Poly(carbonate-ether) polyurethane emulsion for printing glue and preparation method thereof
A technology of polyurethane emulsion and carbonate, which is applied in dyeing, textile and paper making, and can solve the problems of mutual contact, high viscosity of polyurethane prepolymer, and high cost of raw materials
- Summary
- Abstract
- Description
- Claims
- Application Information
AI Technical Summary
Problems solved by technology
Method used
Image
Examples
Embodiment 1
[0037]9 parts of isophorone diisocyanate (IPDI), 7 parts of hexamethylene diisocyanate (HDI), 40 parts of poly(carbonate-ether) glycol (molecular weight 2500, polycarbonate unit 60%), polytetrahydrofuran 10 parts of polyol (molecular weight 1000), 2 parts of trimethylolpropane polyethylene glycol monomethyl ether (molecular weight 1000), 0.4 part of 1,4-butanediol, 1 part of sodium ethylenediaminoethanesulfonate, organic 0.03 part of bismuth catalyst, 45 parts of acetone, 50 parts of deionized water, 0.5 part of isophorone diamine;
[0038] Preparation:
[0039] (1) Heat poly(carbonate-ether) diol and polytetrahydrofuran diol to 100°C, remove water from the polyol under reduced pressure, cool down to 65°C in an inert atmosphere, add trimethylolpropane polyethylene glycol Alcohol monomethyl ether, 1,4-butanediol, diisocyanate and catalyst, react at 80°C for 3 hours, during the reaction, add acetone to adjust the viscosity of the reaction system to 3000-4000cp (45°C), measure N...
Embodiment 2
[0043] 10 parts of isophorone diisocyanate (IPDI), 6 parts of hexamethylene diisocyanate (HDI), 40 parts of poly(carbonate-ether) glycol (molecular weight 2500, polycarbonate unit 60%), polytetrahydrofuran 20 parts of polyol (molecular weight 2000), 4 parts of trimethylolpropane polyethylene glycol monomethyl ether (molecular weight 1200), 0.5 part of neopentyl glycol, 2.5 parts of sodium ethylenediaminoethanesulfonate, 0.03 parts of organic bismuth catalyst Parts, 55 parts of acetone, 52 parts of deionized water, 0.5 parts of ethylenediamine;
[0044] Preparation:
[0045] (1) Heat poly(carbonate-ether) diol and polytetrahydrofuran diol to 110°C, remove water from the polyol under reduced pressure, cool down to 70°C in an inert atmosphere, add trimethylolpropane polyethylene glycol Alcohol monomethyl ether, 1,4-butanediol, diisocyanate and catalyst, react at 90°C for 2h, during the reaction, add acetone to adjust the viscosity of the reaction system to 3000-4000cp (45°C), me...
Embodiment 3
[0049] 15 parts of isophorone diisocyanate (IPDI), 8 parts of hexamethylene diisocyanate (HDI), 35 parts of poly(carbonate-ether) glycol (molecular weight 2500, polycarbonate unit 60%), polytetrahydrofuran 20 parts of polyol (molecular weight 2000), 5 parts of trimethylolpropane polyethylene glycol monomethyl ether (molecular weight 1200), 1 part of neopentyl glycol, 2.5 parts of sodium ethylenediaminoethanesulfonate, organic bismuth catalyst 0.03 part, 58 parts of acetone, 55 parts of deionized water, 0.8 part of hydrazine hydrate;
[0050] The preparation method was the same as in Example 1 to obtain a poly(carbonate-ether) type aqueous polyurethane emulsion with a solid content of 60%.
PUM
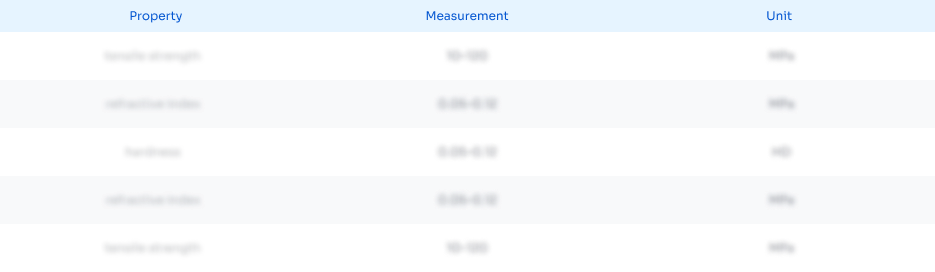
Abstract
Description
Claims
Application Information

- R&D
- Intellectual Property
- Life Sciences
- Materials
- Tech Scout
- Unparalleled Data Quality
- Higher Quality Content
- 60% Fewer Hallucinations
Browse by: Latest US Patents, China's latest patents, Technical Efficacy Thesaurus, Application Domain, Technology Topic, Popular Technical Reports.
© 2025 PatSnap. All rights reserved.Legal|Privacy policy|Modern Slavery Act Transparency Statement|Sitemap|About US| Contact US: help@patsnap.com