Method for recovering copper and cobalt from copper furnace slag
A technology for recovering copper and slag, applied in the field of metallurgy, can solve the problems of high cost and large consumption of sulfuric acid, and achieve the effect of low recovery cost and reduction of sulfuric acid consumption
- Summary
- Abstract
- Description
- Claims
- Application Information
AI Technical Summary
Problems solved by technology
Method used
Image
Examples
Embodiment 1
[0041] Take 200g of copper slag and grind it to -200 mesh, make a slurry according to the liquid-solid ratio of 3:1, then add 110g of sulfuric acid to it, stir and leaching at 80°C and normal pressure for 4 hours to perform pre-soaking.
[0042] Put the pre-impregnated slurry into the autoclave, the liquid-solid ratio is 6:1 (L / kg), the volume of the stock solution is 1200ml, after sealing, continue to feed oxygen into it, start stirring and heating, and the stirring speed is 800 rpm After heating up to 180°C with a total pressure of 1.2MPa (where the oxygen partial pressure is 0.3MPa), the temperature is maintained for 1.5 hours.
[0043] After the oxygen pressure leaching is completed, the temperature and pressure are lowered, and then the slurry is taken out from the autoclave, filtered and washed with a Buchner funnel to obtain the leaching solution, washing water and leaching residue, and then recover copper and cobalt from the leaching solution, and finally measure the le...
Embodiment 2
[0045] Take 200g of copper slag and grind it to -320 mesh, make a slurry according to the liquid-solid ratio of 4:1, then add 110g of sulfuric acid to it, stir and leaching at 80°C and normal pressure for 1 hour, and perform pre-soaking.
[0046] Put the pre-impregnated slurry into the autoclave, the liquid-solid ratio is 5:1, and the volume of the stock solution is 1000ml. After sealing, continue to feed oxygen into it, start stirring and start heating. The stirring speed is 800 rpm, and the temperature is raised to After 190°C and a total pressure of 1.46MPa (of which the partial pressure of oxygen is 0.3MPa), it is maintained for 1.5 hours.
[0047] After the oxygen pressure leaching is completed, the temperature and pressure are lowered, and then the slurry is taken out from the autoclave, filtered and washed with a Buchner funnel to obtain the leaching solution, washing water and leaching residue, and then copper and cobalt are recovered from the leaching solution, and fin...
Embodiment 3
[0049] Take 200g of copper slag and grind it to -320 mesh, make a slurry according to the liquid-solid ratio of 3.3:1, then add 110g of sulfuric acid to it, stir and leaching at 80°C and normal pressure for 1.5 hours, and perform pre-soaking.
[0050] Put the pre-impregnated slurry into the autoclave, the liquid-solid ratio is 5:1, and the volume of the stock solution is 1000ml. After sealing, oxygen is continuously introduced into it, stirring is started and heating is started. The stirring speed is 800 rpm, and the temperature is raised to After 230° C. and a total pressure of 3.1 MPa (of which the partial pressure of oxygen is 0.4 MPa), it is maintained for 1 hour.
[0051] After the oxygen pressure leaching is completed, the temperature and pressure are lowered, and then the slurry is taken out from the autoclave, filtered and washed with a Buchner funnel to obtain the leaching solution, washing water and leaching residue, and then copper and cobalt are recovered from the l...
PUM
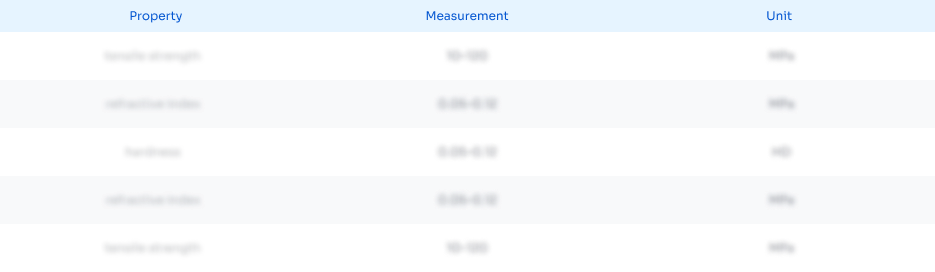
Abstract
Description
Claims
Application Information

- R&D Engineer
- R&D Manager
- IP Professional
- Industry Leading Data Capabilities
- Powerful AI technology
- Patent DNA Extraction
Browse by: Latest US Patents, China's latest patents, Technical Efficacy Thesaurus, Application Domain, Technology Topic, Popular Technical Reports.
© 2024 PatSnap. All rights reserved.Legal|Privacy policy|Modern Slavery Act Transparency Statement|Sitemap|About US| Contact US: help@patsnap.com