A manufacturing process of hot work die steel forgings
A technology of hot work die steel and preparation process, which is applied in the direction of metal processing equipment, etc., can solve the problems of coarse quenched martensite and affect the strength and toughness of modules, and achieve grain refinement, less dendrite segregation, and clean steel Effect
- Summary
- Abstract
- Description
- Claims
- Application Information
AI Technical Summary
Problems solved by technology
Method used
Image
Examples
Embodiment 1
[0062] Used steel ingot chemical composition (wt%) is as follows:
[0063] 0.385C; 1.183Si; 0.333Mn; 0.014P; 0.003S; 5.045Cr;
[0064] The process is as follows:
[0065] (1) Smelting
[0066] First use 40t electric arc furnace for smelting, then use 40t submerged arc heating ladle refining furnace to refine and vacuum degassed molten steel to pour ¢300mm consumable electrode, and use ¢300 consumable electrode to melt ¢300mm in electroslag remelting furnace 720 / ¢760mm, electroslag remelting steel ingot weighing about 5t.
[0067] (2) forging
[0068] Raise the electroslag remelted ingot to 650°C at a heating rate of 50°C / h for the first preheating, keep it for 2 hours, then raise the temperature at a rate of 80°C / h to 810°C for the second preheating, and hold it for 2 hours , and then raised to 1210°C at a heating rate of 110°C / h, held for 14 hours for high-temperature diffusion, started forging at 1100°C, three upsetting and three pulling out, upsetting ratio = 2, total f...
Embodiment 2
[0077] Used steel ingot chemical composition (wt%) is as follows:
[0078] 0.401C; 1.137Si; 0.350Mn; 0.012P; 0.003S; 5.104Cr;
[0079] The process is as follows:
[0080] (1) Smelting
[0081] First use 40t electric arc furnace for smelting, then use 40t submerged arc heating ladle refining furnace to refine and vacuum degassed molten steel to pour ¢300mm consumable electrode, and use ¢300 consumable electrode to melt ¢300mm in electroslag remelting furnace 720 / ¢760mm, electroslag remelting steel ingot weighing about 5t.
[0082] (2) forging
[0083] Raise the electroslag remelted ingot to 650°C at a heating rate of 50°C / h for the first preheating, keep it for 2 hours, then raise it to 820°C at a heating rate of 80°C / h for the second preheating, and hold it for 2 hours , and then raised to 1200°C at a heating rate of 100°C / h, held for 15 hours for high-temperature diffusion, started forging at 1100°C, three upsetting and three pulling out, upsetting ratio = 2, total forgin...
Embodiment 3
[0092] Used steel ingot chemical composition (wt%) is as follows:
[0093] 0.394C; 1.077Si; 0.370Mn; 0.010P; 0.002S; 5.207Cr;
[0094] The process is as follows:
[0095] (1) Smelting
[0096] First use 40t electric arc furnace for smelting, then use 40t submerged arc heating ladle refining furnace to refine and vacuum degassed molten steel to pour ¢300mm consumable electrode, and use ¢300 consumable electrode to melt ¢300mm in electroslag remelting furnace 720 / ¢760mm, electroslag remelting steel ingot weighing about 5t.
[0097] (2) forging
[0098] Raise the electroslag remelted ingot to 650°C at a heating rate of 50°C / h for the first preheating, keep it for 2 hours, then raise it to 810°C at a heating rate of 80°C / h for the second preheating, and hold it for 2 hours , and then raised to 1200°C at a heating rate of 100°C / h, held for 15 hours for high-temperature diffusion, started forging at 1100°C, three upsetting and three pulling out, upsetting ratio = 2, total forgin...
PUM
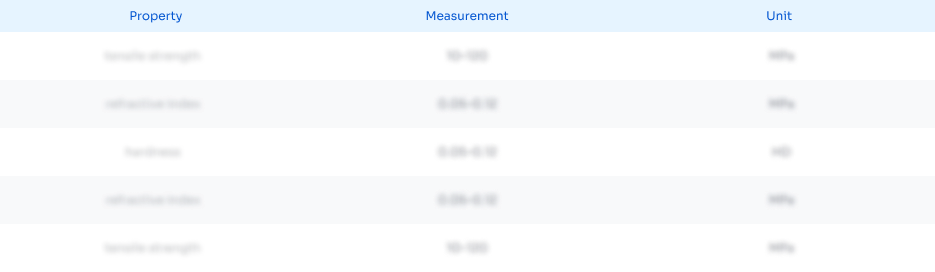
Abstract
Description
Claims
Application Information

- Generate Ideas
- Intellectual Property
- Life Sciences
- Materials
- Tech Scout
- Unparalleled Data Quality
- Higher Quality Content
- 60% Fewer Hallucinations
Browse by: Latest US Patents, China's latest patents, Technical Efficacy Thesaurus, Application Domain, Technology Topic, Popular Technical Reports.
© 2025 PatSnap. All rights reserved.Legal|Privacy policy|Modern Slavery Act Transparency Statement|Sitemap|About US| Contact US: help@patsnap.com