Preparation method for Al2O3p / Mo alloy
An al2o3p, alloy technology, applied in the field of molybdenum-based alloys, can solve the problem that the preparation method is not suitable for large-scale mass production, etc., and achieves improved high-temperature recrystallization temperature, anti-wear and anti-arc ablation properties, high hardness, and good wear resistance. Effect
- Summary
- Abstract
- Description
- Claims
- Application Information
AI Technical Summary
Problems solved by technology
Method used
Examples
Embodiment 1
[0027] Al in this example 2 o 3p / Mo alloy, the volume percentage composition is Al 2 o 3 0.05%, the balance being Mo, prepared by the following method:
[0028] 1) Weigh 4000g of ammonium tetramolybdate and put it into a resistance furnace for calcination, calcine at 520°C for 4h, and pass through a 40-mesh sieve to obtain MoO 3 Powder;
[0029] 2) In an autoclave with a capacity of 250ml, add 8.5g of aluminum nitrate and 2.5g of urea respectively, add 10ml of glycerol as template agent and dispersant, then add distilled water, the filling degree is 80%, and heat the autoclave to 180 ℃, keep warm for 20h, and obtain AlOOH nanoparticle suspension with good dispersion after cooling;
[0030] 3) MoO 3 Put the powder into a ball mill tank, dry mill for 8 hours, then pour the AlOOH nanoparticle suspension prepared in step 2), add 1000ml of water and 500ml of absolute ethanol, wet mill for 8 hours, then dry at 140°C for 24 hours, pass 40 AlOOH / MoO prepared by mesh sieve 3 ...
Embodiment 2
[0035] Al in this example 2 o 3p / Mo alloy, the volume percentage composition is Al 2 o 3 0.4%, the balance being Mo, prepared by the following method:
[0036] 1) Weigh 4000g of ammonium tetramolybdate and put it into a resistance furnace for calcination, calcine at 510°C for 3 hours, pass through a 40-mesh sieve to obtain MoO 3 Powder;
[0037] 2) In an autoclave with a capacity of 250ml, add 68.0g of aluminum nitrate and 20.0g of urea respectively, add 20ml of glycerol as template agent and dispersant, then add distilled water, the filling degree is 80%, and heat the autoclave to 160 ℃, keep warm for 25h, and obtain AlOOH nanoparticle suspension with good dispersion after cooling;
[0038] 3) MoO 3 Put the powder into a ball mill jar, dry mill for 10 hours, then pour the AlOOH nanoparticle suspension prepared in step 2), add 1000ml of water and 500ml of absolute ethanol, wet mill for 10 hours, then dry at 160°C for 24 hours, and pass 40 AlOOH / MoO prepared by mesh si...
Embodiment 3
[0043] Al in this example 2 o 3p / Mo alloy, the volume percentage composition is Al 2 o 3 0.25%, and the balance is Mo, prepared by the following method:
[0044] 1) Weigh 4000g of ammonium dimolybdate and put it into a resistance furnace for calcination, calcine at 500°C for 5h, and pass through a 40-mesh sieve to obtain MoO 3 Powder;
[0045] 2) In an autoclave with a capacity of 250ml, add 14.77g of aluminum chloride and 5g of urea respectively, add 40ml of glycerol as template agent and dispersant, then add distilled water, the filling degree is 80%, and heat the autoclave to 170 ℃, keep warm for 22h, and obtain AlOOH nanoparticle suspension with good dispersion after cooling;
[0046] 3) MoO 3 Put the powder into a ball mill jar, dry mill for 9 hours, then pour the AlOOH nanoparticle suspension prepared in step 2), then add 1000ml of water and 500ml of absolute ethanol, wet mill for 9 hours, then dry at 180°C for 24 hours, and pass 40 AlOOH / MoO prepared by mesh si...
PUM
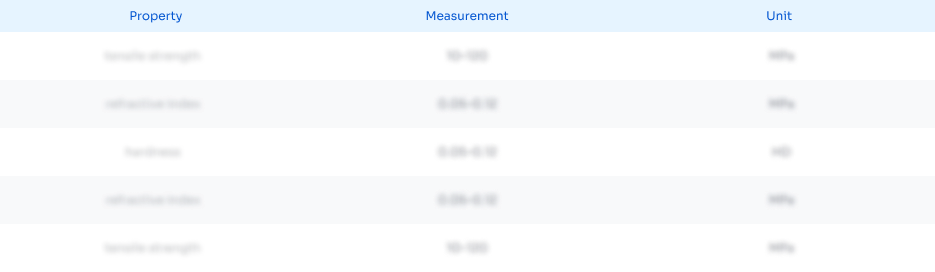
Abstract
Description
Claims
Application Information

- R&D Engineer
- R&D Manager
- IP Professional
- Industry Leading Data Capabilities
- Powerful AI technology
- Patent DNA Extraction
Browse by: Latest US Patents, China's latest patents, Technical Efficacy Thesaurus, Application Domain, Technology Topic, Popular Technical Reports.
© 2024 PatSnap. All rights reserved.Legal|Privacy policy|Modern Slavery Act Transparency Statement|Sitemap|About US| Contact US: help@patsnap.com