Preparation technology of corrosion-resistant aluminum alloy material and corrosion-resistant aluminum alloy material
A corrosion-resistant aluminum alloy and a preparation process technology are applied in the preparation process of corrosion-resistant aluminum alloy materials and the field of corrosion-resistant aluminum alloy materials, and can solve the problems of weak oxidation resistance and corrosion resistance, unenvironmentally friendly production process, and short service life. , to achieve the effect of strong oxidation resistance and corrosion resistance, long service life and high hardness
- Summary
- Abstract
- Description
- Claims
- Application Information
AI Technical Summary
Problems solved by technology
Method used
Examples
preparation example Construction
[0023] The preparation process of the corrosion-resistant aluminum alloy material comprises the following steps:
[0024] S1. Smelting: After cleaning the prepared materials, they are smelted by casting aluminum alloy smelting method. First, silicon nitride, borax, aluminum, copper, and diatomaceous earth are melted. After melting, stir evenly and then add ferromolybdenum, manganese, Yttrium, titanium, chromium, nickel, inject graphene, trisodium phosphate, acrylic regulator, p-hydroxybenzenesulfonic acid, dispersant POLYRON, 701 powder enhancer after the chemical clearing. Constant temperature smelting under the conditions of 420-580W, temperature 65-75°C, and rotation speed 160-310r / min to obtain a crude aluminum alloy melt by constant temperature smelting for 45-70min;
[0025] S2. Refining: when the temperature reaches 750-800°C, the aluminum alloy crude melt is refined: the scum on the surface of the aluminum alloy crude melt in the furnace is cleaned, and it will be bake...
Embodiment 1
[0030] A corrosion-resistant aluminum alloy material, in parts by weight, comprising the following raw materials: 12 parts of silicon nitride, 25 parts of ferromolybdenum, 14 parts of copper, 1.2 parts of graphene, 9 parts of manganese, 8 parts of yttrium, 18 parts of titanium, 12 parts of borax, 20 parts of chromium, 8 parts of nickel, 8 parts of diatomaceous earth, 2 parts of trisodium phosphate, 1 part of acrylate regulator, 2 parts of p-hydroxybenzenesulfonic acid, 2 parts of dispersant POLYRON, 701 powder enhancer 2 parts and aluminum 180 parts;
[0031] The preparation process of the corrosion-resistant aluminum alloy material comprises the following steps:
[0032] S1. Smelting: After cleaning the prepared materials, they are smelted by casting aluminum alloy smelting method. First, silicon nitride, borax, aluminum, copper, and diatomaceous earth are melted. After melting, stir evenly and then add ferromolybdenum, manganese, Yttrium, titanium, chromium, nickel, inject ...
Embodiment 2
[0037] A corrosion-resistant aluminum alloy material, in parts by weight, comprising the following raw materials: 14 parts of silicon nitride, 27 parts of ferromolybdenum, 16 parts of copper, 1.4 parts of graphene, 11 parts of manganese, 9 parts of yttrium, 20 parts of titanium, 14 parts of borax, 21 parts of chromium, 10 parts of nickel, 9 parts of diatomaceous earth, 2 parts of trisodium phosphate, 1 part of acrylate regulator, 2 parts of p-hydroxybenzenesulfonic acid, 2 parts of dispersant POLYRON, 701 powder enhancer 2 parts and aluminum 195 parts;
[0038] The preparation process of the corrosion-resistant aluminum alloy material comprises the following steps:
[0039] S1. Smelting: After cleaning the prepared materials, they are smelted by casting aluminum alloy smelting method. First, silicon nitride, borax, aluminum, copper, and diatomaceous earth are melted. After melting, stir evenly and then add ferromolybdenum, manganese, Yttrium, titanium, chromium, nickel, injec...
PUM
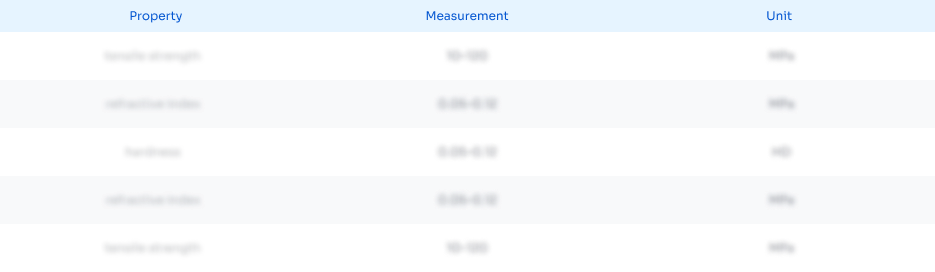
Abstract
Description
Claims
Application Information

- R&D
- Intellectual Property
- Life Sciences
- Materials
- Tech Scout
- Unparalleled Data Quality
- Higher Quality Content
- 60% Fewer Hallucinations
Browse by: Latest US Patents, China's latest patents, Technical Efficacy Thesaurus, Application Domain, Technology Topic, Popular Technical Reports.
© 2025 PatSnap. All rights reserved.Legal|Privacy policy|Modern Slavery Act Transparency Statement|Sitemap|About US| Contact US: help@patsnap.com