Molding process for roller bearing retainer of railway carriage
A molding process and roller bearing technology, applied in the field of cages, can solve the problems of high risk of manual operation, unidirectional operation of steel cages, large molding shrinkage, etc., to achieve simple and reasonable technical solutions, clean and safe production process , Processability and light weight effect
- Summary
- Abstract
- Description
- Claims
- Application Information
AI Technical Summary
Problems solved by technology
Method used
Examples
specific Embodiment
[0012] A specific embodiment of the present invention: a molding process for a roller bearing cage of a railway passenger car. The molding process steps are: glass fiber reinforced polyamide plastics are used as raw materials, a dehumidifying dryer is used to dry the raw materials, and then the raw materials are dried. The granular plastic is transported to the hopper of the screw-type plastic injection molding machine, and sent to the heated barrel by the screw, so that it is heated and melted to a fluid state. Under high-pressure injection, the molten plastic is compressed and moves forward quickly, and is ejected from the nozzle , Inject into the engineering plastic cage mold, after cooling and shaping, open the mold to take out the product.
[0013] The specific forming process steps are as follows:
[0014] (1) Drying of raw materials
[0015] Glass fiber reinforced polyamide plastic (nylon) is a kind of hygroscopic plastic because it contains hydrophilic amide group in the m...
PUM
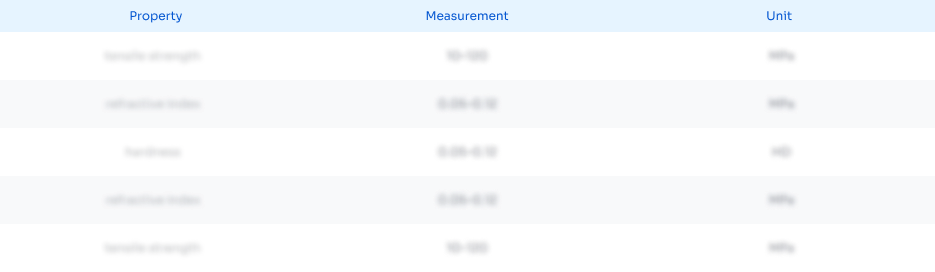
Abstract
Description
Claims
Application Information

- Generate Ideas
- Intellectual Property
- Life Sciences
- Materials
- Tech Scout
- Unparalleled Data Quality
- Higher Quality Content
- 60% Fewer Hallucinations
Browse by: Latest US Patents, China's latest patents, Technical Efficacy Thesaurus, Application Domain, Technology Topic, Popular Technical Reports.
© 2025 PatSnap. All rights reserved.Legal|Privacy policy|Modern Slavery Act Transparency Statement|Sitemap|About US| Contact US: help@patsnap.com