Method for recovering indium from indium-contained materials in zinc smelting
A zinc smelting and material technology, applied in the field of recovering indium, can solve the problems of difficult to solve emulsification problems, long process flow, high production cost, and achieve the effects of no emulsification phenomenon, accelerated reaction rate and high recovery rate.
- Summary
- Abstract
- Description
- Claims
- Application Information
AI Technical Summary
Problems solved by technology
Method used
Examples
Embodiment 1
[0026] The method for recovering indium from the indium-containing material of zinc smelting of the present invention comprises the following steps:
[0027] Under microwave conditions, heat 500L of reducing leaching solution to 80°C. Under ultrasonic conditions, light calcium carbonate is slurried and slowly added until the final pH is 5.0. After 1 hour of reaction, liquid-solid separation is carried out, and the output contains In 4500g / t. The first gypsum slag with 2.43wt% Zn and 3.68wt% Fe.
[0028] The first gypsum slag was leached with zinc electrolytic waste solution for 2 hours at a temperature of 75°C to obtain an indium-rich solution and a second gypsum slag. The initial sulfuric acid concentration of the zinc electrolysis waste liquid is 95g / L, and the liquid-solid ratio of the indium-rich slag and the zinc electrolysis waste liquid is 4L / Kg. Among them, the main chemical components of the indium-rich solution are: Zn 55.27g / L, Fe 15.92g / L, Fe 2+ 11.40g / L, Fe 3+...
Embodiment 2
[0032] The method for recovering indium from the indium-containing material of zinc smelting of the present invention comprises the following steps:
[0033] Under microwave conditions, heat 400L of reducing leaching solution to 90°C. Under ultrasonic conditions, light calcium carbonate is slurried and slowly added until the final pH is 5.0. After 0.5 hours of reaction, liquid-solid separation is carried out, and the output contains In4610g / t, Zn3.06wt%, Fe3.64wt% first gypsum slag.
[0034] The first gypsum slag was leached with zinc electrolysis waste solution for 4 hours at a temperature of 60° C. to obtain an indium-rich solution and a second gypsum slag. The initial sulfuric acid concentration of the zinc electrolysis waste liquid is 90g / L, and the liquid-solid ratio between the indium-rich slag and the zinc electrolysis waste liquid is 3.5L / Kg. Among them, the main chemical components of the indium-rich solution are: Zn 58.72g / L, Fe 16.03g / L, Fe 2+ 10.90g / L, Fe 3+ 5....
Embodiment 3
[0038] The method for recovering indium from the indium-containing material of zinc smelting of the present invention comprises the following steps:
[0039] Under microwave conditions, heat 600L reduction leaching solution to 85°C. Under ultrasonic conditions, light calcium carbonate is slurried and slowly added until the final pH is 5.0. After 1 hour of reaction, liquid-solid separation is carried out, and the output contains In 4465g / t, Zn 2.87wt%, Fe3.13wt% first gypsum slag.
[0040] The first gypsum slag was leached with zinc electrolytic waste solution for 1 hour at a temperature of 85° C. to obtain an indium-rich solution and a second gypsum slag. The initial sulfuric acid concentration of the zinc electrolysis waste liquid is 110g / L, and the liquid-solid ratio of the indium-rich slag and the zinc electrolysis waste liquid is 5L / Kg. Among them, the main chemical components of the indium-rich solution are: Zn 53.64g / L, Fe 15.73g / L, Fe 2+ 11.40g / L, Fe 3+ 4.66g / L, In 1....
PUM
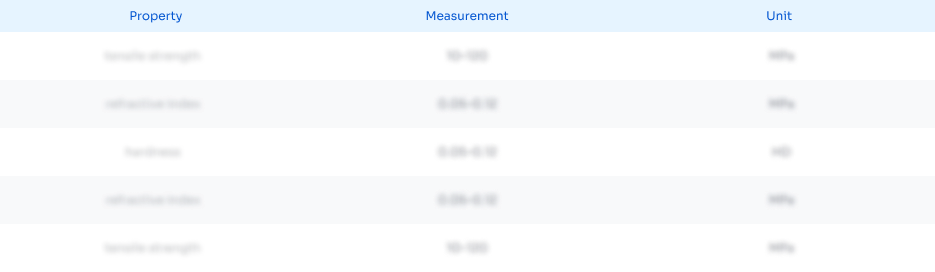
Abstract
Description
Claims
Application Information

- R&D Engineer
- R&D Manager
- IP Professional
- Industry Leading Data Capabilities
- Powerful AI technology
- Patent DNA Extraction
Browse by: Latest US Patents, China's latest patents, Technical Efficacy Thesaurus, Application Domain, Technology Topic, Popular Technical Reports.
© 2024 PatSnap. All rights reserved.Legal|Privacy policy|Modern Slavery Act Transparency Statement|Sitemap|About US| Contact US: help@patsnap.com