Sulfuric acid anodizing method for 7050 aluminum alloy
An anodizing, aluminum alloy technology, applied in anodizing, electrolytic coating, surface reaction electrolytic coating, etc., can solve the problem of sulfuric acid anodizing process, and achieve the effect of high cost and long order cycle
- Summary
- Abstract
- Description
- Claims
- Application Information
AI Technical Summary
Problems solved by technology
Method used
Image
Examples
example 1
[0081] Wipe the 7050-T7451 ultra-thick plate aluminum alloy with methyl ethyl ketone; immerse it in 55g / L alkali cleaning solution (TURCO4215NCLT cleaning agent solution) at 52°C for 8 minutes, then wash it with water for 4 minutes; observe the continuous water film on the surface of the aluminum alloy and then carry out pickling ; In the pickling solution at room temperature (the mixed solution of chromic anhydride, nitric acid, hydrofluoric acid and deionized water), the concentration of chromic anhydride is 25.2g / L, the concentration of nitric acid is 96g / L, and the corrosion rate is 23.6 microns / unit surface / hour, etch for 2.5 minutes, wash with water for 5 minutes; put the pretreated aluminum alloy parts in an anodic oxidation solution: sulfuric acid 212g / L, temperature 22°C, current density 1.4A / dm 2 , Oxidation for 30min. A pure lead plate is used as the cathode, and compressed air is used to stir during the anodizing process. After oxidation, wash with water for 4 min...
example 2
[0084] Wipe the 7050-T7451 ultra-thick plate aluminum alloy with methyl ethyl ketone; immerse it in 52g / L alkali cleaning solution (TURCO4215NCLT cleaning agent solution) at 53°C for 10 minutes, then wash it with water for 5 minutes; observe the continuous water film on the surface of the aluminum alloy and then carry out pickling ; In the pickling solution at room temperature (the mixed solution of chromic anhydride, nitric acid, hydrofluoric acid and deionized water), the concentration of chromic anhydride is 24.9g / L, the concentration of nitric acid is 93g / L, and the corrosion rate is 23.5 microns / unit Surface / hour, etching for 2 minutes, washing with water for 4 minutes; put the pretreated aluminum alloy parts in an anodic oxidation solution: sulfuric acid 210g / L, temperature 21°C, current density 1.3A / dm 2 , Oxidation for 35min. A pure lead plate is used as the cathode, and compressed air is used to stir during the anodizing process. After oxidation, wash with water for ...
example 3
[0087] After wiping the 7050-T7451 ultra-thick plate aluminum alloy with methyl ethyl ketone; immerse it in 49g / L alkali cleaning solution (TURCO4215NCLT cleaning agent solution) at 51°C for 9 minutes, then wash it with water for 4 minutes; observe the continuous water film on the surface of the aluminum alloy and then carry out pickling ; In the pickling solution at room temperature (the mixed solution of chromic anhydride, nitric acid, hydrofluoric acid and deionized water), the concentration of chromic anhydride is 23.9g / L, the concentration of nitric acid is 92g / L, and the corrosion rate is 23.2 microns / unit surface / hour, etch for 3 minutes, wash with water for 5 minutes; put the pretreated aluminum alloy parts in an anodic oxidation solution: sulfuric acid 208g / L, temperature 20°C, current density 1.2A / dm 2 , oxidation for 40min. A pure lead plate is used as the cathode, and compressed air is used to stir during the anodizing process. After oxidation, wash with water for...
PUM
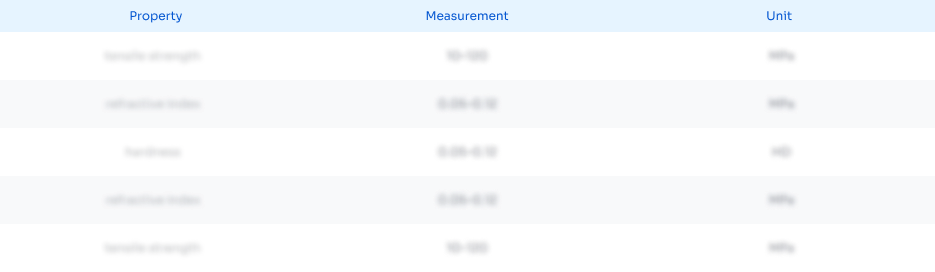
Abstract
Description
Claims
Application Information

- R&D Engineer
- R&D Manager
- IP Professional
- Industry Leading Data Capabilities
- Powerful AI technology
- Patent DNA Extraction
Browse by: Latest US Patents, China's latest patents, Technical Efficacy Thesaurus, Application Domain, Technology Topic, Popular Technical Reports.
© 2024 PatSnap. All rights reserved.Legal|Privacy policy|Modern Slavery Act Transparency Statement|Sitemap|About US| Contact US: help@patsnap.com