A kind of method of continuous production polyether amide
A technology of polyetheramide and caprolactam, which is applied in the field of continuous production of polyetheramide, can solve the problems of poor product uniformity, cost, quality and product disadvantage, achieve high structural uniformity, eliminate the concentration of terminal carboxyl groups, and reduce the risk of esterification reaction Effect
- Summary
- Abstract
- Description
- Claims
- Application Information
AI Technical Summary
Problems solved by technology
Method used
Image
Examples
Embodiment 1
[0069]A1. Mix the caprolactam melt, capping agent adipic acid and water uniformly and enter the pre-polymerization reactor to carry out the pre-polymerization reaction. The mass ratio of caprolactam melt, capping agent adipic acid and water is 92.6wt%:4.7 wt%: 2.7 wt%, the reaction temperature is 265° C., the reaction pressure is 200 kPa, and the reaction time is 4 h to obtain a carboxyl-terminated caprolactam prepolymer with a molecular weight of 3000.
[0070]A2. The carboxyl-terminated caprolactam prepolymer prepared in step A1 is mixed with the polyethylene glycol added online and the catalyst tetraisopropyl titanate through the high-shear homogenizing pump of the dynamic mixer, and then enters the falling film tower reaction The pre-polycondensation reaction is carried out in the reactor, wherein the molecular weight of the polyethylene glycol added online is 2000, the polyethylene glycol injection amount is 10wt% of the mass of the caprolactam prepolymer, and the injection amount...
Embodiment 2
[0074]A1. Mix the caprolactam melt, capping agent adipic acid and water uniformly and enter the pre-polymerization reactor for pre-polymerization reaction. The mass ratio of caprolactam melt, capping agent adipic acid and water is 75wt%:20wt% : 5wt%, the reaction temperature is 235°C, the reaction pressure is 600kPa, and the reaction time is 3h to obtain a carboxyl-terminated caprolactam prepolymer with a molecular weight of 550.
[0075]A2. The carboxyl-terminated caprolactam prepolymer prepared in step A1, the polypropylene glycol added online and the catalyst tetrapropyl zirconate are mixed uniformly through the high-shear homogenization pump of the dynamic mixer, and then enters the falling film tower reactor to proceed. Pre-polycondensation reaction, where the molecular weight of the polypropylene glycol added online is 4000, the injection amount of polypropylene glycol is 20wt% of the mass of the caprolactam prepolymer, the injection amount of the catalyst tetrapropyl zirconate i...
Embodiment 3
[0079]A1. Mix the caprolactam melt, capping agent adipic acid and water uniformly and enter the pre-polymerization reactor for the pre-polymerization reaction. The mass ratio of caprolactam melt, capping agent adipic acid and water is 98.0wt%: 1.5 wt%: 0.5wt%, the reaction temperature is 300° C., the reaction pressure is 100 kPa, and the reaction time is 10 h to obtain a carboxyl-terminated caprolactam prepolymer with a molecular weight of 10,000.
[0080]A2. The carboxyl-terminated caprolactam prepolymer prepared in step A1 is mixed with the polyethylene glycol added online and the catalyst tetrabutyl titanate uniformly through the dynamic mixer screw extruder, and then enters the falling film tower reactor for pretreatment. Polycondensation reaction, where the molecular weight of the polyethylene glycol added online is 10,000, the polyethylene glycol injection amount is 40wt% of the mass of the caprolactam prepolymer, and the injection amount of the catalyst tetraisopropyl titanate i...
PUM
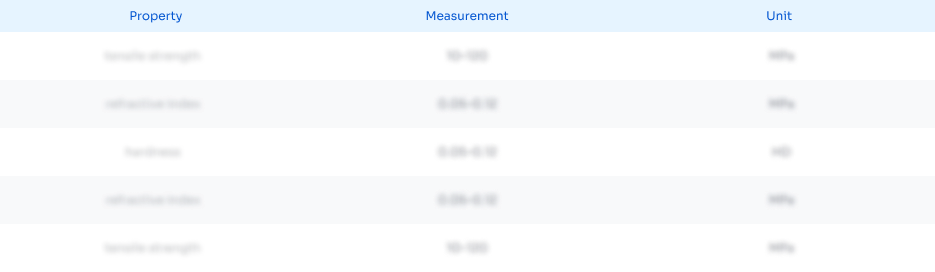
Abstract
Description
Claims
Application Information

- R&D
- Intellectual Property
- Life Sciences
- Materials
- Tech Scout
- Unparalleled Data Quality
- Higher Quality Content
- 60% Fewer Hallucinations
Browse by: Latest US Patents, China's latest patents, Technical Efficacy Thesaurus, Application Domain, Technology Topic, Popular Technical Reports.
© 2025 PatSnap. All rights reserved.Legal|Privacy policy|Modern Slavery Act Transparency Statement|Sitemap|About US| Contact US: help@patsnap.com