Method for producing aramid fiber fibrid
A kind of technology of aramid fiber and production method, applied in the field of polymer, can solve the problem of no national standard, achieve the effect of stable quality, simplify the process flow, and broaden the application field
- Summary
- Abstract
- Description
- Claims
- Application Information
AI Technical Summary
Problems solved by technology
Method used
Image
Examples
Embodiment 1
[0067] Resin synthesis and dilution: put 200Kg of dimethylacetamide solvent, 12.2Kg of m-phenylenediamine, and 9.4Kg of p-phenylenediamine into a 1000L polymerization reactor, start stirring under the protection of nitrogen and fully dissolve them, then put them into the jacket of the polymerization reactor Feed into the refrigerated liquid to reduce the temperature in the kettle to -9°C. At this time, adjust the stirring speed of the polymerization reactor to 280 rpm, keep the circulation of the refrigerated liquid, and put 40.6Kg of isophthaloyl chloride into the polymerization reactor for reaction. When the thick viscosity is 1100, add dimethylacetamide to the polymerization reactor to dilute and terminate the reaction. The polymerization reaction lasts for 20 minutes. When the polymer solution is diluted to a reduced viscosity of 120, stop adding solvent. Add 14.8Kg calcium hydroxide to carry out neutralization reaction in the polymerization kettle.
[0068] Coagulation so...
Embodiment 2
[0072] Resin synthesis and dilution: Put 200Kg of dimethylacetamide solvent, 16.2Kg of m-phenylenediamine, 5.4Kg of p-phenylenediamine into a 1000L polymerization reactor, turn on the stirring under the protection of nitrogen and fully dissolve it, then put it into the jacket of the polymerization reactor Feed into the refrigerated liquid to reduce the temperature in the kettle to -9°C. At this time, adjust the stirring speed of the polymerization reactor to 280 rpm, keep the circulation of the refrigerated liquid, and put 40.6Kg of isophthaloyl chloride into the polymerization reactor for reaction. When the thick viscosity is 1200, add dimethylacetamide to the polymerization reactor to dilute and terminate the reaction. The polymerization reaction takes 23 minutes. When the polymer solution is diluted to a reduced viscosity of 150, stop adding solvent. Add 14.8Kg calcium hydroxide to carry out neutralization reaction in polymerization reactor.
[0073] Coagulation solution pr...
Embodiment 3
[0077] Resin synthesis and dilution: Put 200Kg of dimethylacetamide solvent, 19.2Kg of m-phenylenediamine, and 2.4Kg of p-phenylenediamine into a 1000L polymerization reactor, start stirring under nitrogen protection and fully dissolve it, then put it into the jacket of the polymerization reactor Feed into the refrigerated liquid to reduce the temperature in the kettle to -9°C. At this time, adjust the stirring speed of the polymerization reactor to 280 rpm, keep the circulation of the refrigerated liquid, and put 40.6Kg of isophthaloyl chloride into the polymerization reactor for reaction. When the thick viscosity is 1400, add dimethylacetamide to the polymerization reactor to dilute and terminate the reaction. The polymerization reaction lasts for 25 minutes. When the polymer solution is diluted to a reduced viscosity of 180, stop adding solvent. Add 14.8Kg calcium hydroxide to carry out neutralization reaction in polymerization reactor.
[0078] Coagulation solution prepara...
PUM
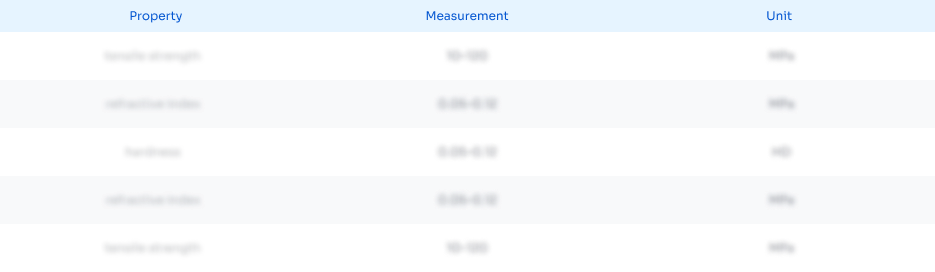
Abstract
Description
Claims
Application Information

- Generate Ideas
- Intellectual Property
- Life Sciences
- Materials
- Tech Scout
- Unparalleled Data Quality
- Higher Quality Content
- 60% Fewer Hallucinations
Browse by: Latest US Patents, China's latest patents, Technical Efficacy Thesaurus, Application Domain, Technology Topic, Popular Technical Reports.
© 2025 PatSnap. All rights reserved.Legal|Privacy policy|Modern Slavery Act Transparency Statement|Sitemap|About US| Contact US: help@patsnap.com