smelted, and the marked furnace number is 1#~9#. At the same time, the comparison steel grade (254SMO) with furnace number 10# and the comparison steel grade with furnace number 11# ( 654SMO), the charging capacity is 80kg, the specific steps are as follows:
[0075] (1), smelting and casting ingots, the composition weight percentages of the ingots are as shown in Table 1 and Table 2, wherein % is the weight percentage content;
[0076] (2), heating the ingot to 1200±10°C, keeping it warm for 1-2 hours, and forging it into a super austenitic stainless steel forged plate;
[0077] (3) cutting out a part of the forged plate obtained in step (2), heating it to 1200±10° C., keeping it warm for 1 to 2 hours, and rolling it into a super austenitic stainless steel rolled plate through 6 to 7 passes of hot rolling;
[0078] (4) ...
Embodiment 2
[0085] Example 2 Super austenitic stainless steel structure stability
[0086] A number of 10×10mm samples were cut from the super austenitic stainless steel plate prepared according to Example 1 and the comparison steel, and after solution treatment at 1200°C for 1 hour, aged at 950°C for 30 minutes and 2 hours, respectively, and then water-cooled. Grind, polish and metallographically corrode the samples after aging treatment, observe the microstructure with a metallographic microscope, and use the software attached to the microscope to count the content of precipitates, which is used to evaluate the precipitation sensitivity and structure stability of each furnace steel . The lower the precipitated phase content, the weaker the precipitation sensitivity and the stronger the stability of the structure. Such as figure 1 Shown is the volume fraction of the precipitated phase in each furnace steel, as can be seen, the precipitated phase content is generally lower than the comp...
Embodiment 3
[0087] Embodiment 3 super austenitic stainless steel hot working performance
[0088] Cut on the super austenitic stainless steel wrought plate prepared by embodiment 1 and the comparison steel plate For rod-shaped tensile samples, use Gleebe 3800 thermal simulation testing machine to test the reduction of area of the samples at 900°C, 1050°C, and 1200°C to evaluate the high-temperature thermoplasticity and hot workability of each furnace steel. The higher the reduction of area, the better the high temperature thermoplasticity and hot processing performance. Such as figure 2 Shown is the reduction of area of each furnace steel, and it can be seen that at three temperatures, the reduction of area of steel grades 1# to 9# of the present invention is generally higher than that of comparative steel grades 10# (254SMO) and 11# ( 654SMO), especially steel 2# (0.0066% B, 0.036% RE, 0.045% (Ca+Mg), 0.13% (Nb+V+Ti)), 6# (0.0051% B, 0.053% RE, 0.035% (Ca+Mg), 0.10% (Nb+V+Ti))...
PUM
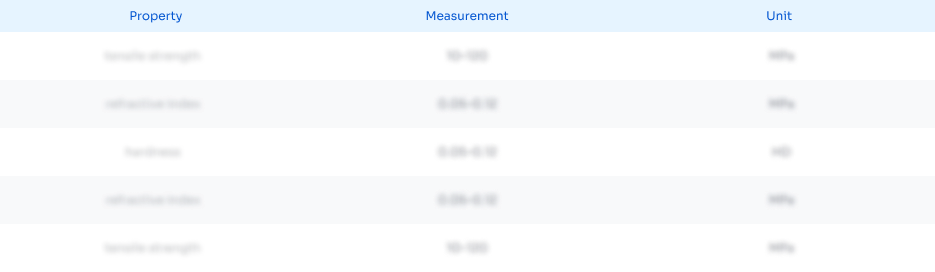
Abstract
Description
Claims
Application Information

- R&D Engineer
- R&D Manager
- IP Professional
- Industry Leading Data Capabilities
- Powerful AI technology
- Patent DNA Extraction
Browse by: Latest US Patents, China's latest patents, Technical Efficacy Thesaurus, Application Domain, Technology Topic, Popular Technical Reports.
© 2024 PatSnap. All rights reserved.Legal|Privacy policy|Modern Slavery Act Transparency Statement|Sitemap|About US| Contact US: help@patsnap.com