Self-lubricating diamond wire and production method thereof
A production method and technology of diamond wire, applied in the field of diamond wire, can solve the problems of high risk of wire breakage and increase cutting resistance, and achieve the effects of reducing the risk of wire breakage, increasing the resistance of lattice deformation, and enhancing the holding force of diamond
- Summary
- Abstract
- Description
- Claims
- Application Information
AI Technical Summary
Problems solved by technology
Method used
Image
Examples
Embodiment approach 1
[0041] (1) Pay-off: power pay-off, under constant speed of 5-10N tension
[0042] (2) Surface cleaning: After treatment with alkaline degreasing agent solution at 60±5°C, washing water, 10% sulfuric acid solution at 40±5°C and washing water respectively, the core wire with clean surface can be obtained;
[0043] (3) Surface pretreatment: The core wire that has been cleaned on the surface is deposited on the surface with a layer of nickel layer medium with high adhesion and fine grains through the flash nickel plating process. By adjusting the core wire speed, solution formula, current, pH value, Temperature, stirring and other parameters are used to adjust the grain size and thickness distribution of the nickel coating.
[0044] (4) Diamond attachment: diamond particles with a specification of 5 / 10 are attached to the surface of the core wire by electrochemical co-deposition technology.
[0045] (5) Diamond consolidation: connect the core wire with diamond particles to the ca...
Embodiment approach 2
[0051] The difference from Example 1 is that the self-lubricating material used is graphite fluoride, the additive used contains cetyltrimethylammonium chloride, the diamond particle size is 4 / 8, and other steps are the same as in Example 1.
Embodiment 3
[0053] The difference from Example 1 is that the self-lubricating material used is PTFE particles with an equivalent diameter of 10-1000 nanometers, and the specification of the diamond particles is 30 / 40. Other steps are all the same as in Example 1.
PUM
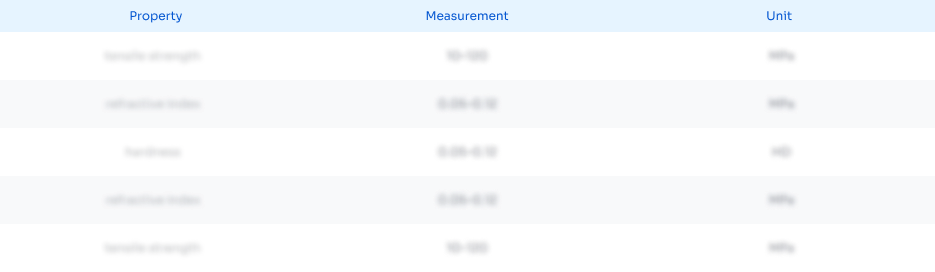
Abstract
Description
Claims
Application Information

- Generate Ideas
- Intellectual Property
- Life Sciences
- Materials
- Tech Scout
- Unparalleled Data Quality
- Higher Quality Content
- 60% Fewer Hallucinations
Browse by: Latest US Patents, China's latest patents, Technical Efficacy Thesaurus, Application Domain, Technology Topic, Popular Technical Reports.
© 2025 PatSnap. All rights reserved.Legal|Privacy policy|Modern Slavery Act Transparency Statement|Sitemap|About US| Contact US: help@patsnap.com