Solidified and modified epoxy resin composition containing side carboxyl hyperbranched polyarylether copolymer, preparation method and application thereof
A technology of epoxy resin and polyarylether, which is applied in the field of polymer material science, can solve problems such as poor toughening effect, poor compatibility, and poor stability, and achieve improved heat resistance and insulation, improved toughness, The effect of excellent comprehensive performance
- Summary
- Abstract
- Description
- Claims
- Application Information
AI Technical Summary
Problems solved by technology
Method used
Image
Examples
Embodiment 1
[0041] Add successively 0.9837 gram (0.0078mol) phloroglucinol, 5.8623 gram (0.0183mol) phenolphthalein, 6.546 gram (0.03mol) 4,4'-difluorobenzophenone, 12.4389 grams (0.09mol) of anhydrous potassium carbonate, 19 milliliters of dimethyl sulfoxide and 21 milliliters of toluene, heated to 140 ° C, after 2 hours, continued to heat up to 175 ° C for reaction 4 Hour. It is diluted with N,N-dimethylformamide, precipitated in ethanol, washed repeatedly with distilled water to remove inorganic salts, and dried to obtain a flocculent product, which is a hyperbranched polyarylether copolymer containing carboxyl side groups.
[0042] The carboxyl-containing side group hyperbranched polyarylether copolymer has a structure of formula (I), wherein
[0043] A is: B for C is
[0044] Dissolve carboxyl side group hyperbranched polyarylether copolymer, bisphenol A type epoxy resin E51 and 4-methyl-hexahydrophthalic anhydride, 2-ethyl-4-methylimidazole in tetrahydrofuran solvent to prep...
Embodiment 2
[0046] Dissolve carboxyl side group-containing hyperbranched polyarylether copolymer (structure shown below), bisphenol F diglycidyl ether, phthalic acid, and tetrabutylammonium bromide in tetrahydrofuran solvent to form a resin solution. Wherein the amount of the curing accelerator tetrabutylammonium bromide is 0.8% of the total weight of the epoxy resin composition. First, pour the resin solution into the mold, put it in a vacuum oven to remove air bubbles at room temperature, heat at 140°C for 1 hour, then heat at 155°C for 3 hours, and finally heat at 195°C for 2 hours. The glass transition temperature of the obtained epoxy resin composition was 130.9°C, and the temperature at the time of thermal weight loss of 5% was 259°C. Compared with before modification, the flexural strength increased by 61%, the flexural modulus increased by 20%, the flexural strain at break increased by 85%, the critical stress intensity factor increased by 32.1%, and the critical strain energy rel...
Embodiment 3
[0049] The carboxyl-containing side group hyperbranched polyarylether copolymer (structure shown below), alicyclic epoxy resin dicyclopentadiene diepoxide and hexahydrophthalic anhydride phthalic anhydride, 1,3,5-triethyl Base-hexahydro-S-triazine is dissolved in tetrahydrofuran solvent, is made into resin solution, wherein the amount of curing accelerator 1,3,5-triethyl-hexahydro-S-triazine is the total amount of epoxy resin composition 0.8% by weight. First pour the resin solution into the mold, put it in a vacuum oven to remove air bubbles at room temperature, and heat at 135°C for 2 hours, then at 160°C for 3 hours, and finally at 200°C for 1 hour. The glass transition temperature of the obtained epoxy resin composition was 130.9°C, and the temperature at the time of thermal weight loss of 5% was 259°C. Compared with before modification, the flexural strength increased by 61%, the flexural modulus increased by 20%, the flexural strain at break increased by 85%, the critic...
PUM
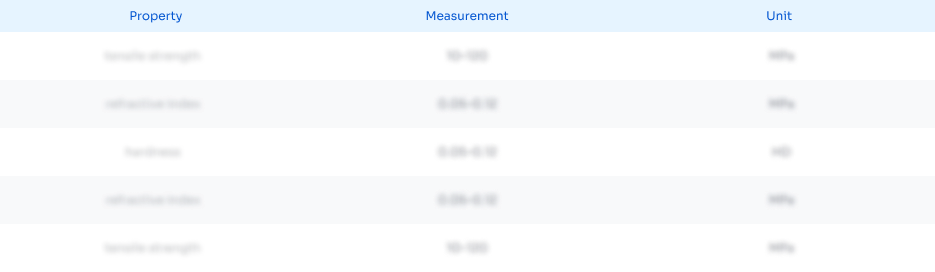
Abstract
Description
Claims
Application Information

- Generate Ideas
- Intellectual Property
- Life Sciences
- Materials
- Tech Scout
- Unparalleled Data Quality
- Higher Quality Content
- 60% Fewer Hallucinations
Browse by: Latest US Patents, China's latest patents, Technical Efficacy Thesaurus, Application Domain, Technology Topic, Popular Technical Reports.
© 2025 PatSnap. All rights reserved.Legal|Privacy policy|Modern Slavery Act Transparency Statement|Sitemap|About US| Contact US: help@patsnap.com