Novel method for anodic oxidation of beryllium aluminum alloy
A beryllium aluminum alloy, anodic oxidation technology, applied in anodic oxidation, electrolytic coating, surface reaction electrolytic coating, etc., can solve the problems of carcinogenicity, unclear process description, increase of actual process operation cost, etc., and achieve the effect of easy industrial production
- Summary
- Abstract
- Description
- Claims
- Application Information
AI Technical Summary
Problems solved by technology
Method used
Image
Examples
specific Embodiment approach
[0016] A new method of anodizing beryllium aluminum alloy, the method mainly consists of the following steps:
[0017] 1. The surface of the beryllium aluminum alloy material is processed by machining to improve the surface finish, and rinsed with deionized water repeatedly.
[0018] 2. For the beryllium aluminum alloy material that has been surface-treated in step 1, soak in an organic solution for 5-10 minutes in an air-circulating environment, and rinse with deionized water for 3 to 4 times after degreasing; The solution is: acetone, ethanol, kerosene, gasoline.
[0019] 3. The cleaned alloy material is subjected to a chemical degreasing process under certain temperature conditions, and the duration is 10-15s. The formula of chemical degreasing agent is: NaOH 10~25 g / L, Na 2 CO 3 20~30 g / L; the temperature condition of the whole degreasing process is between 40~50℃; after degreasing is finished, rinse with deionized water for 3 to 4 times.
[0020] 4. Use acidic solution to chemic...
PUM
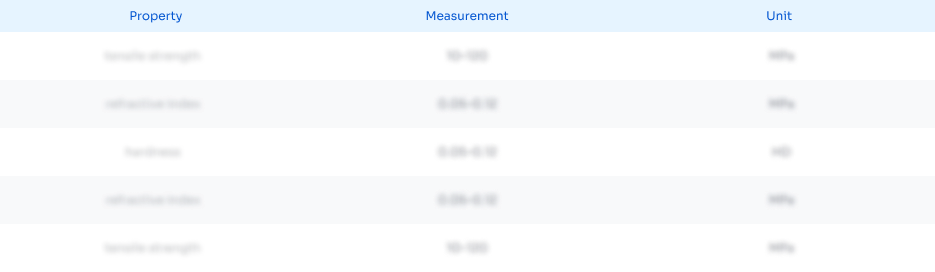
Abstract
Description
Claims
Application Information

- R&D Engineer
- R&D Manager
- IP Professional
- Industry Leading Data Capabilities
- Powerful AI technology
- Patent DNA Extraction
Browse by: Latest US Patents, China's latest patents, Technical Efficacy Thesaurus, Application Domain, Technology Topic, Popular Technical Reports.
© 2024 PatSnap. All rights reserved.Legal|Privacy policy|Modern Slavery Act Transparency Statement|Sitemap|About US| Contact US: help@patsnap.com