Polyformaldehyde composition and preparation method thereof
A polyoxymethylene composition and a technology for uniform mixing, applied in the field of polyoxymethylene composition and its preparation, can solve the problem that the tensile strength, flexural strength, flexural modulus, heat resistance and other properties are greatly reduced, and the polarity of the POM molecular chain is weak. , limiting the application of POM in the market, etc., to achieve the effect of simple preparation process, stable size and good impact resistance
- Summary
- Abstract
- Description
- Claims
- Application Information
AI Technical Summary
Problems solved by technology
Method used
Examples
Embodiment 1
[0033] Mix the weight ratio of POM 23%, ABS 74%, compatibilizer 2.2%, lubricant 0.4%, 168 0.2%, 1076 0.2% in the mixer; put the mixed raw materials into the twin-screw extruder The feeding hopper is melted and extruded, granulated, fully plasticized, melted, compounded, then extruded, drawn, cooled, pelletized, dried and packaged; the processing technology is as follows: Twin-screw extruder zone 160- 170℃, zone 2 160-180℃, zone 3 160-180℃, zone 4 170-190℃, zone 5 170-190℃, zone 6 160-180℃, zone 7 160-170℃, zone 8 160-170℃ ℃; the screw speed is controlled at 200-500 rpm; the residence time is 2-6 minutes.
Embodiment 2
[0035] Mix the weight ratio of POM 35%, ABS 60%, compatibilizer 4.2%, lubricant 0.4%, 168 0.2%, 1076 0.2% in the mixer; put the mixed raw materials into the twin-screw extruder The feeding hopper is melted and extruded, granulated, fully plasticized, melted, compounded, then extruded, drawn, cooled, pelletized, dried and packaged; the processing technology is as follows: Twin-screw extruder zone 160- 170℃, zone 2 160-180℃, zone 3 160-180℃, zone 4 170-190℃, zone 5 170-190℃, zone 6 160-180℃, zone 7 160-170℃, zone 8 160-170℃ ℃; the screw speed is controlled at 200-500 rpm; the residence time is 2-6 minutes.
Embodiment 3
[0037] Mix the weight ratio of POM 60%, ABS 35%, compatibilizer 4.2%, lubricant 0.6%, 168 0.2%, 1076 0.2% in the mixer; put the mixed raw materials into the twin-screw extruder The feeding hopper is melted and extruded, granulated, fully plasticized, melted, compounded, then extruded, drawn, cooled, pelletized, dried and packaged; the processing technology is as follows: Twin-screw extruder zone 160- 170℃, zone 2 160-180℃, zone 3 160-180℃, zone 4 170-190℃, zone 5 170-190℃, zone 6 160-180℃, zone 7 160-170℃, zone 8 160-170℃ ℃; the screw speed is controlled at 200-500 rpm; the residence time is 2-6 minutes.
PUM
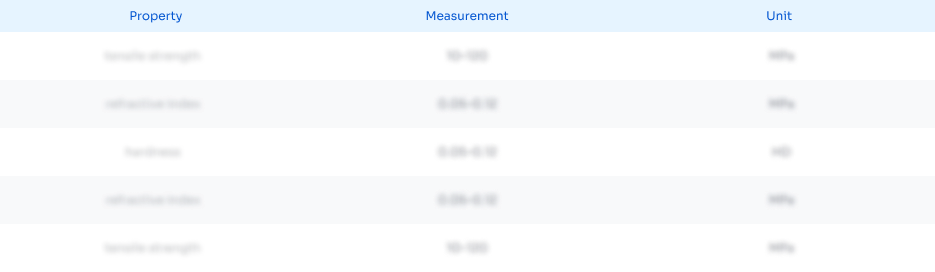
Abstract
Description
Claims
Application Information

- R&D
- Intellectual Property
- Life Sciences
- Materials
- Tech Scout
- Unparalleled Data Quality
- Higher Quality Content
- 60% Fewer Hallucinations
Browse by: Latest US Patents, China's latest patents, Technical Efficacy Thesaurus, Application Domain, Technology Topic, Popular Technical Reports.
© 2025 PatSnap. All rights reserved.Legal|Privacy policy|Modern Slavery Act Transparency Statement|Sitemap|About US| Contact US: help@patsnap.com