Polyamide modified melamine-formaldehyde prepolycondensate and foam material, and preparation methods thereof
A technology of precondensation polymers and foam materials, which is applied in the field of foam materials and preparation, and polyamide-modified melamine-formaldehyde precondensation polymers. Improved deformability, reduced process difficulty, and simple synthesis process
- Summary
- Abstract
- Description
- Claims
- Application Information
AI Technical Summary
Problems solved by technology
Method used
Image
Examples
preparation example Construction
[0039] A method for preparing a polyamide-modified melamine-formaldehyde precondensate, comprising the following steps: adding paraformaldehyde to deionized water, adjusting the pH value of the system to 9-11, raising the temperature to 75°C-80°C, adding melamine , polyamide and modifier, heat up to 85°C-110°C and react at constant temperature, when the cloud point reaches 30-45°C, stop heating and quickly cool down to below 40°C to obtain polyamide-modified melamine-formaldehyde precondensed polymer.
[0040] A polyamide-modified melamine-formaldehyde foam material, comprising the following components by mass:
[0041]
[0042] Further, a polyamide-modified melamine-formaldehyde foam material, comprising the following components in parts by mass:
[0043]
[0044] Further, the surfactant is one or more of anionic surfactant, nonionic surfactant or polymer surfactant. The selection of specific surfactants according to the invention helps to improve the mechanical prope...
example 1
[0059] The specific preparation process of the polyamide-modified melamine-formaldehyde foam of this example is as follows:
[0060] Add 500kg of paraformaldehyde to 520kg of water, adjust the pH of the system to 10.7 with alkali, heat up to 75°C, add 840kg of melamine, 16.8kg of methylol polyamide-66 and 84kg of sodium metabisulfite, heat up to 95°C and react at a constant temperature, turbid The progress of the reaction was monitored point by point, and when the cloud point reached 40°C, the heating was stopped and the temperature was rapidly lowered to below 40°C to obtain a methylol polyamide-modified melamine-formaldehyde resin precondensate.
[0061] 4000g methylol polyamide-66 modified melamine-formaldehyde resin, 80g sodium dodecylbenzenesulfonate, 80g octylphenol ethoxylate, 120g 1,2,2-trichloro-1,1- Difluoroethane, 120g of n-pentane, 140g of formic acid, and 200g of water were mixed and stirred evenly to obtain a homogeneous foaming solution; then the foaming solutio...
example 2
[0063] The specific preparation process of the polyamide-modified melamine-formaldehyde foam of this example is as follows:
[0064] Add 500kg of paraformaldehyde to 650kg of water, adjust the pH of the system to 10.0 with alkali, raise the temperature to 90°C, add 1050kg of melamine, 31.5kg of low-molecular-weight amino polyamide and 105kg of sodium sulfite, raise the temperature to 95°C and react at a constant temperature, and monitor the reaction at the cloud point process, when the cloud point reaches 40°C, stop heating and quickly cool down to below 40°C to prepare aminopolyamide-modified melamine-formaldehyde resin precondensate.
[0065] 4000g aminoamide modified melamine-formaldehyde resin, 80g sodium dodecylbenzenesulfonate, 80g octylphenol ethoxylate, 120g 1,2,2-trichloro-1,1-difluoroethane, 120g of n-pentane, 140g of formic acid, 40g of water, mixed and stirred evenly to obtain a homogeneous foaming liquid; then the foaming liquid was microwave foamed at 100°C for 5...
PUM
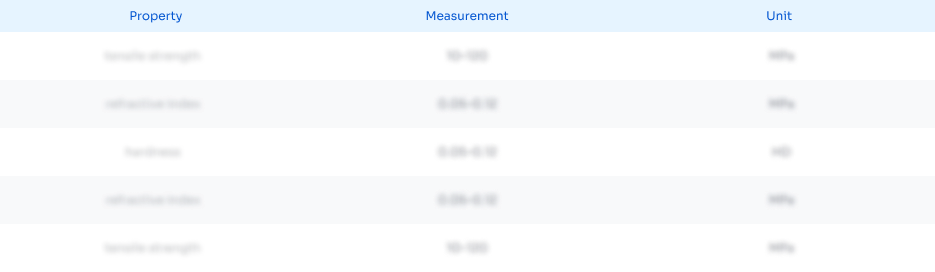
Abstract
Description
Claims
Application Information

- Generate Ideas
- Intellectual Property
- Life Sciences
- Materials
- Tech Scout
- Unparalleled Data Quality
- Higher Quality Content
- 60% Fewer Hallucinations
Browse by: Latest US Patents, China's latest patents, Technical Efficacy Thesaurus, Application Domain, Technology Topic, Popular Technical Reports.
© 2025 PatSnap. All rights reserved.Legal|Privacy policy|Modern Slavery Act Transparency Statement|Sitemap|About US| Contact US: help@patsnap.com