Thin-shell structure zirconium oxide powder for thermal spraying
A technology of zirconia powder and thin shell structure, which is applied in coating, fusion spraying, metal material coating process, etc., can solve the difficulty of heat protection of non-spraying parts of the workpiece, the increase of nozzle and electrode consumption speed, and the decrease of production cost Advanced problems, to achieve the effect of increasing contact heat transfer area, reducing spraying power and improving production efficiency
- Summary
- Abstract
- Description
- Claims
- Application Information
AI Technical Summary
Problems solved by technology
Method used
Image
Examples
Embodiment 1
[0018] Using the thin shell structure yttrium oxide partially stabilized zirconia powder of the present invention and the commercially available zirconia powder, the zirconia high-temperature thermal insulation coating was prepared under the same equipment to compare its process performance and final coating performance.
[0019] The thin-shell structure zirconia powder of the present invention has a wall thickness of about 8% of its outer diameter, and the commercially available zirconia powder is Metco 204NS, and the spraying equipment adopted is Metco 9MB plasma spraying equipment, and the spraying process parameters adopted are as follows: , the best spraying parameters obtained through orthogonal experiment optimization. The spraying parameters used and the typical coating performance comparison are shown in Table 1 below:
[0020] Table 1 Comparison of spraying process parameters and coating properties of the two powders
[0021]
[0022] Note 1: The bonding strength...
Embodiment 2
[0026] The thin-shell structure yttria partially stabilized zirconia ceramic powder of the present invention has a wall thickness of about 3% of its outer diameter. A commercially available oxyacetylene flame spray gun was used to prepare the thermal insulation coating, and the spraying parameters were optimized through orthogonal experiments. The spraying parameters and typical coating properties used are shown in Table 2 below:
[0027] Table 2 Oxyacetylene flame spraying process parameters and coating properties of thin shell structure zirconia powder
[0028]
[0029] It can be seen from the above table that the zirconia thermal insulation coating can be prepared by using the ordinary oxyacetylene flame spray gun and the thin-shell structure zirconia powder of the present invention, which not only has low equipment cost, but also has lower thermal conductivity. rate, and its heat insulation effect is better. The low thermal conductivity of the coating is mainly due to ...
Embodiment 3
[0031] Using the zirconia powder containing ytterbium oxide, gadolinia and yttrium oxide in the thin shell structure of the present invention, its wall thickness is about 8.7% of its outer diameter, compared with the zirconia powder of ytterbium oxide, gadolinia and yttrium oxide in the traditional structure Coating properties. The spraying equipment used is Metco 9MB plasma spraying equipment, and the spraying process parameters used are the best spraying parameters obtained through orthogonal experiment optimization. The comparison of spraying parameters and typical coating performance is shown in Table 3 below:
[0032] Table 3 Comparison of spraying process parameters and coating properties of the two powders
[0033]
[0034] It can be seen from the above table that compared with the traditional powder, the use of the thin-shell structure powder of the present invention has obvious advantages in terms of spraying power, production efficiency (powder feeding rate), and...
PUM
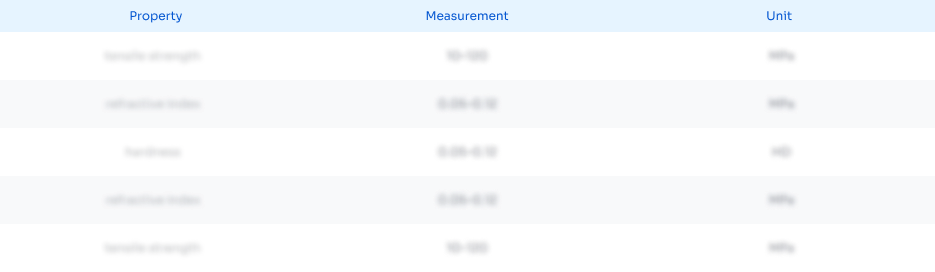
Abstract
Description
Claims
Application Information

- R&D Engineer
- R&D Manager
- IP Professional
- Industry Leading Data Capabilities
- Powerful AI technology
- Patent DNA Extraction
Browse by: Latest US Patents, China's latest patents, Technical Efficacy Thesaurus, Application Domain, Technology Topic, Popular Technical Reports.
© 2024 PatSnap. All rights reserved.Legal|Privacy policy|Modern Slavery Act Transparency Statement|Sitemap|About US| Contact US: help@patsnap.com