Graphite nickel plating method
A technology of nickel and graphite plating, applied in the field of electrochemistry, can solve the problems of wasting time, increasing the cost of graphite nickel plating, reducing the efficiency of nickel plating, etc., and achieving the effect of good electrical conductivity and tensile strength
- Summary
- Abstract
- Description
- Claims
- Application Information
AI Technical Summary
Problems solved by technology
Method used
Image
Examples
Embodiment 1
[0068] Embodiment 1 nickel-plated graphite powder
[0069] (1) Configure the electroless nickel plating solution: nickel sulfate hexahydrate 25g / L, lactic acid 30g / L, triethanolamine 18g / L, sodium citrate 20g / L, ammonium chloride 35g / L, sodium hypophosphite 45g / L, L-arginine 0.1mg / L, potassium ferrocyanide 5mg / L, adjusted to pH8.8 with ammonia water.
[0070] (2) Add graphite powder directly into the electroless nickel plating solution heated to 30°C, and mechanically stir for 10 minutes. After chemical reaction, a layer of electroless nickel-phosphorus alloy metal layer can be formed on the surface of graphite powder. After washing with running water and drying at 150°C for 10 minutes, good nickel-phosphorus alloy-plated graphite can be obtained.
[0071] figure 1 It is a process flow chart of nickel plating in Example 1 of the present invention.
Embodiment 2
[0073] The first step of electroless copper plating
[0074] (1) Configure the electroless copper plating solution: copper sulfate pentahydrate 8g / L, tetrasodium edetate 35g / L, sodium hydroxide 12g / L, formaldehyde 10mL / L, bipyridine 5mg / L, polyethylene glycol Alcohol 50mg / L.
[0075] (2) Add the graphite powder directly into the electroless copper plating solution at a temperature of about 30°C, and stir mechanically for 10 minutes. After a chemical reaction, a layer of chemical copper metal layer can be formed on the surface of the graphite powder.
[0076] The second step of electroless nickel plating
[0077] (1) Configure the electroless nickel plating solution: nickel sulfate hexahydrate 25g / L, lactic acid 30g / L, triethanolamine 18g / L, sodium citrate 20g / L, ammonium chloride 35g / L, sodium hypophosphite 45g / L, L-arginine 0.2mg / L, potassium ferrocyanide 10mg / L, ammonia water adjusted to PH8.8, etc.
[0078] (2) After the graphite powder of the electroless copper layer ha...
Embodiment 3
[0081] First Step Electroless Nickel Plating
[0082] (1) Add the graphite powder directly into the electroless nickel plating solution at a temperature of about 45°C, and stir it mechanically for 10 minutes. After a chemical reaction, a layer of chemical nickel-phosphorus alloy metal layer can be formed on the surface of the graphite powder.
[0083] (1) Configure the electroless nickel plating solution: The electroless nickel plating solution consists of nickel sulfate hexahydrate, lactic acid, triethanolamine, sodium citrate, ammonium chloride, sodium hypophosphite, stabilizer and the like. Dosage: nickel sulfate hexahydrate 25g / L, lactic acid 30g / L, triethanolamine 18g / L, sodium citrate 20g / L, ammonium chloride 35g / L, sodium hypophosphite 45g / L, L-arginine 0.01mg / L L, potassium ferrocyanide 0.1mg / L, ammonia water to adjust the pH to 8.8.
[0084] The second step configures electroless copper plating
[0085] (2) Configure the electroless copper plating solution: copper s...
PUM
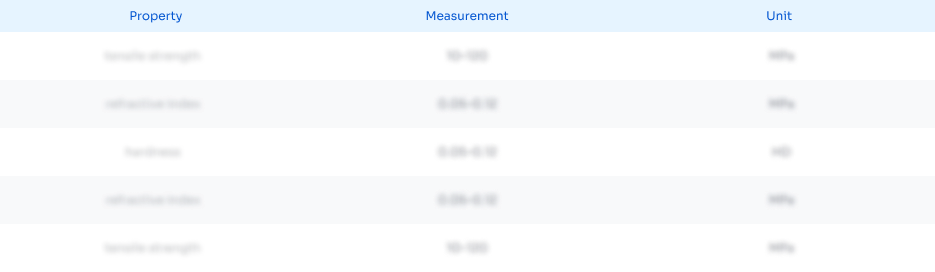
Abstract
Description
Claims
Application Information

- Generate Ideas
- Intellectual Property
- Life Sciences
- Materials
- Tech Scout
- Unparalleled Data Quality
- Higher Quality Content
- 60% Fewer Hallucinations
Browse by: Latest US Patents, China's latest patents, Technical Efficacy Thesaurus, Application Domain, Technology Topic, Popular Technical Reports.
© 2025 PatSnap. All rights reserved.Legal|Privacy policy|Modern Slavery Act Transparency Statement|Sitemap|About US| Contact US: help@patsnap.com