Electrocoppering method
A technology of electroplating copper and electroplating solution, which is applied to circuits, semiconductor devices, etc., can solve the problems of bump electromigration performance degradation, reliability degradation, and rough interface between electroplating layers, so as to shorten the electroplating process time and chemical mechanical polishing process time, reduced copper film thickness, and the effects of high fill rates
- Summary
- Abstract
- Description
- Claims
- Application Information
AI Technical Summary
Problems solved by technology
Method used
Examples
Embodiment 1
[0016] A kind of copper electroplating method of the present invention, comprises the following steps:
[0017] The first step, before the chemical plating process of the chip, the wafer groove is ultrasonically oscillated or washed with deionized water to fill it with deionized water. Fill the wafer trench with deionized water;
[0018] Second step, prepare electroplating solution, described electroplating solution comprises: copper sulfate is 50 / liter, and sulfuric acid is 50 grams / liter, and chloride ion is 10 mg / liter, and suppressor is 5 mg / liter, and accelerator is 5 milligrams / liter, the leveling agent is 0.5 mg / liter, and the rest is deionized water;
[0019] The third step, the initial condition electroplating process parameters are: time: 10 seconds, current density: 0.8 ampere / dm2, silicon wafer rotation speed: 5 rpm, electroplating solution flow rate: 4 liters / min, silicon wafer process position: 5 mm.
[0020] The fourth step, the electroplating process par...
Embodiment 2
[0024] A method for electroplating copper, comprising the steps of:
[0025] The first step, before the chemical plating process of the chip, the wafer groove is ultrasonically oscillated or washed with deionized water to fill it with deionized water. Fill the wafer trench with deionized water;
[0026] Second step, prepare electroplating solution, described electroplating solution comprises: copper sulfate is 150 grams / liter, and sulfuric acid is 150 grams / liter, and chloride ion is 100 mg / liter, and suppressor is 80 mg / liter, and accelerator is 30 mg / L, the leveling agent is 8 mg / L, and the rest is deionized water;
[0027] The third step, the initial condition electroplating process parameters are: time: 25 seconds, current density: 1 ampere / square decimeter, silicon wafer rotation speed: 10 rpm, electroplating solution flow rate: 5 liters / min, silicon wafer process position: 8mm.
[0028] The fourth step, the electroplating process parameters in the transition stage are...
Embodiment 3
[0032] A method for electroplating copper, comprising the steps of:
[0033] The first step, before the chemical plating process of the chip, the wafer groove is ultrasonically oscillated or washed with deionized water to fill it with deionized water. Fill the wafer trench with deionized water;
[0034] Second step, prepare electroplating solution, described electroplating solution comprises: copper sulfate is 200 grams / liter, and sulfuric acid is 220 grams / liter, and chloride ion is 150 mg / liter, and suppressor is 200 mg / liter, and accelerator is 50 mg / L, the leveling agent is 20 mg / L, and the rest is deionized water;
[0035] The third step, the initial condition electroplating process parameters are: time: 50 seconds, current density: 3 amps / dm2, silicon wafer rotation speed: 30 rpm, electroplating solution flow rate: 10 liters / min, silicon wafer process position: 10 mm.
[0036] The fourth step, the electroplating process parameters in the transition stage are: time: 10...
PUM
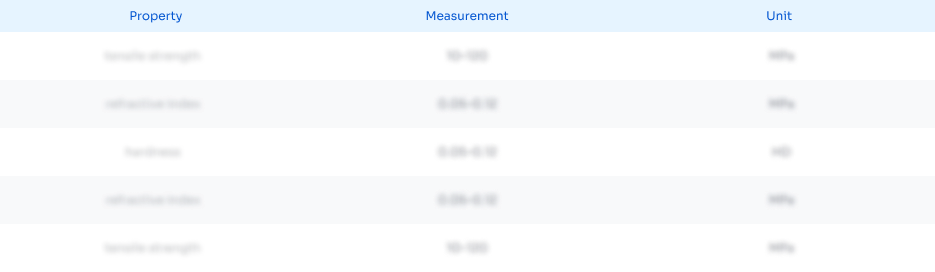
Abstract
Description
Claims
Application Information

- Generate Ideas
- Intellectual Property
- Life Sciences
- Materials
- Tech Scout
- Unparalleled Data Quality
- Higher Quality Content
- 60% Fewer Hallucinations
Browse by: Latest US Patents, China's latest patents, Technical Efficacy Thesaurus, Application Domain, Technology Topic, Popular Technical Reports.
© 2025 PatSnap. All rights reserved.Legal|Privacy policy|Modern Slavery Act Transparency Statement|Sitemap|About US| Contact US: help@patsnap.com