Heat treatment process of stator core for air conditioner
A stator core and process technology, applied in the field of heat treatment, can solve the problems of unsatisfactory heat treatment effect, poor internal stress relief effect, inability to recover well and improve the magnetic properties of the stator core, so as to improve the effect of stress relief, Excellent anti-rust and anti-corrosion properties, improved compactness and stability
- Summary
- Abstract
- Description
- Claims
- Application Information
AI Technical Summary
Problems solved by technology
Method used
Examples
Embodiment 1
[0021] A kind of air-conditioning stator core heat treatment process that the present invention proposes comprises the following steps:
[0022] (1) Burning oil: Put the stator core in a heating furnace, raise the temperature from room temperature to 450°C under the condition of nitrogen gas, and keep it warm for 120 minutes to remove the stamping oil on its surface;
[0023] (2) Annealing: Put the deoiled stator core in the annealing furnace, raise the temperature to 720°C at an average heating rate of 8°C / min, keep it warm for 90min, feed a mixture of nitrogen and hydrogen, and then The average heating rate of 1°C / min is raised to 760°C, and the temperature is kept for 210min;
[0024] (3) Slow cooling: the stator core in the annealing furnace is taken out of the furnace, air-cooled first, and then air-cooled to 320°C;
[0025] (4) Bluing: Place the slowly cooled stator core in a heating furnace, pass saturated water vapor into it for bluing treatment, cool with the furnace...
Embodiment 2
[0027] A kind of air-conditioning stator core heat treatment process that the present invention proposes comprises the following steps:
[0028] (1) Burning oil: Put the stator core in a heating furnace, raise the temperature from room temperature to 455°C under the condition of nitrogen gas, and keep it warm for 120 minutes to remove the stamping oil on its surface;
[0029] (2) Annealing: Place the deoiled stator core in an annealing furnace, raise the temperature to 725°C at an average heating rate of 8.5°C / min, keep it warm for 90min, and feed a mixture of nitrogen and hydrogen at a flow rate of 88m 3 / h, the volume ratio of nitrogen and hydrogen is 2:1, and then the temperature is raised to 755°C at an average heating rate of 1°C / min, and the temperature is kept for 210min;
[0030] (3) Slow cooling: take the stator core out of the annealing furnace, first air cool to 580°C, and then air cool to 330°C;
[0031] (4) Bluing: Place the cooled stator core in a heating furna...
Embodiment 3
[0033] A kind of air-conditioning stator core heat treatment process that the present invention proposes comprises the following steps:
[0034] (1) Burning oil: Put the stator core in a heating furnace, raise the temperature to 460°C under the condition of nitrogen gas, and keep it warm for 120 minutes to remove the stamping oil on its surface;
[0035] (2) Annealing: Place the deoiled stator core in an annealing furnace, raise the temperature to 730°C at an average heating rate of 9°C / min, keep it warm for 90min, and inject a mixture of nitrogen and hydrogen at a flow rate of 95m 3 / h, the volume ratio of nitrogen and hydrogen is 3:1, then the temperature is raised to 760°C at an average heating rate of 1.5°C / min, and the temperature is kept for 210min;
[0036] (3) Slow cooling: take the stator core out of the annealing furnace, first air cool to 590°C, and then air cool to 340°C;
[0037] (4) Bluing: Place the slowly cooled stator core in a heating furnace, and pass satu...
PUM
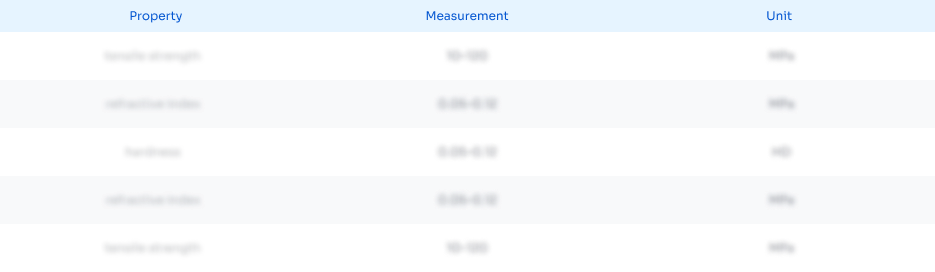
Abstract
Description
Claims
Application Information

- R&D
- Intellectual Property
- Life Sciences
- Materials
- Tech Scout
- Unparalleled Data Quality
- Higher Quality Content
- 60% Fewer Hallucinations
Browse by: Latest US Patents, China's latest patents, Technical Efficacy Thesaurus, Application Domain, Technology Topic, Popular Technical Reports.
© 2025 PatSnap. All rights reserved.Legal|Privacy policy|Modern Slavery Act Transparency Statement|Sitemap|About US| Contact US: help@patsnap.com