A method for preparing (meth)acrylic acid-3,4-epoxycyclohexylmethyl ester with a microchannel reactor
A technology of microchannel reactor and cyclohexenyl methyl ester, applied in the direction of organic chemistry, can solve the problems of continuous production difficulty, low product yield, high raw material cost, etc., and achieve the improvement of conversion rate and product selectivity, The effect of high product purity and the improvement of production economic benefits
- Summary
- Abstract
- Description
- Claims
- Application Information
AI Technical Summary
Problems solved by technology
Method used
Image
Examples
Embodiment 1
[0049] Esterification reaction: 58.8g of 3-cyclohexene-1-methanol, 0.05g of polymerization inhibitor p-hydroxyanisole, 50.6g of triethylamine and 300g of chloroform were sequentially added into a three-necked flask and stirred evenly to obtain solution 1. Solution 1 and 52.3g of methacryloyl chloride were pumped into the first mixer at a flow rate of 6.8mL / min: 1mL / min and mixed evenly, then entered the first microchannel reactor, and reacted for 22 minute. After the reaction is over, filter the salts generated by the reaction to obtain the intermediate methacrylate-3-cyclohexenyl methyl ester solution (solution two); this step solution can be directly used in the epoxidation reaction without vacuum distillation , simplifying the operation steps.
[0050] Epoxidation reaction: 10.7g of anhydrous sodium acetate was dissolved in 71.5g of 50% hydrogen peroxide (w / W) aqueous solution to obtain solution three; solution three and 75g of acetic anhydride were mixed at a flow rate of...
Embodiment 2
[0052] Esterification reaction: Add 58.8g of 3-cyclohexene-1-methanol, 0.05g of polymerization inhibitor p-hydroxyanisole, 50.6g of triethylamine and 300g of chloroform into a three-necked flask and stir evenly to obtain solution 1. Solution 1 and 45.2g of acryloyl chloride were pumped into the first mixer at a flow rate of 6.8mL / min: 1mL / min. After mixing, they entered the first microchannel reactor and reacted for 25 minutes at a temperature of 10°C. After the reaction, use a Buchner funnel to filter out the salt in the reaction solution to obtain a solution containing the intermediate 3-cyclohexenylmethyl acrylate (solution 2).
[0053] Epoxidation: 10.5g of anhydrous sodium acetate was dissolved in 72g of 50% hydrogen peroxide (w / w) aqueous solution to obtain solution three; solution three and 75g of acetic anhydride were respectively mixed at a flow rate of 1mL / min: 1mL / min After being pumped into the second mixer and mixed evenly, solution 4 was obtained; 367.5 g of solu...
Embodiment 3
[0056] The implementation conditions and steps are the same as in Example 1, except that the triethylamine in the esterification reaction is changed to 32% aqueous sodium hydroxide solution, the purity of methacrylic acid-3,4-epoxycyclohexylmethyl ester is 98.8%, and the molar yield 98.7%, 3-cyclohexenyl methyl methacrylate conversion rate 99.0%, product selectivity 99.7%.
[0057] The resulting product spectrogram is consistent with Example 1, so it is not provided repeatedly.
PUM
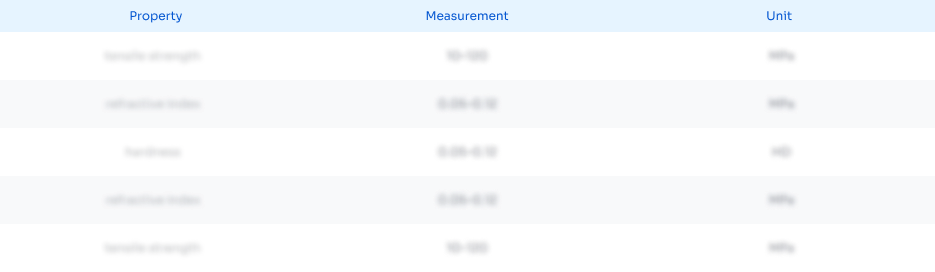
Abstract
Description
Claims
Application Information

- R&D Engineer
- R&D Manager
- IP Professional
- Industry Leading Data Capabilities
- Powerful AI technology
- Patent DNA Extraction
Browse by: Latest US Patents, China's latest patents, Technical Efficacy Thesaurus, Application Domain, Technology Topic, Popular Technical Reports.
© 2024 PatSnap. All rights reserved.Legal|Privacy policy|Modern Slavery Act Transparency Statement|Sitemap|About US| Contact US: help@patsnap.com