Quaternary ammonium salt modified organosilicon polyurethane ocean antifouling paint and preparation method and application thereof
A marine antifouling, quaternary ammonium salt technology, applied in the direction of polyurea/polyurethane coatings, antifouling/underwater coatings, coatings, etc. The effect of adsorption and avoidance
- Summary
- Abstract
- Description
- Claims
- Application Information
AI Technical Summary
Problems solved by technology
Method used
Image
Examples
Embodiment 1
[0032] 1) React 47.9g of chloropropylmethyldichlorosilane and 4.5g of water in the organic solvent ether for 3 hours, wash with water until neutral, dry with anhydrous calcium chloride, remove the organic solvent ether by distillation at atmospheric pressure, and distill under reduced pressure to obtain 2 ,4,6-tris(3-chloropropyl)-2,4,6-trimethyl-cyclotrisiloxane;
[0033] 2) Dissolve 40.50g of allyl glycidyl ether in toluene, add 20 μL of catalyst chloroplatinic acid, raise the temperature to 80°C, slowly add 46.85g of tetramethyldisiloxane dropwise under stirring, and continue the reaction at 120°C for 6 h Afterwards, underpressure distillation obtains 1,3-bis[3-(2,3-epoxypropoxy)propyl]-tetramethyldisiloxane;
[0034] 3) Mix 13g of 1,3-bis[3-(2,3-epoxypropoxy)propyl]-tetramethyldisiloxane and 58g of methanol, and add 20μL of trifluoromethyl under N2 protection Sulfonic acid, after reacting at 70°C under reflux for 6 hours, adjust the pH to 7, continue the reaction for 1 ho...
Embodiment 2
[0039] 1) React 47.9g of chloropropylmethyldichlorosilane and 18g of water in the organic solvent ether for 3 hours, wash with water until neutral, dry with anhydrous calcium chloride, remove the organic solvent ether by distillation at atmospheric pressure, and distill under reduced pressure to obtain 2, 4,6-tris(3-chloropropyl)-2,4,6-trimethyl-cyclotrisiloxane;
[0040] 2) Dissolve 40.50g of allyl glycidyl ether in toluene, add 20 μL of catalyst chloroplatinic acid, raise the temperature to 80°C, slowly add 46.85g of tetramethyldisiloxane dropwise under stirring, and continue the reaction at 120°C for 6 h Afterwards, underpressure distillation obtains 1,3-bis[3-(2,3-epoxypropoxy)propyl]-tetramethyldisiloxane;
[0041] 3) Mix 13g of 1,3-bis[3-(2,3-epoxypropoxy)propyl]-tetramethyldisiloxane and 58g of methanol, and add 20μL of trifluoromethyl under N2 protection Sulfonic acid, after reacting at 70°C under reflux for 6 hours, adjust the pH to 7, continue the reaction for 1 hou...
Embodiment 3
[0046] 1) React 47.9g of chloropropylmethyldichlorosilane and 18g of water in the organic solvent ether for 3 hours, wash with water until neutral, dry with anhydrous calcium chloride, remove the organic solvent ether by distillation at atmospheric pressure, and distill under reduced pressure to obtain 2, 4,6-tris(3-chloropropyl)-2,4,6-trimethyl-cyclotrisiloxane;
[0047] 2) Dissolve 40.50 g of allyl glycidyl ether in toluene, add 20 μL of catalyst chloroplatinic acid, raise the temperature to 80 °C, slowly add 20.30 g of tetramethyldisiloxane dropwise under stirring, and continue the reaction at 120 °C for 6 h Afterwards, underpressure distillation obtains 1,3-bis[3-(2,3-epoxypropoxy)propyl]-tetramethyldisiloxane;
[0048] 3) Mix 13g of 1,3-bis[3-(2,3-epoxypropoxy)propyl]-tetramethyldisiloxane and 58g of methanol, and add 20μL of trifluoromethyl under N2 protection Sulfonic acid, after reacting at 70°C under reflux for 6 hours, adjust the pH to 7, continue the reaction for 1...
PUM
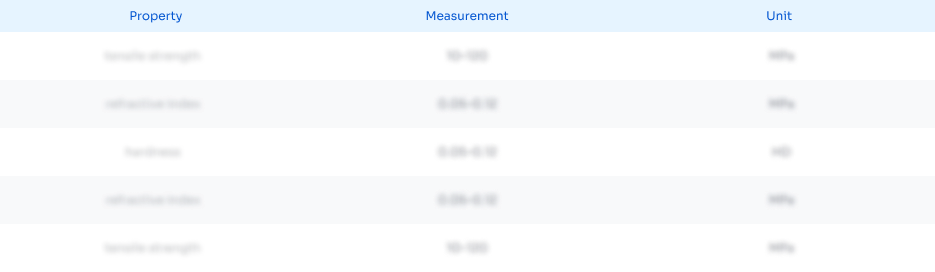
Abstract
Description
Claims
Application Information

- R&D
- Intellectual Property
- Life Sciences
- Materials
- Tech Scout
- Unparalleled Data Quality
- Higher Quality Content
- 60% Fewer Hallucinations
Browse by: Latest US Patents, China's latest patents, Technical Efficacy Thesaurus, Application Domain, Technology Topic, Popular Technical Reports.
© 2025 PatSnap. All rights reserved.Legal|Privacy policy|Modern Slavery Act Transparency Statement|Sitemap|About US| Contact US: help@patsnap.com