Phenyl hydrazine and substituted phenyl hydrazine continuous flow synthesis process
A synthesis process and flow synthesis technology, applied in the field of chemistry, can solve the problems of slow reaction rate, reduced product yield, production efficiency, low production efficiency, etc.
- Summary
- Abstract
- Description
- Claims
- Application Information
AI Technical Summary
Problems solved by technology
Method used
Image
Examples
Embodiment 1-20
[0143] Such as figure 1 As shown, raw material 1 (aniline acid feed liquid) and raw material 2 (concentration is 20% NaNO 2 Aqueous solution) is transported into the temperature zone 1 by a constant flow pump, and flows through the temperature zone 1 to complete the diazotization reaction. Raw material 3 (concentration is 19% Na 2 SO 3 aqueous solution) to temperature zone 2 for preheating, then mixed with the diazonium salt generated in temperature zone 1 in temperature zone 3, then flow through temperature zone 3 until the reaction is complete, and the reaction solution and raw material 4 (acid ) into the temperature zone 4 after mixing, and flow through the temperature zone 4 until the reaction is complete. The reaction mixture was collected, cooled and crystallized. After filtering and drying, the product phenylhydrazine salt can be obtained. The reaction parameters and results are as follows:
[0144] Table 1: Raw material ratio*:
[0145]
[0146]
[0147] *...
Embodiment 21-31
[0156] Such as figure 1 Shown, raw material 1 (o-fluoroaniline acid feed solution) and raw material 2 (concentration is 20% NaNO 2 Aqueous solution) is transported into the temperature zone 1 by a constant flow pump, and flows through the temperature zone 1 to complete the diazotization reaction. Raw material 3 (concentration is 19% Na 2 SO 3 aqueous solution) to temperature zone 2 for preheating, then mixed with the diazonium salt generated in temperature zone 1 in temperature zone 3, then flow through temperature zone 3 until the reaction is complete, and the reaction solution and raw material 4 (acid ) into the temperature zone 4 after mixing, and flow through the temperature zone 4 until the reaction is complete. The reaction mixture was collected, cooled and crystallized. After filtering and drying, the product o-fluorophenylhydrazine salt can be obtained. The reaction parameters and results are as follows:
[0157] Table 3: Raw material ratio*:
[0158]
[0159...
Embodiment 32-42
[0169] Such as figure 1 As shown, the raw material 1 (p-toluidine acid feed liquid) and the raw material 2 (concentration is 20% NaNO 2 Aqueous solution) is transported into the temperature zone 1 by a constant flow pump, and flows through the temperature zone 1 to complete the diazotization reaction. Use a constant flow pump to feed raw material 3 (20% NH 4 HSO 3 Aqueous solution) is transported to temperature zone 2 for preheating, then mixed with the diazonium salt generated in temperature zone 1 in temperature zone 3, then flows through temperature zone 3 until complete reaction, and the reaction liquid and raw material 4 (acid) in temperature zone 3 flow out After mixing, it enters temperature zone 4 and flows through temperature zone 4 until the reaction is complete. The reaction product was collected, cooled and crystallized. Filter and dry to obtain p-methylphenylhydrazine salt. The reaction parameters and results are as follows:
[0170] Table 5: Raw material ra...
PUM
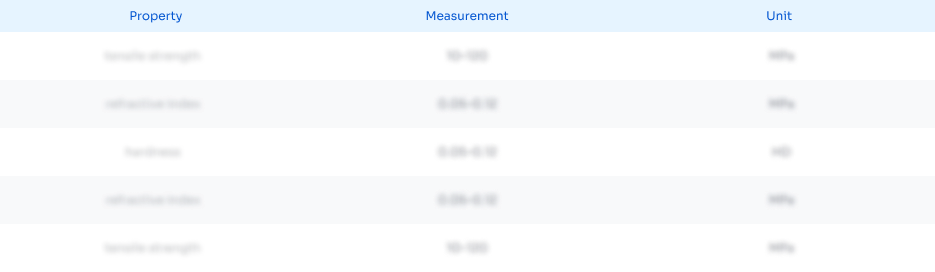
Abstract
Description
Claims
Application Information

- Generate Ideas
- Intellectual Property
- Life Sciences
- Materials
- Tech Scout
- Unparalleled Data Quality
- Higher Quality Content
- 60% Fewer Hallucinations
Browse by: Latest US Patents, China's latest patents, Technical Efficacy Thesaurus, Application Domain, Technology Topic, Popular Technical Reports.
© 2025 PatSnap. All rights reserved.Legal|Privacy policy|Modern Slavery Act Transparency Statement|Sitemap|About US| Contact US: help@patsnap.com