Triblock polycarboxylic acid water reducing agent and preparation method thereof
A polycarboxylic acid and triblock technology, applied in the field of preparation of triblock polycarboxylate water reducing agent, can solve the problems of poor sulfate resistance, small slump loss, fast slump loss and the like
- Summary
- Abstract
- Description
- Claims
- Application Information
AI Technical Summary
Problems solved by technology
Method used
Image
Examples
Embodiment 1
[0066] 15g polyethylene glycol monomethyl ether methacrylate (Mn=500g / mol), 0.17g S, S'-p-(α,α'-dimethyl-α"-acetic acid) trithiocarbonate and After 0.02g of azobisisobutylamidine hydrochloride and 35g of water are fully mixed, feed N 2 O in the solution 2 discharge, the N 2 The reversible addition-fragmentation chain transfer polymerization reaction is carried out under protection, the reaction temperature is 60°C, the reaction time is 10h, the conversion rate of monomer X is 97.07%, and the unreacted monomer and small molecules are removed by dialysis to obtain the polyether Macromonomer-RAFT reagent (Mw=12.14kDa), add 2.05g acrylic acid (45.83% conversion rate), 0.24g sodium methacrylate (43.19% conversion rate) and continue polymerization for 12h to obtain triblock polycarboxylic acid Aqueous mother liquor (Mw=13.47kDa).
Embodiment 2
[0068] Mix 15g polyethylene glycol monomethyl ether acrylate (Mn=500g / mol), 0.11g S, S'-p-(α,α'-dimethyl-α"-acetic acid) trithiocarbonate with 0.01g After azobisisobutylamidine hydrochloride and 35g water are fully mixed, pass into N 2 O in the solution 2 discharge, the N 2 The reversible addition-fragmentation chain transfer polymerization reaction was carried out under protection, the reaction temperature was 80°C, the reaction time was 4h, the conversion rate of monomer X was 97.34%, and the unreacted monomer and small molecules were removed by dialysis to obtain the polyether macro Monomer-RAFT reagent (Mw=19.43kDa), add 4.64g methacrylic acid (47.84% conversion rate), 0.86g sodium propylene sulfonate (47.69% conversion rate) and continue polymerization for 5h to obtain triblock polycarboxylic acid dehydrated Agent stock solution (Mw=25.87kDa).
Embodiment 3
[0070] 28.5g polyethylene glycol monomethyl ether methacrylate (Mn=950g / mol), 0.32g S, S'-p-(α,α'-dimethyl-α"-acetic acid) trithiocarbonate After fully mixing with 0.03g 4,4'-azobis(4-cyanovaleric acid) and 66.5g water, pass N 2 O in the solution 2 discharge, the N 2 The reversible addition-fragmentation chain transfer polymerization reaction was carried out under protection, the reaction temperature was 70°C, the reaction time was 8 hours, the conversion rate of monomer X was 97.62%, and the unreacted monomer and small molecules were removed by dialysis to obtain polyether macro Monomer-RAFT reagent (Mw=12.48kDa), add 3.89g acrylic acid (48.56% conversion rate), 0.94g sodium methacrylate (47.04% conversion rate) and continue to polymerize for 5h to obtain three-block polycarboxylic acid dehydrated Agent stock solution (Mw=14.26kDa).
PUM
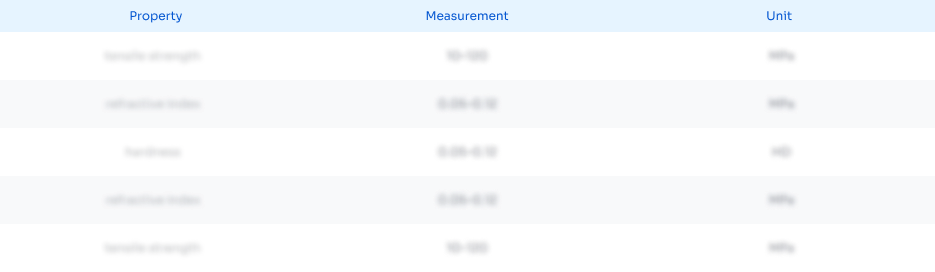
Abstract
Description
Claims
Application Information

- Generate Ideas
- Intellectual Property
- Life Sciences
- Materials
- Tech Scout
- Unparalleled Data Quality
- Higher Quality Content
- 60% Fewer Hallucinations
Browse by: Latest US Patents, China's latest patents, Technical Efficacy Thesaurus, Application Domain, Technology Topic, Popular Technical Reports.
© 2025 PatSnap. All rights reserved.Legal|Privacy policy|Modern Slavery Act Transparency Statement|Sitemap|About US| Contact US: help@patsnap.com