Preparation method of special cyanide-free zinc-plating brightener for sylvite system
A brightener and system technology, which is applied in the field of preparation of cyanide-free galvanized brightener, can solve the problems of narrow bright current density range, rough coating texture grains, and large difference in thickness of deposited layers, etc., to shorten production time, The effect of high bath current efficiency and high dispersion ability
- Summary
- Abstract
- Description
- Claims
- Application Information
AI Technical Summary
Problems solved by technology
Method used
Image
Examples
Embodiment 1-1
[0015] Add 13.6g of anisaldehyde, 45.8g of glacial acetic acid, and 300ml of water into the reaction vessel, then heat up to 40°C, add 10.5g of a saturated aqueous solution of sodium sulfite dropwise, and the addition time is 50 minutes; after the addition of the saturated aqueous solution of sodium sulfite is completed, the reactor The temperature of the temperature rises to 80°C, and the first step reaction intermediate can be obtained after 6 hours of heat preservation and stirring reaction at this temperature, and then 12.4g of phytic acid aqueous solution is slowly added dropwise to the first step reaction intermediate, dropwise The time is 30 minutes; after the dropwise addition, the reaction temperature is 70-90°C, the temperature is kept constant for 3-4 hours, and the cyanide-free zinc plating brightener is obtained after cooling and recovery.
Embodiment 1-2
[0017] Add 32.5g of veratraldehyde, 65.8g of glacial acetic acid, and 500ml of water into the reaction vessel, then heat up to 50°C, add 25.5g of a saturated aqueous solution of sodium metabisulfite dropwise, and the dropping time is 80 minutes; after the addition of the saturated aqueous solution of sodium metabisulfite is completed, Raise the temperature of the reactor to 85°C, keep stirring and react at this temperature for 10 hours to obtain the first step reaction intermediate, and then slowly add 28.6g of phytic acid aqueous solution to the first step reaction intermediate , The dropwise addition time is 30 minutes; after the dropwise addition, the reaction temperature is 70-90°C, the temperature is kept constant for 3-4 hours, and the cyanide-free zinc-plating brightener is obtained after cooling and recovery.
[0018] The special cyanide-free galvanizing brightener of potassium salt system of the present invention and the galvanizing effect and performance comparison of...
Embodiment 2-1
[0020]
[0021] The coating layer of the Hastelloy cell test piece is generally bright and lustrous between 0.5A / dm2-4A / dm2, and the coating layer is burnt and rough when it is above 4A / dm2. At a current density of 2A / dm2, the deposition rate is 0.2-0.35μm / min
PUM
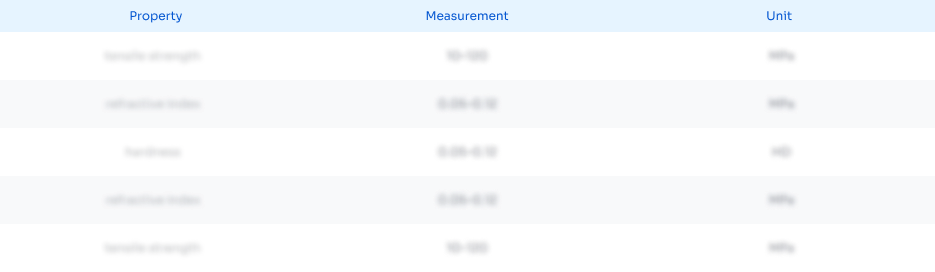
Abstract
Description
Claims
Application Information

- R&D
- Intellectual Property
- Life Sciences
- Materials
- Tech Scout
- Unparalleled Data Quality
- Higher Quality Content
- 60% Fewer Hallucinations
Browse by: Latest US Patents, China's latest patents, Technical Efficacy Thesaurus, Application Domain, Technology Topic, Popular Technical Reports.
© 2025 PatSnap. All rights reserved.Legal|Privacy policy|Modern Slavery Act Transparency Statement|Sitemap|About US| Contact US: help@patsnap.com